Radiant heating and cooling system helps university complex meet aggressive energy savings goals
CASE STUDY
University of Chicago project meets LEED Gold guidelines.
By Steve Cooper
The design, which included a REHAU radiant heating and cooling system, met the EUI performance requirements, making the University of Chicago the first building project to include a specific energy goal as part of the request for proposal (RFP). Image courtesy of Tom Harris
The miles of PEX tubing embedded in the ceilings of the new 360,000-square-foot North Campus Resident Hall and Dining Commons at the University of Chicago not only provided a state-of-the-art heating and cooling system but also helped the project to be LEED Gold Certified. At the university, 300,000 linear feet of REHAU RAUPEX PEXa oxygen barrier tubing, along with other components such as 183 distribution manifolds, were used for the hydronic radiant heating and cooling systems.
Pre-fabricated PEX tubing circuits and manifold stations were assembled on-site in centralized locations in order to reduce the installation time and keep up with floor-by-floor construction. This also reduced the interference of multiple trades on the same floor by keeping the radiant circuit construction off the floor until completely ready for installation.
According to the U.S. Department of Energy (DOE), “Radiant heating systems supply heat directly to the floor or to panels in the wall or ceiling of a house. The systems depend largely on radiant heat transfer - the delivery of heat directly from the hot surface to the people and objects in the room via infrared radiation.”
“This project provides a prominent demonstration of the energy efficiency, comfort, reliability, and environmental benefits of PEX-based radiant systems,” states Lance MacNevin, P. Eng. director of engineering for the Building & Construction Division of the Plastics Pipe Institute (PPI), the major North American trade association representing the plastic pipe industry. REHAU is a member company of PPI.
“Hydronic radiant systems circulate heated or chilled fluid through pipes embedded in floors, walls, or ceilings,” MacNevin says. “By delivering the majority of heating and cooling energy through the ceilings of this project, air requirements and fan loads are greatly reduced, saving electricity. This project is an excellent application of radiant heating/cooling hybrid technology, and it has operated successfully through several seasons already. We know that others in the industry will benefit from this project. It is a prime example for architects and engineers of what can be accomplished with a PEX radiant heating/cooling hybrid system.
“It is also an excellent case study that demonstrates the advantages of hydronic systems for large-scale residential applications that provide a comfortable environment with maximum efficiency and have been proven to support healthy indoor air quality,” he continues. “The ability of the design and construction teams to streamline their installation technique to speed installation of the PEX tubing is another huge success for this project.”
Pre-fabricated PEX tubing circuits and manifold stations were assembled on-site in centralized locations in order to reduce the installation time and keep up with floor-by-floor construction. This also reduced the interference of multiple trades on the same floor by keeping the radiant circuit construction off the floor until completely ready for installation. Image courtesy of REHAU
One of the other beneficial aspects of the project is the ‘smart’ way the heating and cooling systems are controlled. Building controls are linked to meters that record energy use and system performance and slab sensors signal the manifold valves to provide heated or chilled water to each room, providing continuous comfort while saving energy.
The three-building project, with towers of six, 11 and 15 floors, houses approximately 800 undergraduate students and includes music rooms and hang-out spaces. The new complex replaced the Pierce Tower Residence Hall and Dining Commons, which housed students for more than 50 years before it was demolished. When planning began, school administrators had a goal to create a modern, energy-efficient structure that would bridge the academic community with the surrounding neighborhood of Hyde Park.
Kevin Rodgers, who was the university’s campus energy manager at the time of construction, worked with energy specialists at the National Renewable Energy Laboratory (NREL) to set an aggressive annual energy usage intensity (EUI) target of 56.6 kBtu/ft2 for the new residence hall. EUI is defined as the total amount of energy used by a building during a year divided by its total gross floor area. The University of Chicago has pursued energy efficiency across its campus for years, but Rodgers says this is the first building project to include a specific energy goal as part of the RFP.
Compared to the average residence hall usage in Chicago, this EUI represents a 41% reduction, eliminating 1,920 metric tons of CO2 emissions per year, a significant sustainability achievement. Rodgers indicated that the old Pierce Hall had an annual EUI of 150 kBtu/ft2, nearly three times the target for the new structure, while the average university residence hall building in Chicago has an EUI of 96.6 kBtu/ft2 a year based on real data provided by five area universities.
Unique design meets energy targets
Architectural firm Studio Gang Architects (Chicago) and general contractor M. A. Mortenson Construction (Minneapolis, MN) were awarded the design-build partnership.
“There were some concerns going in that the aggressive energy goals we established would result in rectangle boxes instead of architecturally significant buildings,” Rodgers says. “That ended up being false. The four finalists all had very unique designs that met our energy requirements.”
The team targeted and subsequently achieved USGBC LEED Gold certification for BD+C, a measure of the sustainability and efficiency of the design.
More than 285,000 linear feet of REHAU RAUPEX tubing was used for the radiant heating and cooling systems in the floors and ceilings for the three new buildings that make up the University of Chicago's new 360,000-square-foot North Campus Residence Hall and Dining Commons complex. Image courtesy of REHAU
The building’s common areas are heated via a traditional forced-air system, while the student living quarters use REHAU in-slab radiant heating and cooling. Todd Zima, the design principal at Studio Gang, says the radiant system was chosen early in the project for the dorm rooms in order to improve energy efficiency and enhance comfort for the students. By circulating heated or chilled water through 5/8-inch PEX tubing installed at 6-inch spacing in the ceilings on each floor, the hydronic system maintains the spaces at even, comfortable temperatures while using less energy than traditional forced-air systems.
Another ability of the PEX-based system was to provide independent zones. The zoning was divided by manifolds, whose circuits were divided into north- versus south-facing spaces. REHAU’s actuators were utilized on the manifolds, but rather than being connected to thermostats, as typically seen in hydronic radiant projects, they were connected to window sensors so that the radiant system could be shut off in cooling mode if the operable windows were opened by occupants. This design strategy was incorporated to save energy and avoid any undesirable condensation from occurring.
“To include radiant cooling in a project of this size in this climate for a residential structure was something we hadn’t seen,” Zima explained. "Sharing the capabilities of the REHAU radiant system with Mortenson and university officials convinced them it was the way to go."
Energy targets were not the only ambitious component of the project. Mortenson set an aggressive construction schedule to have the residence hall ready by the start of the school year. Installing 300,000 feet, or more than 56 miles, of PEX tubing at the pace required to meet Mortenson’s schedule required some ingenuity.
Ryan Blackman, the project manager at Chicago-based Mechanical Inc., says participation by his company and REHAU early in the planning stages helped them meet tight deadlines that would come later. Blackman’s team worked with engineering firm dbHMS (Chicago) and Studio Gang a year before construction began to “determine how the building would actually be built.”
Partnering early led the team to preassemble each room’s radiant heating/cooling tubing system on wire mesh on the ground. A floor’s worth of mats was then stacked and lifted by crane on a custom-built platform to each tower for speedy installation.
“We thought outside the box a fair amount, and, to be honest, we surprised ourselves,” Blackman explains. “The first couple of floors were a bit of a learning curve, but once we got into a groove of the entire fabrication process, we were able to meet Mortenson’s schedule and put in a quality product. It ended up going very well.”
Blackman credited REHAU team members for their flexibility and innovative ideas. “I can’t tell you how many conference calls and site visits we had. They were great. They went through a lot of revisions, both for design issues, as well as constructability issues,” he stated.
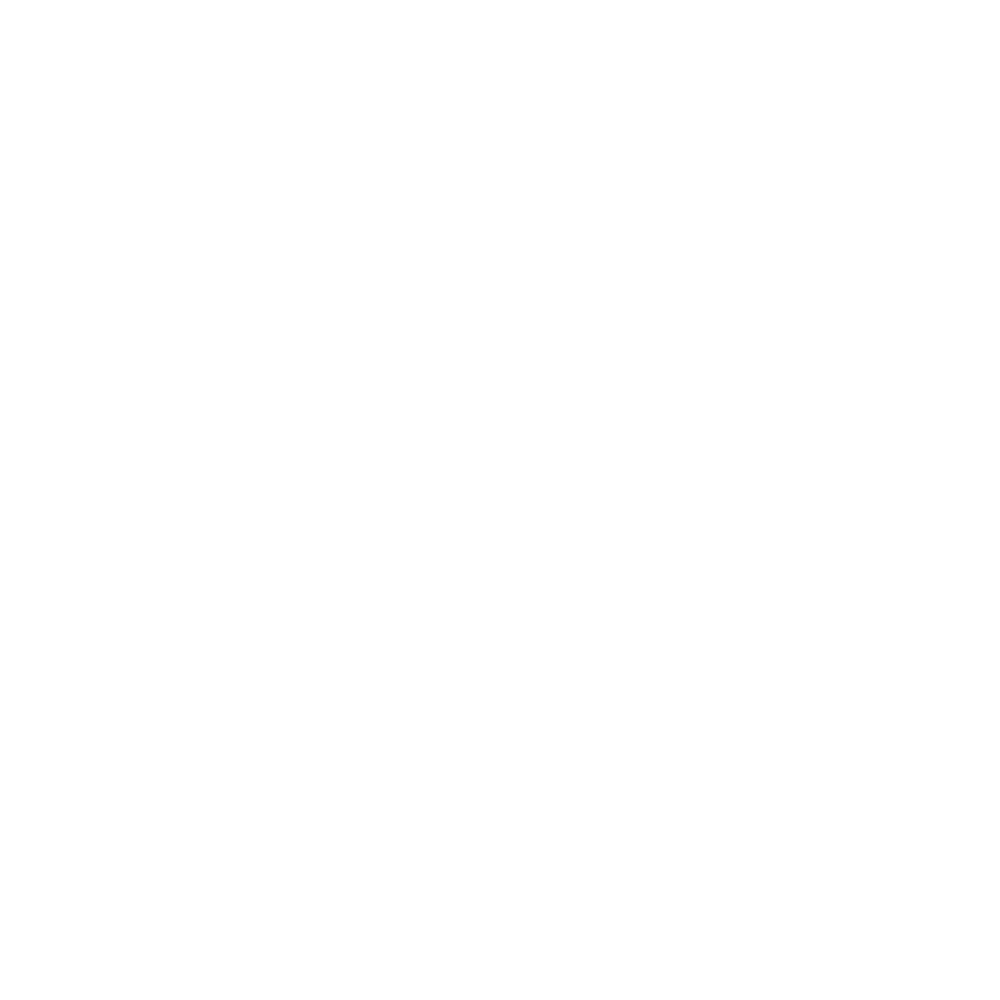
Manifolds with actuators were used to zone the PEX-based system. Image courtesy of REHAU