Heating with Purpose: How Geneva United Methodist Church in Geneva, Illinois Chose Geothermal for the Earth and Their Community
By David Buss, Geothermal Product Manager at Connor Company
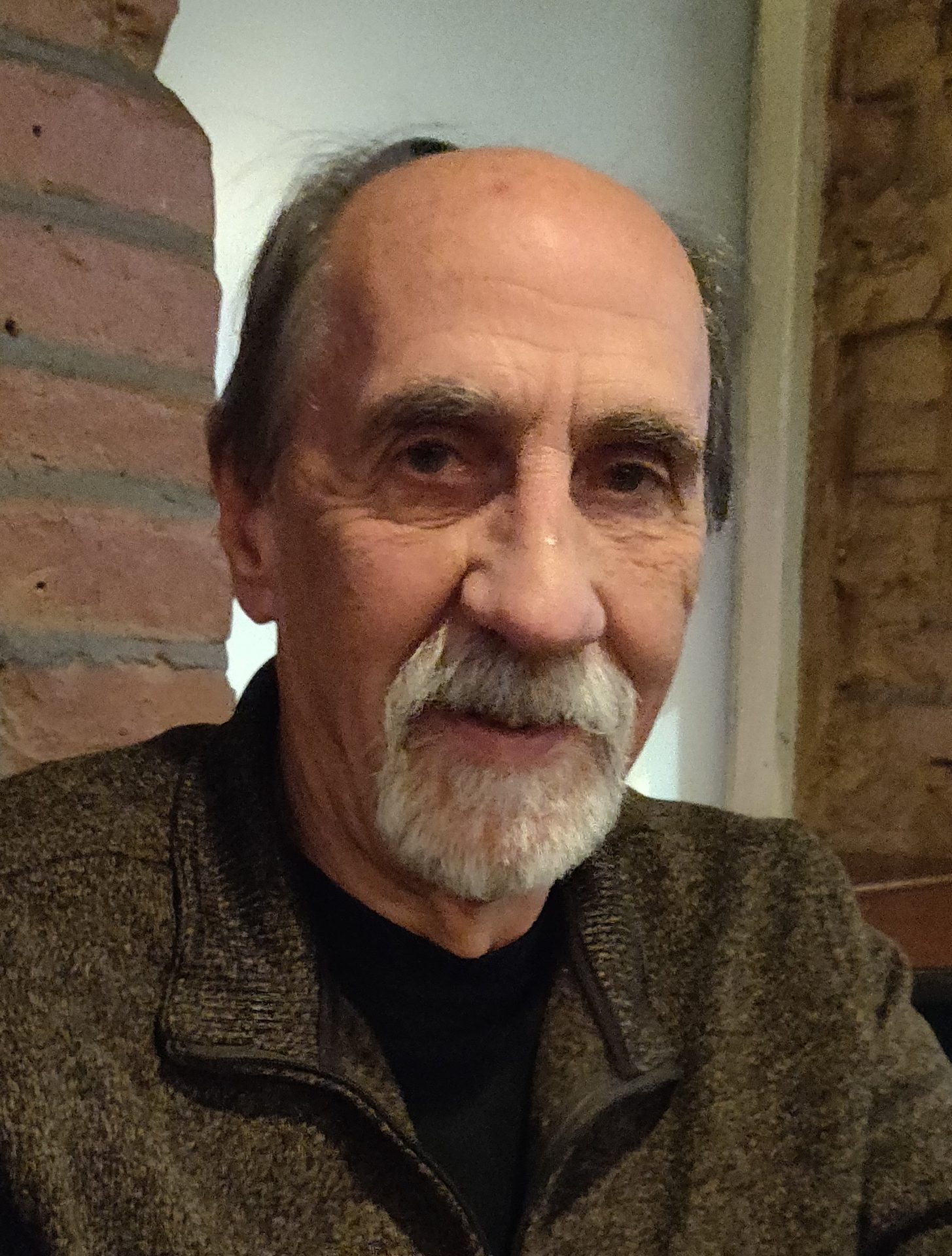
Existing System and Situation
The original church building was constructed in 1874, and the original furnace was coal fired and later changed to use natural gas. It completely filled 2 rooms in the basement of the original building with one room actually part of the return air plenum. As the contractors worked there, they all called it “the beast”, not exactly the picture of energy efficiency. Like many churches there were several additions added to the original building over the years, which included additions to the HVAC system. An education wing was added in 1990 and heated and cooled with several gas-fired rooftop units and a couple of residential furnaces with A/C.
A major addition and renovation in 1997 added to a new sanctuary and office area adjacent to the original building. It was conditioned with additional rooftop units and a 50-ton split system A/C unit for the sanctuary and 4 horizontal gas-fired duct furnaces for heating. There was a nice large mechanical room in an attic space of the new addition for these mechanical systems, but it included a 4’ X 6’ opening with loose fitting louvre for combustion air and 2 similar sized openings for ventilation air. There were controls on the ventilation air, but not functioning properly so that a very large amount of outside air was always being introduced into the building.
This excessive amount of outside air was a major source of problems that they were experiencing with humidity, way too much in summer and none in the winter. In an effort to add humidity there had been humidifiers added to the duct furnaces, which had then rusted out and been ruined over the years. The pipe organ had to be serviced frequently to address the dry conditions in the winter and the excess humidity in the summer.
The total heating capacity of all the rooftop units, individual furnaces, and 4 duct furnaces was well over 1,000,000 million BTU/HR. A/C capacity was 106 tons. An energy study and resulting model indicated that the system was grossly over-sized, largely because of the excessive outside air and infiltration, along with the sizing tendencies of the times.
Requests of the congregation
At our first meetings, the congregation indicated that they wanted to be a positive example to the community for environmental concerns and show their commitment to stewardship of the earth as well as find solutions to their many HVAC problems. There had been some individual experiences with geothermal in residential applications and they decided that they wanted to explore that option for their church.
Solutions
The contractor, Advanced Geothermal, and I worked together to provide a Design-Build solution for the church. Advanced Geothermal has been in the business of geothermal installations and loop installations for over 25 years in the Chicago area, and we have worked together for all that time.
We proposed a Geothermal heating and cooling system for the whole building to address their concerns and fix the problems. The new system consists of 14 individual package geo units ranging in size from 3-tons to 6-tons with a total capacity of 76 tons. The energy model indicated that the total peak load would require 40 tons of loop field. This reduced load is largely a result of taking control of the outside air load and handling it separately from the HVAC system, and scheduling the outside air to match the occupancy of the space. One thing I’ve seen with most churches is that their load actually moves around the building as occupancy changes, so the loop load is generally less than the total of the individual zone loads.
There were several major challenges to the new installation. First of all, there was very little space for the loop field. We finally settled on a narrow space along the west side of the building between the sidewalk and the church wall. It was approximately 10 feet of space that allowed us to drill 12 bores at 500’. We used 1-1/4” PE and tied 3 circuits together into 4 sets of 2” headers into the mechanical room. There the pipes were joined into one 3” header that then was piped all around the building as a 1-pipe primary secondary system.
Each heat pump was ordered with an internally mounted secondary pump and then piped into the main pipe with 2 closely-space tees. The main circulation pumps were Grundfos Magna 3 models and controlled with a delta T controller which varies the flow as a function of temperature difference between entering and leaving water. As more units operate, the temperature difference increases, and causes the pump to speed up to maintain a temperature difference setpoint. We have 2 pumps on the system, but I pump provides about 70-80% of our requirements, so that gives us quite a bit of redundancy. Both pumps rarely come on since the load is so diverse, and we are using a very small amount of energy only as necessary for pumping. This arrangement also is self-controlling, so no external control systems are necessary.
Space for some of the units was also a concern. We had to be flexible as to unit locations so that we could serve individual areas effectively, but also connect to and use existing ductwork as much as possible. Fortunately, the church staff was quite flexible and willing to work with us to get the locations we needed for unit placement. The original mechanical room in the 1997 addition had quite a bit of room and access to a lot of the ducting systems, so we were able to install a lot of the units in that area. As always in an older building, there were also challenges to getting the main piping all around the building. 2’ thick stone walls of the original building were especially difficult. Luckily, we found quite a few openings that we could re-purpose when demo was finished.
The new ventilation system consists of an ERV located in that mechanical room that connects to some of the existing O/A ductwork, then it connects to both the return ductwork of the sanctuary system, and the return duct of the unit that serves the office area in the lower level of the addition. To make the most of the ERV expense, we set up a damper system and schedule that changes the supply of the conditioned fresh air off the ERV from the Sanctuary on Sunday mornings to the offices on Monday-Friday, based on their occupancy schedule. In other words, we distribute the fresh air to occupied spaces only as necessary. You don’t typically need outside air when no one is in the building. This reduced amount of outside air has made huge improvements in humidity control. In the summer our 2-stage equipment runs primarily on 1-stage giving long run times and good humidity removal. In the winter, the reduction of ventilation air and elimination of combustion air helps keep humidity levels much higher. In addition to that main ERV, we installed another smaller one in the education wing of the church that also runs on an occupancy schedule. As a fail-safe in times when the sanctuary may be really loaded with people, we installed an outside air duct in the return air of those units that opens up if the CO2 level goes over a pre-determined level. This demand-controlled system operates from a control point in the sanctuary that also displays temperature, humidity, and CO2 level.
For control of our units, we use the communicating thermostats designed for these units, that also connect to Wi-Fi throughout the building. This allows us and church personnel to remotely monitor the units and their operation, even sending us an email if there’s a problem generally before anyone at the church knows about it. We have learned from many geothermal installations over the years that our systems operate most efficiently when we do NOT use any setback programs. This is even more important now with the advent of 2-stage and variable-speed units. They operate more efficiently and economically when they only have to maintain a temperature, not change it by a few degrees. I’ve seen actual documentation on some of our systems showing this to be the case.
In summary, the results of this installation have produced a much more comfortable environment for the church, and saved significant amounts of money and energy. They were spending approximately $16,600 a year with the existing system and suffering with all the humidity issues, and now the geothermal system only costs about $7200/year to operate. So, they are saving $9000/year, and have eliminated all CO2 production on site. If they choose to add a solar system in the future, they will also be much closer to being net-zero than they could have been. The reduction in demand will allow them to get about 30% more from a given solar system size.
This project was started before the IRA went into effect but lasted long enough to be completed after the new law, so they were able to take that tax credit benefit as a generous bonus to their favorable payback.
Jack DiEnna, Executive Director & Founder of the Geothermal National & International Initiative (GEO-NII). Originator of the “Anchor Tenant” concept for networked geothermal systems installing the ground loop heat exchanger in K to 12 schools’ fields, parking lots, etc. Appointed US Department of Energy’s Geothermal Visionary team. Member of the American/Canadian Bi National GHP Standards Committee. Founding Member of the New York Geo Association and the Pennsylvania Geothermal Association.

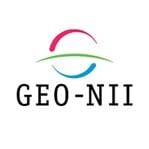
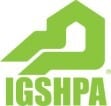