Sampling Procedures and Sample Frequency Using New Age Thermally Enhanced Grouting Products
By Tyler Harbeck , GeoPro, Inc., Lead Product Engineer
History of Thermal Grout
Thermally enhanced grout is not the most glamorous component of the ground source heat pump system, but one could argue it is one of the most important. Thermal Grout provides the direct conduit from the ground loop to the formation and provides the environmental protection required to prevent ground water from being contaminated. On the surface Thermal Grout does not appear to have undergone the same technological advances the other components of the ground source heat pump system have. However, history shows that the grouting products being used this decade differ greatly from the grouting products used at the end of last century. For reference the timeline below provides a brief history on how grouting products began and where grouting products currently are.
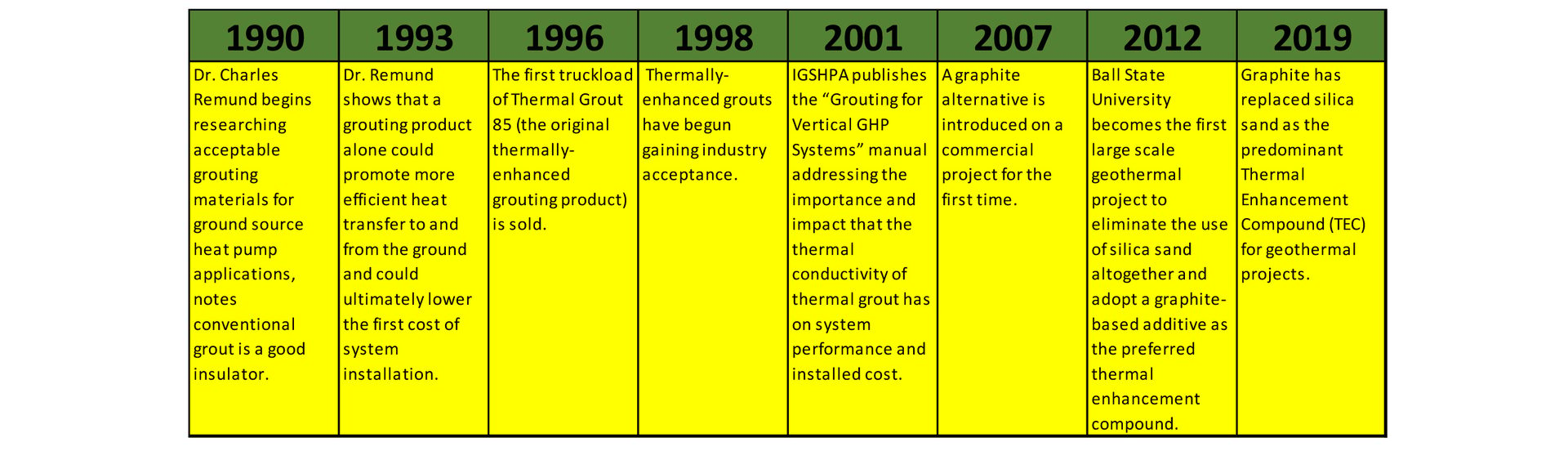
In 1990 the Hubble Space Telescope was launched, smoking was banned on all cross-country flights in the United States, and in a lab at South Dakota State University Dr. Charles Remund begins researching acceptable grouting materials for ground source heat pump applications. That initial research in 1990 highlighted that grouting products available at that time were very good insulators. Further research ultimately discovered that adding a Thermal Enhancement Compound (TEC) would positively impact system design and first cost. Over the next 30 years the industry has seen two dominate TECs 1) Silica Sand and 2) Graphite. The introduction of a graphite-based TEC is the type of technological advancement that is on par with some of the equipment advancements this industry has seen over this same 30-year period.
Anatomy of a Thermal Grout
First let us look at the basics and what composes a thermal grout. Almost all thermally enhanced grouts are made up of primarily three components 1) a sealing component which is typically bentonite or cement or a combination of the two, 2) a Thermal Enhancement Compound (TEC) which is either silica sand or graphite, and 3) a known mix water volume which is specified by the manufacturer. Below is a comparison to the two TEC options.
Silica Sand:
Silica Sand is abundant, locally sourced, and a relatively inexpensive TEC. Sand is abrasive making it hard on equipment and is a relatively heavy material making it very labor intensive. As the industry moves towards deeper bores the higher density of silica sand prevents it from being used on these types of projects. The weight creates enough pressure from the grout column on the outside surface of the U-bend that the piping’s pressure rating may be exceeded during grouting. In addition, because sand is not sourced by the geothermal grouting company it is not held to the same stringent quality control standards that graphite products are and finding a good quality silica sand source can prove difficult.
Graphite:
Graphite TECs are a lighter more conductive alternative to silica sand. They are supplied directly from the grouting manufacturer and should be specifically designed to exceed the published thermal conductivities specified by the manufacturer. Graphite is a non-abrasive material that helps prevent formation loss. Due to their lighter density graphite grouting products are the recommended choice especially when bore depths exceed 600 ft. But graphite enhanced grouts are far more sensitive to mix water volume than silica sand. This is due to the small amount of graphite needed to achieve the same level of thermal performance. For reference 1 lb of graphite can replace as much as 11.4 lb of silica sand. This statement will be dependent on the quality of graphite from the manufacturer.
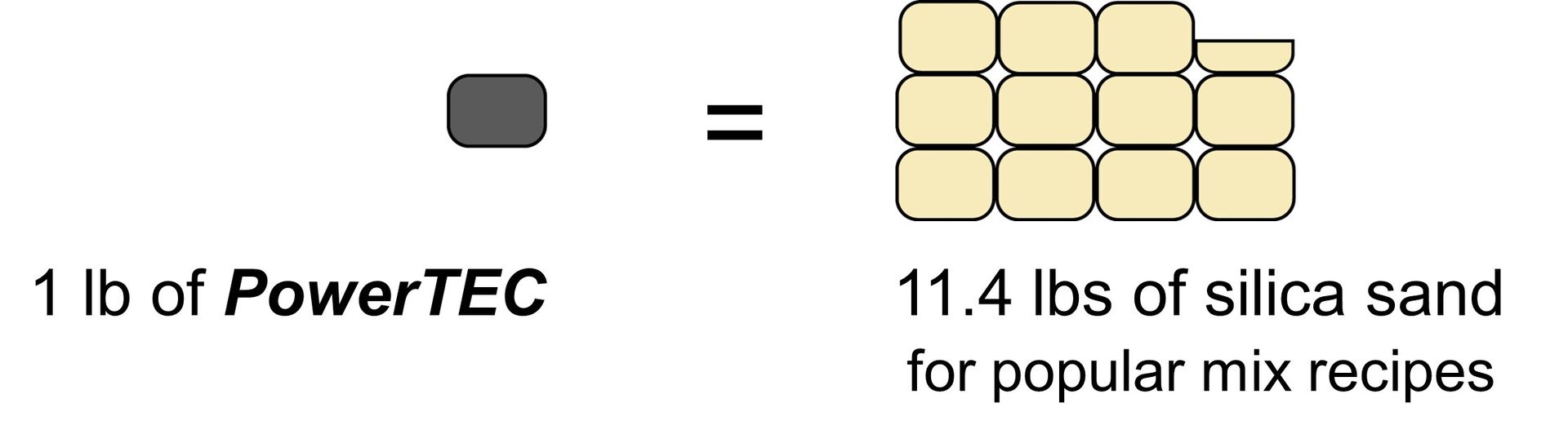
Grout Commissioning and Quality Control
The timeline above depicts how manufacturer’s grout offerings have changed. However, very few adjustments have been made to the recommended field management and quality control processes used to verify the thermal performance of the grouting products being installed. Historically this has been done by collecting 3 samples for every 50 bores in combination with material usage reporting. Both are great practices and highly recommended at a minimum for any geothermal project. However, 3 samples per 50 bores as a rule of thumb is likely no longer the correct answer if graphite is used. In addition, history seems to be repeating itself as there has been a recent influx in geothermal projects requesting sample testing for every borehole. This too is likely not the correct answer. Testing at this high of a frequency provides very little additional value over lower testing frequencies and increases the cost of a project. The requested increase in sample testing frequency indicates the industry is not comfortable with the current manufacturer recommended testing procedures.
A field commissioning and QC program is an integral part of system installation. The process starts long before the first bore is ever drilled. All product specifications and submittals should be in order prior to grouting the first bore hole. All products on site should be verified ahead of time that they are the right product for that specific application. A comprehensive material volume calculation should have been completed including any expected loss to formation. This verifies that the amount of material needed to complete the project is on site and material usage reports can then be used to verify the correct amount of material is being installed as the project progresses. A sample testing schedule should be in place and the contractor should collect samples occasionally throughout the process and send them to a lab capable of testing thermal conductivity in accordance with ASTM-5334. This sample collection process is not meant as a policing agent, but rather a field verification technique to ensure the product is performing according to the manufacturer’s specifications. The frequency and volume of sample collection should be totally dependent on the size of the project and the TEC that will be used to complete the project. It needs to be understood that delivering a specific grout TC value is as simple as counting bags and measuring water. Repeatable results should be the expectation.
Sampling Recommendations - Silica Sand
To meet any manufacturer’s published mix recipes, a silica sand source must contain over 99% silica dioxide. Silica dioxide content is the driving force for sands thermal performance. If a sand product is in question most manufacturers can verify whether it is approved for use with their products. Two common thermal grout mix recipes are highlighted in Figure 1. Each can achieve a minimum thermal conductivity of 1.20 but/hr-ft-°F. Note the amount of bentonite is the same for each recipe. Differences include yield, density, the amount, and type of TEC.
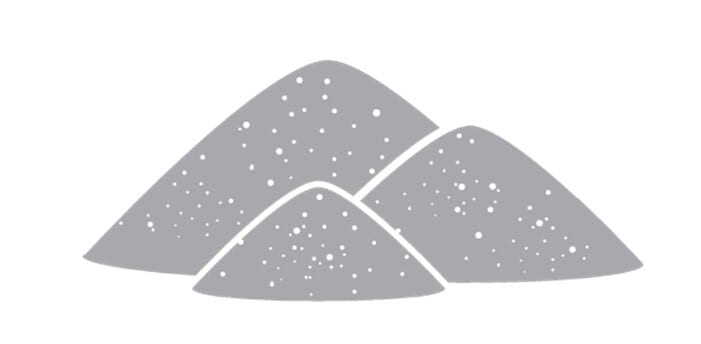
The first highlighted recipe contains 400 lbs of silica sand within a batch that yields 42.2 gallons. Assuming a completely uniform slurry this means that 9.48 lb of sand is suspended in every 1 gallon of slurry. For the recipe in question silica sand makes up roughly 63.5% of that grout slurry. A uniform batch is very easy to achieve and identify due to the sheer volume of solids present. Standard sampling collection at a frequency of 3 samples for every 50 bores is more than adequate. Pair this sampling frequency with documented material usage reports and no further QC practices are required. A side note when using silica sand on a job site: As thermal conductivity changes so does density. The correlation is strong enough that a mud balance can be used to spot check batches on site. This is not a direct TC measurement but is an effective field QC measure that eliminates the need to sample more frequently than 3 times per 50 bores.
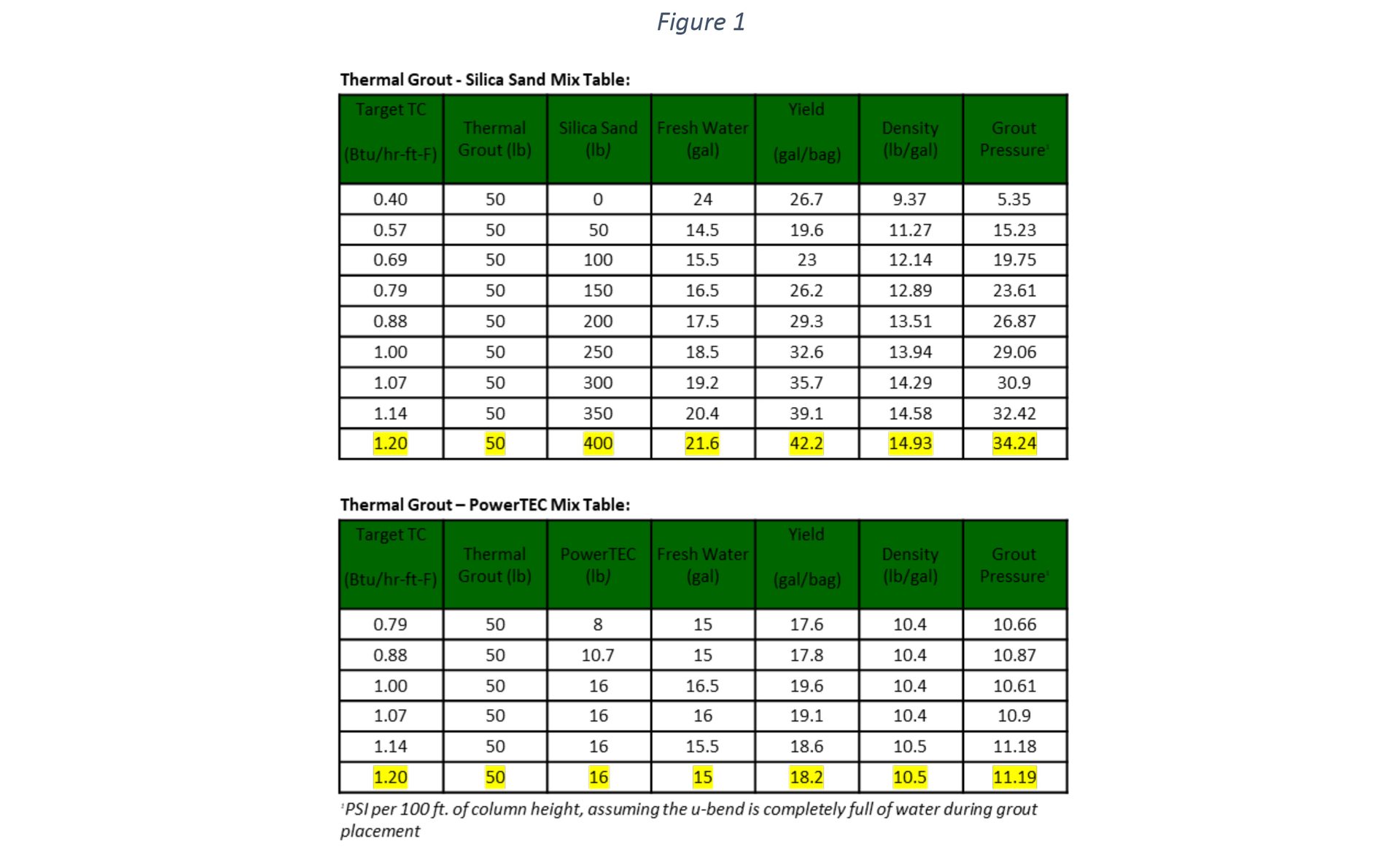
Sampling Recommendations - Graphite
Graphite thermal enhancement compounds are supplied directly from the grout manufacturer and should undergo a comprehensive quality control process before ever being put into a bag. Therefore, the contractor can be confident that when mixed in accordance with the manufacturer’s recipes the product will meet or exceed the minimum published thermal conductivity.
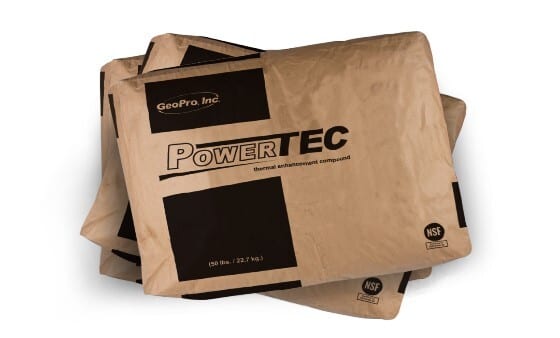
However, collecting quality samples in the field with a graphite-based TEC proves difficult, and different sampling techniques should be used. The second recipe highlighted above uses PowerTEC, which is the trade name for a specific graphite based thermal enhancement compound. The recipe shows that only 16 lb. of graphite is contained within a slurry that yields 18.2 gallons. Again, assuming the slurry is completely uniform, this equates to only 0.88 lb. of PowerTEC suspended in every gallon of slurry. For the mix in question graphite only makes up 8.37% of the grout slurry. Therefore, more emphasis needs to be placed on collecting a uniform sample. Increasing the frequency of testing and collecting samples from every bore or batch does not guarantee those samples are uniform and is typically not the right answer. The focus should change to how one collects a uniform 44 oz sample from a grout batch that can vary from 40-70 gallons in volume. GeoPro, Inc. has discovered that the most accurate way to achieve good consistent samples in this manner is to guarantee those samples are uniform and representative before they are ever collected and sent in for testing. This can be done by filling a 5-gallon bucket full of grout from the batch in question. This bucket should be filled after roughly 1/3 of the batch has already been pumped into the borehole. Simply fill the bucket from the side discharge (if using a Geo-Loop Grouter). Once collected, continue to pump the remainder of the batch down the borehole. The five gallons of grout can sit static in the bucket for a few minutes. Then using a shovel/tool remix the grout located in the 5-gallon bucket. Visibly verify that the grout in the bucket is uniform and collect a sample using a standard 44 oz sample container scooping from the bottom of the bucket to the top. The remainder of grout in the bucket can then be mixed back into the next batch of grout assuming it is not deemed too thick. This process will allow the contractor to obtain a sample from a volume up to 18% of the grout slurry depending on recipe. This process will provide a more representative sample than a single 44 oz sample using standard collection methods and removes most of the variability when collecting small samples. This sampling process should be used to collect up to 3 samples for every 10 bores on a project. As a project progresses and consistent results are achieved sampling can be reduced to collecting 1 sample for every 10 bores. A mud balance cannot be used to spot check graphite recipes as the densities do not differ enough in magnitude.
Conclusion
In closing grout sampling procedures should be dependent on the TEC used. Sampling of every batch or bore is not required and simply adds cost to a project for very little benefit. In addition to the suggested sampling frequencies, material usage reports and mud balance tests (where applicable) should be completed as part of a quality control process. The latter two are great ways to get instant feedback during the grout installation process.
Tyler Harbeck, Lead Product Engineer, GeoPro, Inc.
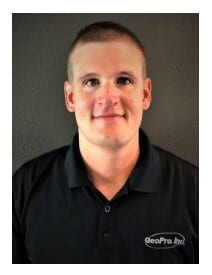
IMAGE CREDIT: Sonja Filitz / Royalty-free / iStock / Getty Images Plus