AUTOMATION UNIVERSITY
Automated Assembly System Roundup
Wheels, switches and drivetrain components are among the myriad items made on automated assembly systems.
John Sprovieri // Chief Editor // sprovierij@bnpmedia.com
Photo: SweetBunFactory via iStock / Getty Images Plus
The previous articles in this ebook have provided an overarching view of automated assembly systems. They’ve discussed how to specify and debug systems. They’ve talked about how to feed parts and how to collect and analyze assembly data.
Here, then, are some examples of how all that preparation can pay off. The following systems exemplify the hard work and ingenuity that routinely go into today’s automated assembly systems.
Robotic System Packages, Palletizes Automotive Wheels
Through the first six months of 2023, U.S. sales of light vehicles topped 7.68 million units, an increase of 13 percent compared with the first six months of 2022, according to market research firm GlobalData. Depending on the outcome of the UAW’s strike against the Detroit Three automakers, sales for the year could range from 15.1 million to 15.4 million units, an increase of 9 to 11 percent over last year.
If that holds true, automakers will need more than 61 million wheels this year, and that doesn’t count aftermarket replacements and upgrades. That’s a lot of wheels.
Satisfying that kind of demand requires automation. Hyperion Automation of Holland, MI, knows all about it. Recently, the systems integrator designed and built an automated packing cell for a wheel manufacturer.
Automation was necessary in the wake of several challenges. Labor shortages made it difficult to find and retain talent for the packing line, which ran around the clock. The wheels were heavy. Without the tire, a metal wheel typically weighs 30 pounds. Moving them from the end of the processing line to packing line required strength and care—while still maintaining the throughput rate.
However, automating the cell would not be easy. For one thing, different wheels required different pallets, dividers and protective polyfoam sheets. The system’s robots and conveyors would need to be precise, but flexible enough to handle all types of materials.
Space was also a concern. The shop floor only had so much space to house automation. The cells had to be large enough to allow access for employees to add new pallets and materials with fork trucks or perform maintenance on the machines.
The packing cell required numerous interface points. Space was needed for fork trucks to get in and out; operators to move rejected wheels and pallets out of the cell; operators to move 48-inch polyfoam rolls into the cell; operators to maintain the robots; and empty pallets and newly finished wheels to come in via conveyors.
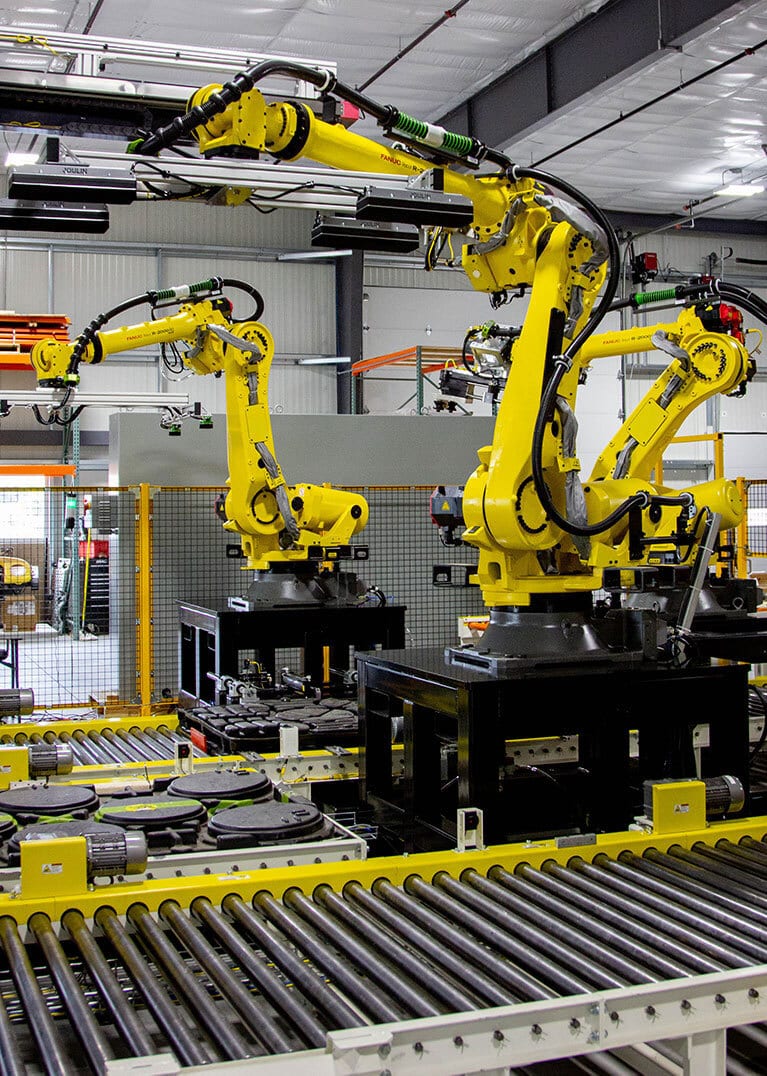
A six-axis robot handles wheels of every size and weight. Photo courtesy Hyperion Automation
Hyperion’s cell meets all these requirements. A roller conveyor transports wheels from the production lines to the packing cell. A second roller conveyor moves loaded pallets out of the cell to shipping. The conveyors are designed to transport all sizes of wheels, pallets and dunnage. The conveyor uses pallet stops to align the pallet along the front edge of the cell. A “crowder” mechanism pushes it into alignment on the side.
A six-axis robot handles wheels of every size and weight. The robot gently picks up a wheel from a conveyor and places it accurately on a pallet at a consistent rate.
As wheels pass through the initial conveyor, a vision system scans the wheels to verify wheel size and type, ensuring consistency and correct packaging materials.
A second vision system guides the robots, identifying divider types as they convey into the cell. The vision system then scans the entire pallet to verify the correct dunnage type for the wheels being loaded, while also capturing positional data on X, Y, Z and angular offsets to successfully pick and place each divider. The system prevents the wrong dividers or bases from being used.
A polyfoam sheeter automatically cuts the material to length on demand. This saves on the cost of precut material and the labor required to manually place the sheets between rows of wheels. The automated sheeter can also switch sheet size on demand to accommodate five to eight pallet sizes.
In the final step of the process, the pallet is conveyed out of the cell and into an automated bander system. Previously, the banding machine required an operator to line up the pallet and then push a button to band it. The new fully automated machine completes the work without the need for an additional worker.
To see a video of the system in operation, click here. For more information on automation, visit the company’s website: https://hyperionautomation.com.
Robotic Assembly Line Increases Production Fivefold
ABB’s Smart Power business unit is the global market leader for low-voltage switches. The company’s assembly plant in Vaasa, Finland, produces a wide range of low-voltage switches for solar, auxiliary power, IT and industrial use.
The factory turned to JOT Automation to design and build a custom automated assembly system that could increase production volume; handle multiple product variants; and meet high quality standards.
Before getting down to automation, JOT engineers broke down the initial setup into steps and identified where potential challenges might arise. Then, they designed and built the line.
JOT’s fully automated assembly system can run two product families with up to 40 different variants. Capable of semi-autonomous production, the system increased throughput by a factor of five.
With a full load of parts, the system can run autonomously for up to two hours. A sophisticated vision system enables six-axis robots to handle components reliably with a cycle time of less than 30 seconds. Components are chosen dynamically based on the orders given by the plant’s manufacturing execution system.
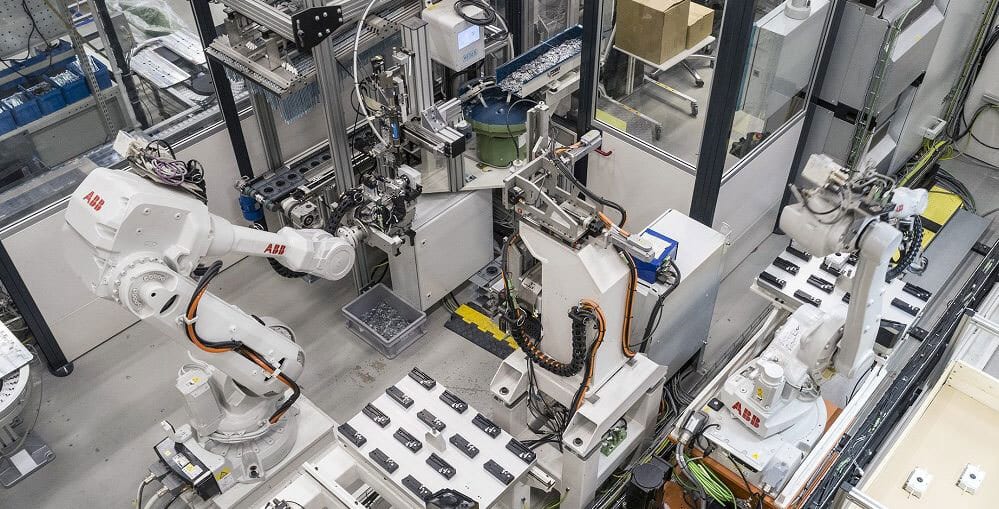
Six-axis robots assemble low-voltage switches at ABB’s assembly plant in Vaasa, Finland. Photo courtesy JOT Automation
Assembly is handled dynamically at various stations. These stations include pick and place operations, screwdriving, and labeling for 100 percent traceability throughout the production process. The line is also equipped with both mechanical and electrical testing stations.
After testing, the switches are placed on an outgoing conveyor for transport to a packaging station and shipping.
“Together with JOT, we created a system that allows us to fully automate our production,” says Juha Sohlberg, senior project manager at ABB. “We required a supplier that can meet demanding requirements while providing industry-leading reliability and quality.
“With this custom line, we have been able to increase our throughput while maintaining production flexibility.”
To see a video of the line, click here. For more information on automated assembly and test equipment, click www.jotautomation.com.
Robots Assemble Drivetrain Components
When a leading manufacturer of automotive drivetrain components was presented with an opportunity to grow its business, the company approached PrimeTest Automation to analyze its current production process and develop a system that could meet its new production volume requirements.
The company’s current process had been in place for more than 20 years and relied heavily on a labor-intensive, manual process. A trained operator was producing a finished part every 2 minutes, requiring two operators to meet a production volume of 80,000 units per year. With volumes projected to increase to 400,000 units annually, the company would need at least seven workers to keep pace.
Additionally, because components were assembled manually, the likelihood of inconsistencies in the final product and overall quality issues would be higher than with an automated process. It would also make production planning more difficult.
Overall, the process was inefficient and needed to be updated with modern production techniques. PrimeTest was up to the challenge. Drawing on its experience with robotics, vision inspection, controls and small-part handling, PrimeTest developed a more efficient, automated process.
The system features two Fanuc LR Mate 200iD robots for material handling and machine tending. These robots move the customer’s product through a series of process operations involving material blanking and bonding, and then through final vision inspection utilizing a Keyence IV-500MA vision sensor.
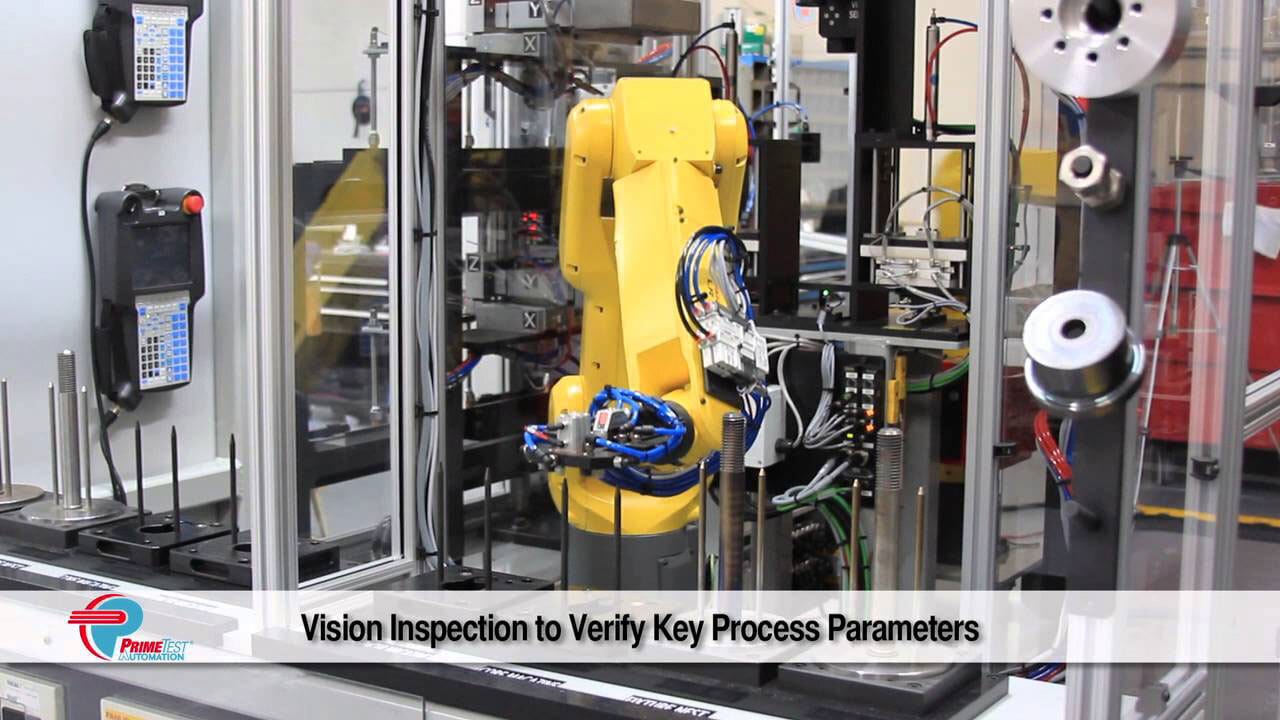
This robotic assembly system can produce some 400,000 drivetrain components annually. Photo courtesy PrimeTest Automation
Although PrimeTest’s headquarters is located more than 1,000 miles away from the manufacturer’s facility, a VPN device integrated into the machine’s control system enables the integrator’s engineers to support the customer’s operation remotely. With this remote access, PrimeTest engineers can access more than 17 Ethernet devices within the system. These devices include programmable safety devices, programmable logic controllers, servo and stepper drives, vision systems, and remote I/O modules.
The robotic assembly system increased output to 3.75 units per minute, meeting the customer’s projected volumes with just one operator tending the system. In addition, the automated process assembles a more consistent final product.
To see a video of the line, click here. For more information on automated assembly and test equipment, click www.primetest.com.
Cam-based Chassis Assemble Consumer Product
ATC Automation has more than four decades of experience providing automated assembly systems for consumer products manufacturers.
Recently, the integrator was called upon to design and build a fully automatic system to assemble a multicomponent residential electrical product. The high-speed system consists of two cam-based chassis. The subassembly of this product begins on an eight-station Weiss rotary assembly dial. The subassembly is then transported to a Stelron precision-link conveyor, where final assembly and test is completed. The system is integrated with a variety of parts feeders, intelligent screwdrivers, precision dispensing valves, and welding equipment. Quality checks are performed throughout the process using sensors and vision systems.
When the assembly is complete and all quality checks are verified, the assemblies are fed directly to a third-party packaging system. The assemblies are kitted and boxed by the packaging system. ATC supplied a palletizing system that uses a Fanuc robot to stack boxes onto a pallet.
For more information on automated assembly and test equipment, click https://atcautomation.com.
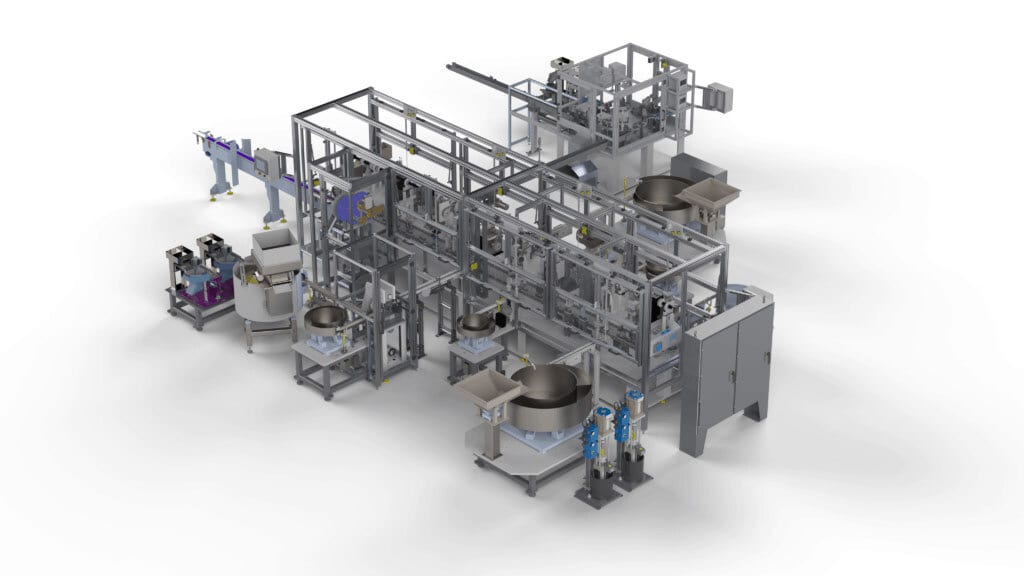
This automation system assembles a multicomponent residential electrical product. Photo courtesy ATC Automation
ASSEMBLY ONLINE
For more information on assembly automation, visit www.assemblymag.com to read these articles: