Selecting Piping Materials for Ground Heat Exchangers
By Lance MacNevin, Director of Engineering for the Building & Construction Division at the Plastics Pipe Institute (PPI)
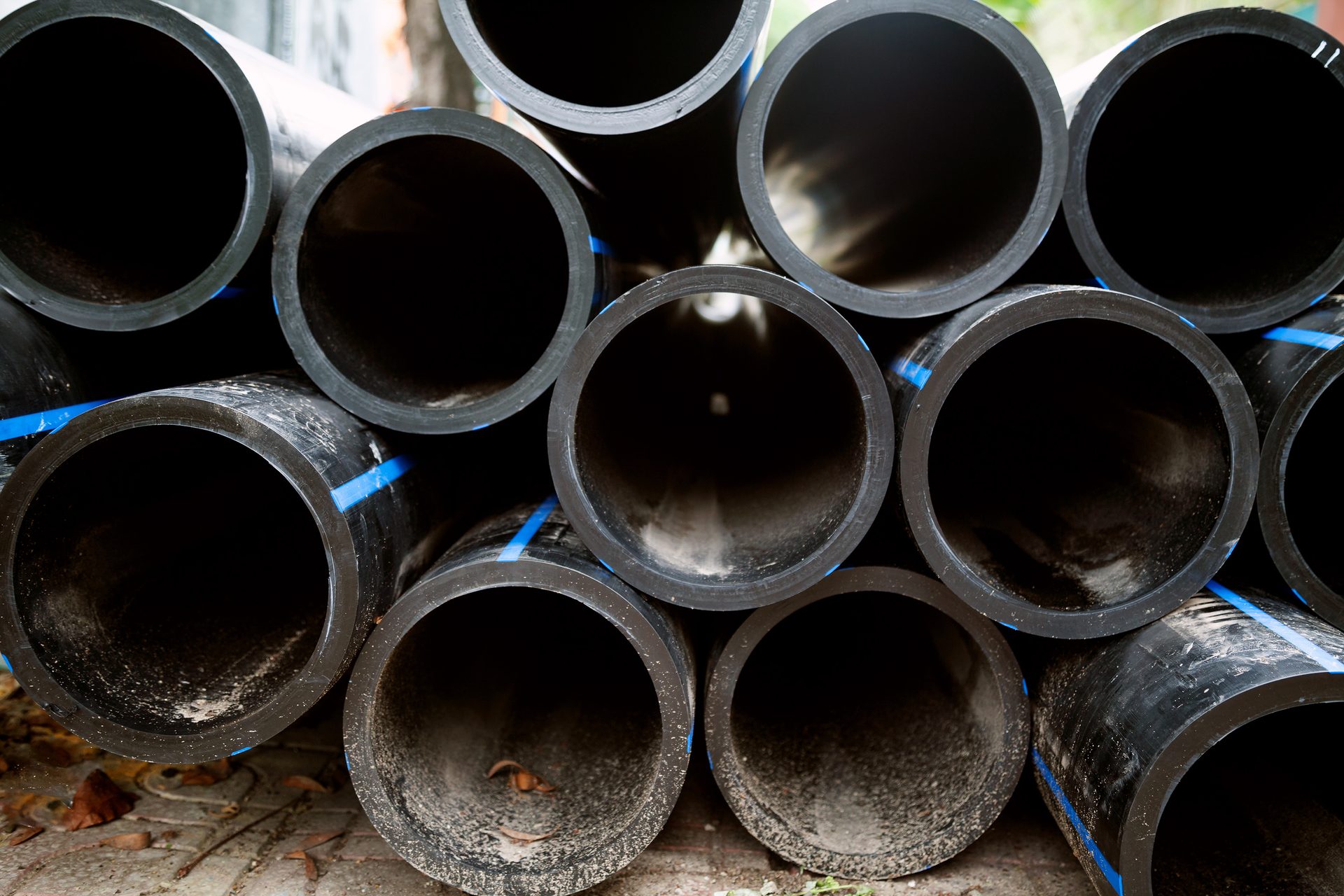
The implementation of ground source heat pump systems is growing rapidly as homeowners, governments, businesses, universities, and others are turning to geothermal technology to save energy, address climate change, and construct efficient heating and cooling systems with long-term reliability. The Plastics Pipe Institute, the Texas-based non-profit trade association, estimates growth in demand for GSHP systems of at least twenty-five percent per year over the next several years.
A critical aspect of GSHP systems is the piping that is buried in the ground or submerged in water. The network of pipe and fittings, sometimes referred to as the ground heat exchanger or simply the ground loop, is the link to the earth’s thermal energy.
Ground heat exchanger piping materials must provide corrosion resistance, chemical resistance, temperature resistance, flexibility, impact resistance, resistance to slow crack growth, and long-term hydrostatic strength (pressure capability). In addition, ground loop heat exchanger materials must provide suitable heat transfer capabilities, since conducting heat with the earth is the primary function of the ground loop.
Fortunately, several types of plastic piping materials are proven to meet these challenges. Each of these piping materials delivers long-term reliability proven over decades of use around the world.
Because it is important for specifiers, purchasers, and installers to understand the characteristics of each of these materials, as well as the relevant standards, this article will explain four types of plastic piping materials (HDPE, PEX, PE-RT, PP) which are approved in US model mechanical codes for ground loop piping. Three of these materials are in the 2016 edition of ANSI/CSA/IGSHPA C448, while the fourth is planned for inclusion in the next edition.
High-Density Polyethylene
High-density polyethylene (HDPE) is the predominant piping material used for ground heat exchangers. These pipes and fittings are joined primarily by heat fusion methods to provide leak-free connections.
HDPE pipes have improved significantly over the past twenty years thanks to new bimodal resins that deliver higher strength with greater toughness and resistance to slow crack growth. The highest performing grade is known as PE4710 which has higher density, much better resistance to slow crack growth caused by abrasion, and higher strength than the previous generation PE3408 pipes. The TC value of PE3408 is 3.0 BTU ∙ in/hr ∙ ft2 ∙°F, while the TC value of PE4710 is 3.1.
For vertical boreholes, pipes should be provided with a 180-degree U-bend fused to two parallel pipes in the factory. For example, for a 400-foot-deep borehole, the piping manufacturer will provide two 400-foot pipes which are fused in the factory to a molded U-bend fitting. This allows the drilling contractor to drop the U-bend assembly down the borehole without having to first fuse pipes to the U-bend fitting in the field, saving time and adding reliability.
Since ground loops are a demanding application for pipes, it is recommended for piping components to be third-party certified to industry standards. For HDPE, the first of these is NSF/ANSI 358-1 “Polyethylene Pipe and Fittings for Water-based Ground Source Geothermal Heat Pump Systems”.
HDPE pipe should also be certified to a national pipe standard such as ASTM D3035 or CSA B137.1 which defines everything from dimensions to material properties to long-term strength. Finally, it is recommended for ground loop pipes to be certified to NSF/ANSI/CAN 61 “Drinking Water Systems Components - Health Effects” to ensure that any aquifer or water reservoir into which the piping system is installed is not contaminated by the piping itself.
Figure 1: Coil of HDPE piping with molded U-bend already fused to pipe ends. [Courtesy Versa profiles]
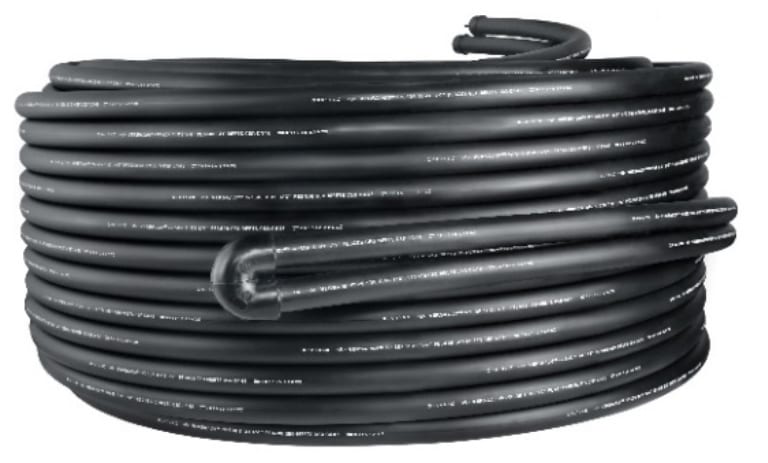
Figure 2: HDPE loop in slinky configuration being dropped into a trench. [Courtesy Centennial Plastics]
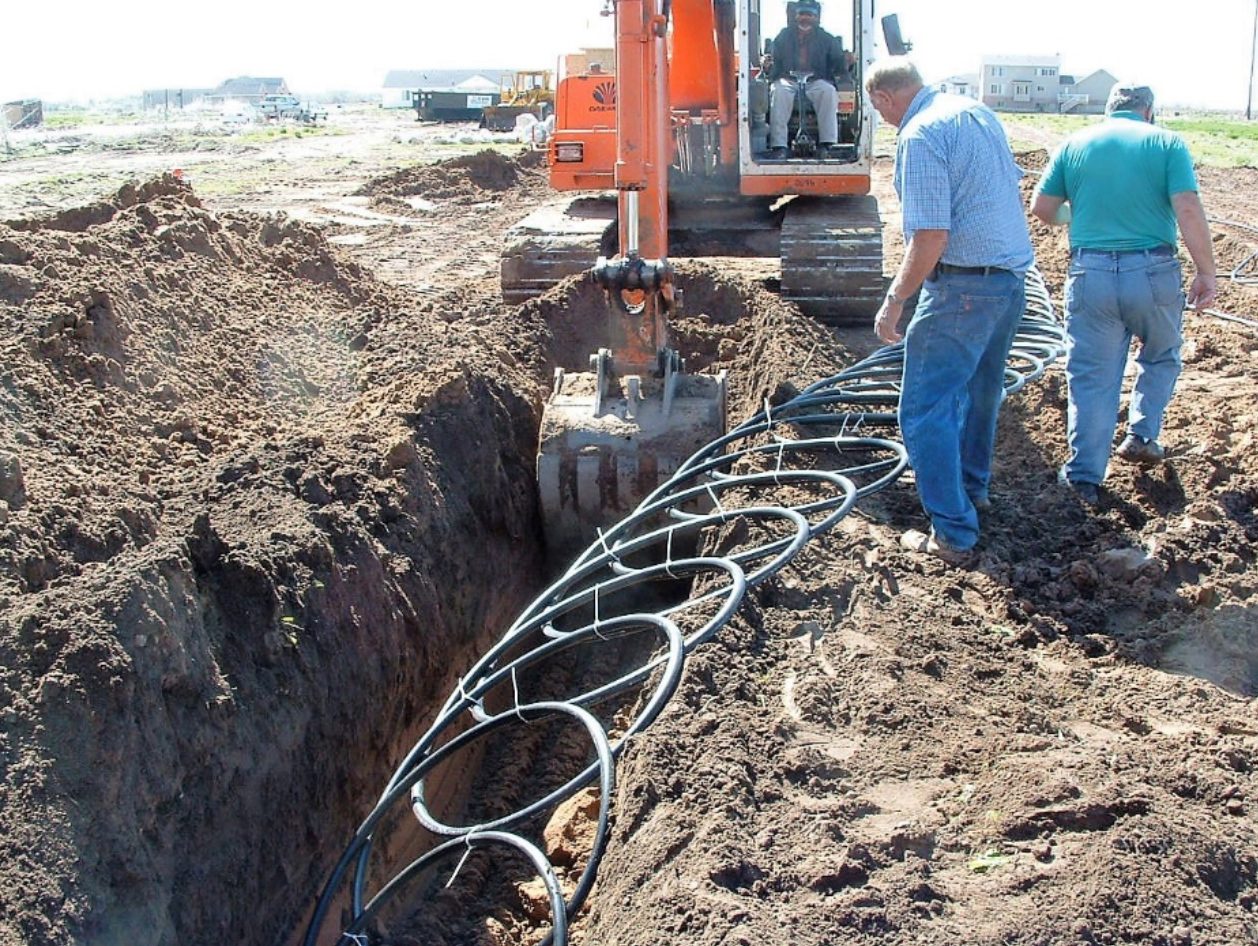
HDPE pipes and fittings are typically joined using butt fusion, socket fusion, or electrofusion methods. One bad joint could create a leak that is very expensive and difficult to find, access, and repair, so fusion contractors should seek hands-on training from the supplier of the fusion requirement to gain the skills needed for proper fused joints. McElroy University is a popular source of fusion training and provides events across North America.
Once trained, installers should strictly follow the guidance provided in ASTM F2620 “Standard Practice for Heat Fusion Joining of Polyethylene Pipe and Fittings” which describes proper fusion procedures for butt and socket fusion. Electrofusion fittings should be installed in accordance with ASTM F1290.
Once installed, ground loop piping systems should be tested according to ASTM F2164 “Standard Practice for Field Leak Testing of PE and PEX Pressure Piping Systems Using Hydrostatic Pressure”. This practice provides the details of safely pressurizing and testing buried pipe systems.
Crosslinked Polyethylene
Crosslinked polyethylene (PEX) is HDPE that is modified during manufacturing to crosslink the majority of the polyethylene molecular chains. The result is a flexible pressure pipe material with high temperature capabilities. PEX was first produced in the early 1970s and is now used for many applications. It is more expensive to produce than HDPE.
The primary benefit of crosslinking HDPE into PEX is capability of continuous operation at temperatures of 180°F (82°C) or above. This higher temperature capability may be necessary in borehole thermal energy storage (BTES) systems where thermal solar energy is pumped into the earth to raise the ground temperature during summer, for example. An example of this is Drake Landing Solar Community in Alberta (www.dlsc.ca). PEX tubing also has excellent chemical resistance and it is slightly more flexible than HDPE. The TC value of PEX is 2.9 BTU ∙ in/hr. ∙ ft2 ∙°F.
Figure 3: PEX tubing used as horizontal ground loops
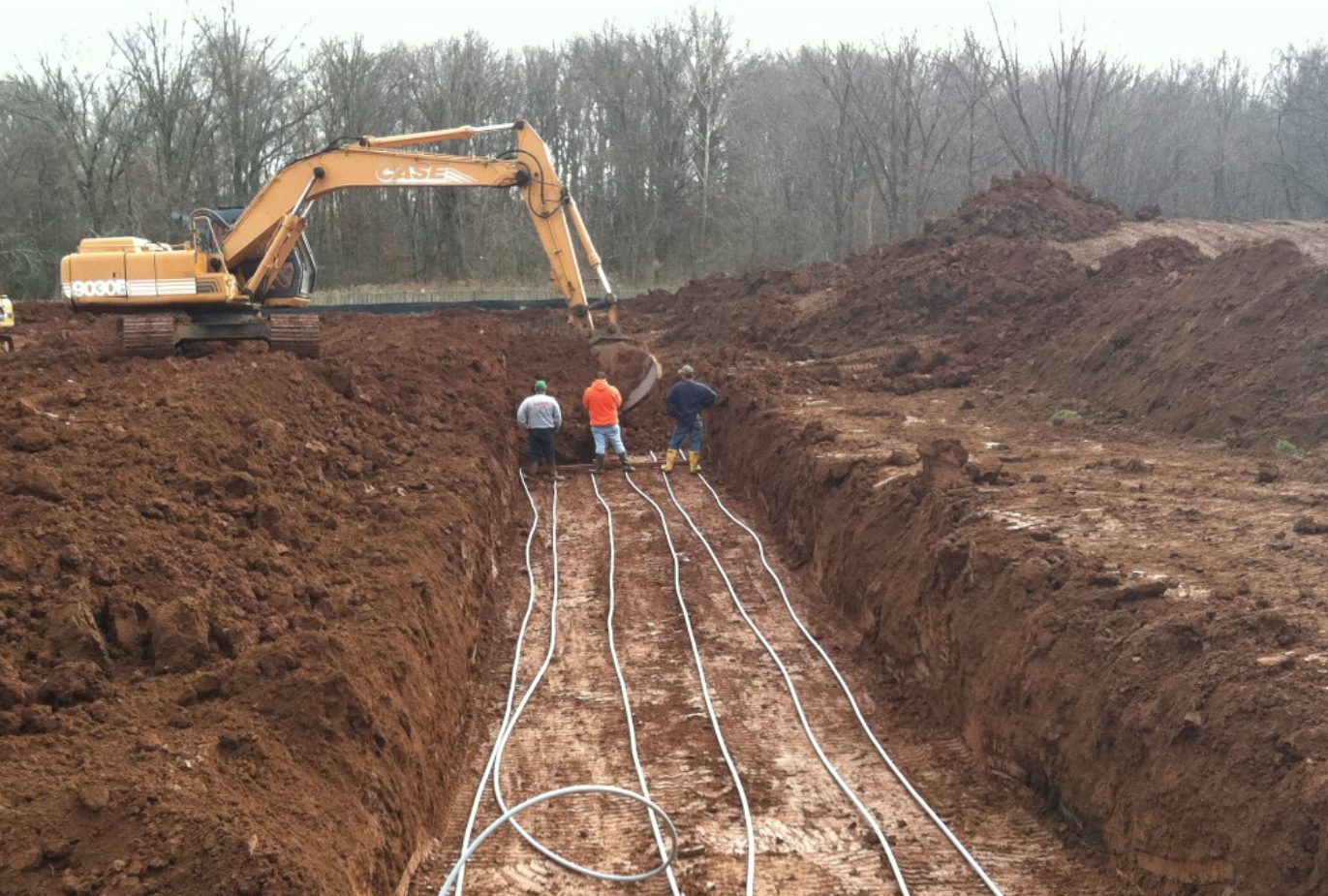
"PEX tubing is not approved for joining with butt fusion or socket fusion methods because most of the molecules are already locked in place and are not free to flow into the adjoining components."
PEX tubing is not approved for joining with butt fusion or socket fusion methods because most of the molecules are already locked in place and are not free to flow into the adjoining components. Instead, several types of mechanical compression fittings are approved for underground use with PEX tubing, as are electrofusion fittings. For a new installer of geothermal piping, installing PEX fittings with manual hand tools avoids the cost and complexity of becoming proficient with heat fusion.
In North America, PEX is available up to nominal tubing size 3 and can be supplied as coils, straight lengths, or as prefabricated U-bends for boreholes. PEX ground loop piping should have a minimum material designation code of PEX 1206 and be certified to ASTM F876 or CSA B137.5 as well as NSF/ANSI Standard 358-3 and NSF/ANSI/CAN 61.
Figure 4: PEX tubing with factory-formed double U-bend. [Courtesy REHAU]
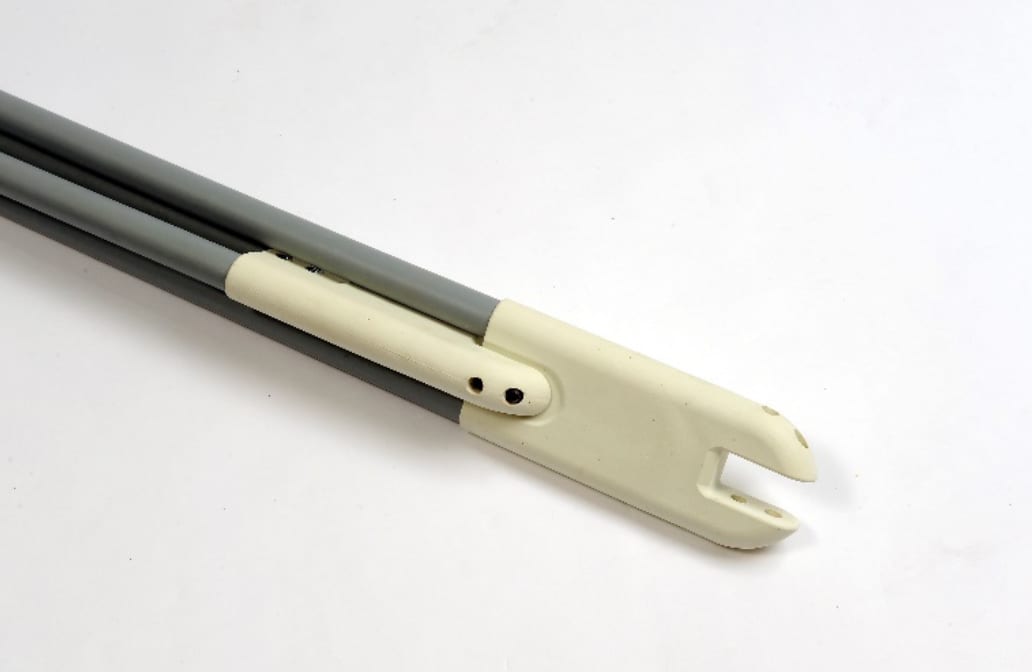
Polyethylene of Raised Temperature
Polyethylene of raised temperature (PE-RT) is high-density polyethylene piping material with enhanced capabilities to withstand temperatures up to 180°F. PE-RT may be joined using heat fusion processes, just like HDPE, or using mechanical compression fittings, just like PEX. PE-RT tubing may be produced using PE3608 or PE4710 materials. The TC value is 3.0 BTU ∙ in/hr ∙ ft2 ∙°F or 3.1, depending on the base resin that is used for its production.
PE-RT tubing is typically more expensive than HDPE but less expensive than PEX and can be a great choice when higher temperature resistance than what HDPE can provide is required.
Like PEX tubing, PE-RT is typically produced in copper tube size dimensions, but larger diameter PE-RT pipes are also available. PE-RT ground loop tubing should be certified to ASTM F2769 or CSA B137.18 as well as NSF/ANSI Standard 358-4 and NSF/ANSI/CAN 61.
Polypropylene
Polypropylene (PP) is a rigid piping material that is used in a wide range of plumbing and mechanical applications. Two types of PP are used for pressure piping systems: PP-R (polypropylene random copolymer) and PP-RCT (polypropylene random copolymer with modified crystallinity and temperature resistance). PP-RCT material has approximately 25% higher pressure rating than PP-R pipes for the same wall thickness at a given operating temperature.
Polypropylene pipes may include layers of chopped glass fibers for reduced longitudinal thermal expansion/contraction. PP-R and PP-RCT pipes and fittings are completely compatible with each other.
PP-R and PP-RCT piping can be used for geothermal headers and manifolds in vaults or mechanical rooms, as well as indoor piping. Joints are typically heat fused following standard industry practices, but flanged and grooved fittings are also available.
PP piping should be certified to ASTM F2389 or CSA B137.11 as well as NSF/ANSI Standard 358-2.
Figure 5: PP-5 Manifolds in an outdoor vault
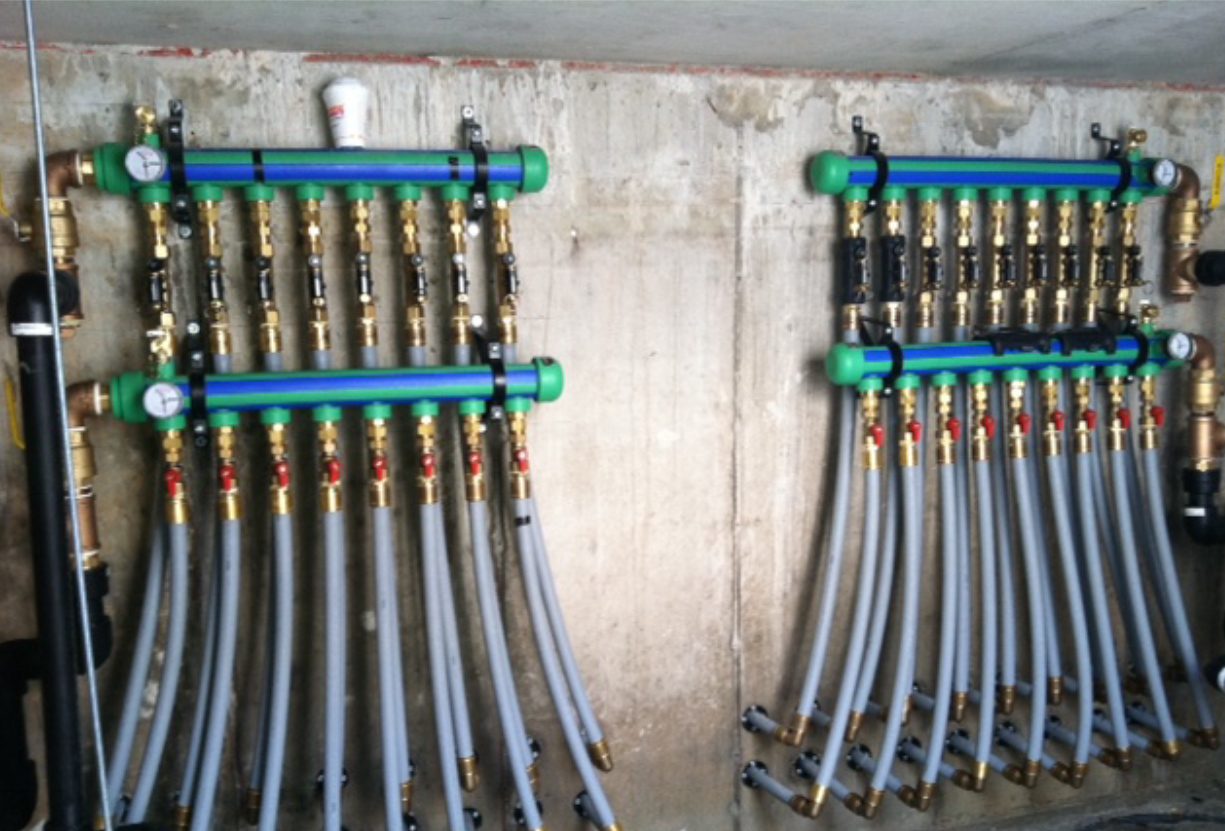
Summary
HDPE, PEX, and PE-RT are all recommended for ground loop piping, and each has its own benefits. Additionally, PP is a suitable material for headers and indoor piping. These piping materials provide high performance and reliability over decades of service.
When selecting each of these materials, it’s important to specify the correct standards and certification requirements, and to be sure to seek out proper training for the joining system/s being utilized.
PPI recently published the new Model Specification MS-7 “Plastic Piping Materials for Ground Source Heat Pump Applications” that covers each of these materials in detail. MS-7 also provides installation advice for piping systems. Designers can also use the free online Plastic Pipe Design Calculator at www.plasticpipecalculator.com to assist with calculations such as pressure loss and static water column pressure.
Lance MacNevin, P.Eng., is the Director of Engineering for the Building & Construction Division at the Plastics Pipe Institute (PPI). He has been in the plastic pipe industry since 1993 involved with applications such as hydronic heating and cooling, geothermal, plumbing, and fire protection systems. Lance earned his IGSHPA installer accreditation in 2008 and has been closely involved with the geothermal industry ever since. He serves on technical committees within ASHRAE, ASPE, ASTM, AWWA, CSA, IAPMO, ICC, and IGSHPA.
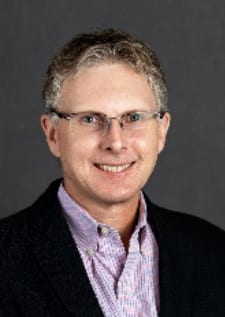
IMAGE CREDIT: Getty Images Plus via Getty Images