journal highlights
Jonathon Foreman
ACerS journals managing editor
Routes to raw material sustainability in ceramic and glass production
When considering raw material supplies, sustainability has many components. Among these are
- Substantial natural supply or replenishable source;
- Reducing the resources needed to obtain, process, and transport the materials; and
- Minimizing the environmental damage during extraction, processing, and disposal.
These goals can be achieved through several routes, such as local sourcing, using waste materials in the production of new products, and substituting low-emission materials for ones that are more highly polluting. The challenges to using such raw materials include developing processes that accommodate inconsistent composition (e.g., impurities in a waste stream) and physical properties, such as particle size and crystal structure.
Though finding and utilizing alternate sources of high-value materials, such as rare earths, dominates the headlines, high-volume traditional ceramic applications are benefitting now from the research into identification and adoption of alternate types and sources of raw materials. For example, the open-access article by Kriven et al., “Why geopolymers and alkali-activated materials are key components of a sustainable world: A perspective contribution,” provides a look at “the transformative potential” of geopolymers and other materials to provide better properties for construction materials with lower environmental impact.
Furthermore, in the open-access article “Alternative raw material research for decarbonization of U.K. glass manufacture,” Deng et al. describe the potential for substantially reducing carbon dioxide emissions in glass production by incorporating ancient raw materials—namely biomass ash—into modern processes. They found the simple steps of sieving and washing the ash substantially reduced impurity content. Additionally, they showed that adding approximately 5% biomass ash to green soda-lime-silica container glass batches has little impact on the color and redox state of the resulting glasses.
Utilizing local resources is particularly important in emerging market countries to take advantage of readily available materials and to minimize transportation resources and costs. In the paper “Sustainable activation of pumice with partially variable substitutions of metakaolin and/or fumed silica,” Turkish researchers Bagci and Kafkas collaborated with Samuel and Kriven in the U.S. to prepare geopolymers with alkali-activate local pumice as a raw material. Mixing the activated pumice with metakaolin yielded more geopolymer than mixing with fumed silica and resulted in higher compressive strength.
Also, in Africa, many of the millet growing countries are grappling with serious environmental challenges posed by the accumulation of unmanaged waste in tandem with their population growth and urbanization rate. The authors of the open-access article “Use of waste husk from millet grain cultivation in the production of fired clay bricks” formulated bricks using different ratios of waste millet husk along with locally sourced grey clay and laterite (Figure 1). The authors conclude that the husk could be used as a pore former in processing bricks with good thermal and mechanical properties for load-bearing construction applications.
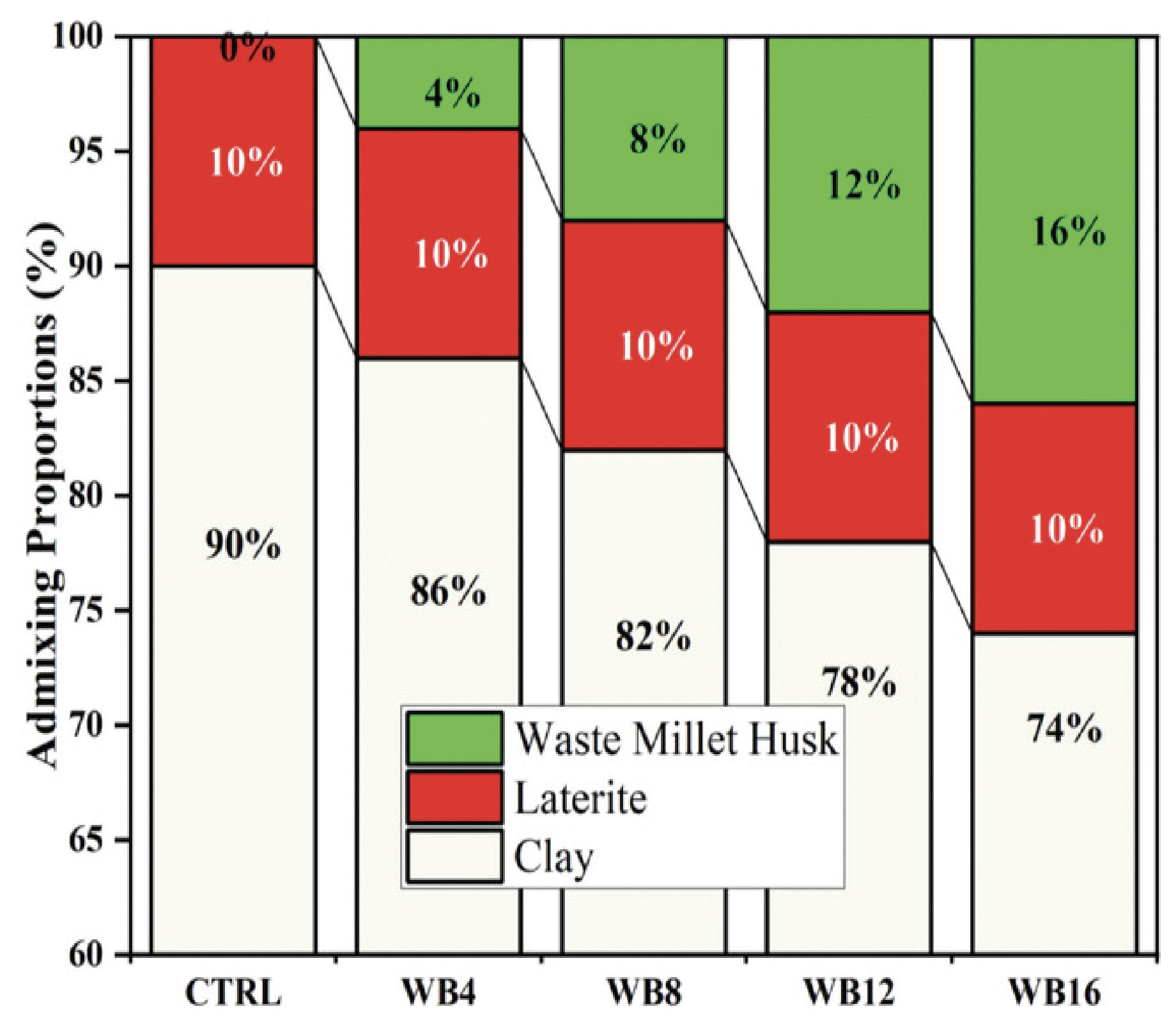
Figure 1. Raw materials admixed ratios of various brick series.
Credit: Adazabra and Viruthagiri, International Journal of Ceramic Engineering & Science (CC BY 4.0)
Reclaiming waste from manufacturing provides dual benefits. It can reduce disposal volumes and costs while providing inexpensive raw materials for other processes. The articles by Fang et al. (“Effect of Fe2O3 additive on the preparation of Si3N4−Si2N2O composite ceramics via diamond-wire saw silicon waste”) and Jiang et al. (“Preparation of nano SiC by carbothermic reduction of silicon cutting waste with phenolic resin”) mention that the process of cutting high-purity silicon ingots into wafers for solar photovoltaic cells is highly wasteful. Cutting silicon results in up to 40% of the ingots, or about 160,000–200,000 metric tons annually, being converted to powder. Because the silicon powder is contaminated with carbon and metal oxides from the cutting tools, it is difficult to reuse in the photovoltaic application and often becomes hazardous waste. However, according to the authors of the two articles, the composition of these powders does not hinder—and may even be beneficial for—conversion to high-temperature silicon nitride carbide and silicon carbide ceramics, respectively.
The Topical Collection “Sustainable ceramic and glass raw materials” can be found on the ACerS Publication Central hub. Click on the “Collections” menu and select “Topical Collections” from the drop down. You will see this collection along with others created over the past few years. You can also directly access this collection.