Paths to commercialization: Bridging the gap between research and market
By David Holthaus
Basic research often has its beginnings with an elemental wonder at the world around us. In the case of Richard Riman, professor of materials science and engineering at Rutgers, the State University of New Jersey, pondering how crystals grow in caves, how ice crystallizes in beautiful and transparent shapes, and how snow solidifies into ice started him thinking about the kind of work he would like to do as a research professor.
Perhaps there was a way to make ceramics using water instead of high-temperature furnaces, he thought. He studied how engineers densified arctic fields of snow and ice to create airplane landing strips and how shellfish make ceramics at low temperatures. Reviewing the literature, he found work conducted by researchers in Japan using water. However, this approach still required high temperature and high pressure.
Further research found other scientists in Japan using low-temperature densification, compacting materials together with the assistance of water to densify them. But Riman pondered, “What can I do that’s really different from what they’re doing?”
ADVERTISEMENT
This pondering led Riman and Vahit Atakan, a former Rutgers doctoral student, to invent an energy-efficient technology that harnesses largely low-temperature, water-based reactions. Called hydrothermal liquid-phase densification, the technology creates bonds between materials at low temperatures.
Riman used this densification process to create a range of ceramic composite materials. But during a mid-career sabbatical from Rutgers, he began thinking about how to use this technology for the common good.
“I went through this whole life evaluation process,” he says. “I asked myself, ‘Have you made a real difference in what your research has done?’”
He had published numerous research papers, made many presentations to professional organizations, and even licensed technologies to corporations. But these collaborations never made it to commercial production.
Around the time hydrothermal liquid-phase densification was invented, Riman met people in the venture capital community who were investigating laboratory research in search of investment opportunities. One was Bill Joy, a computer engineer, venture capitalist, and cofounder of Sun Microsystems, a Silicon Valley technology company.
At the time, Joy was a partner in Kleiner Perkins Caufield & Byers, the storied Silicon Valley venture capital firm. With Joy and others at Kleiner Perkins steering the densification process toward commercialization, they formed a company called Solidia Technologies in 2008 focused on commercializing the technology for the concrete and cement industry, a huge global market.
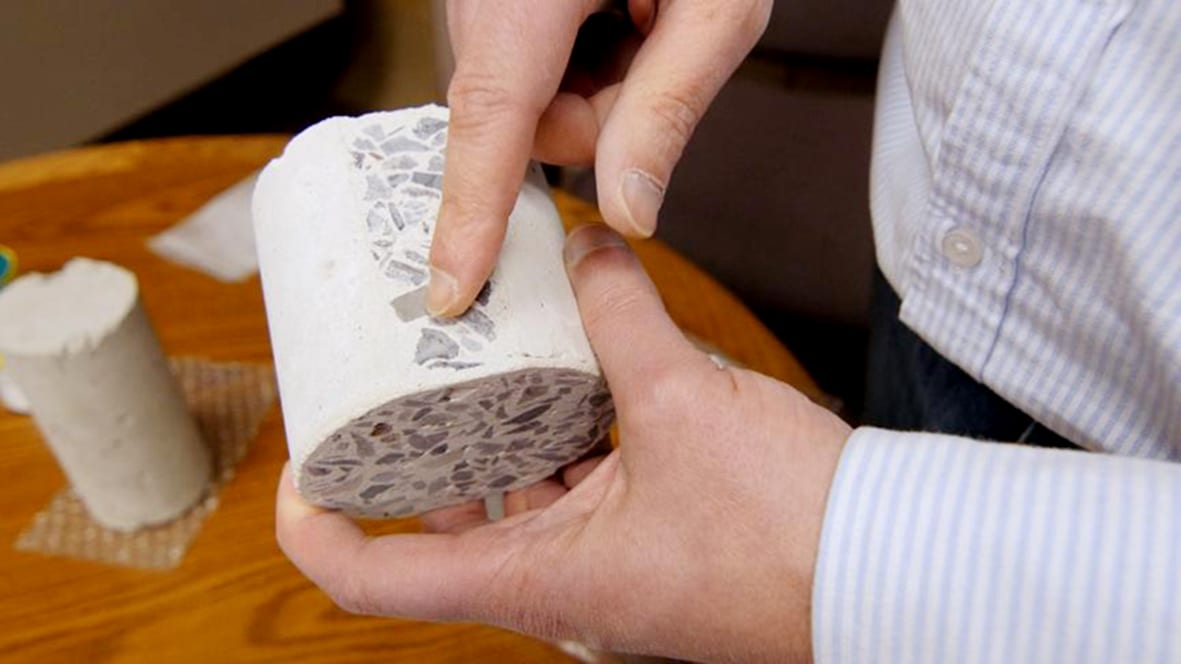
Riman’s technology has been used to make more than 30 different materials, including concrete that stores carbon dioxide. Credit: Cameron Bowman, Rutgers University
Originally based in Piscataway, N.J., and now based in San Antonio, Texas, Solidia Technologies markets eco-friendly cement and concrete for construction and infrastructure. Riman and colleagues demonstrated that they could make a material that costs the same as conventional Portland cement, with the same strength and durability, and reduce the carbon footprint of the materials by up to 70%.
Earlier this year, the company entered a technology licensing arrangement with CalPortland Co., one of the largest building materials producers in the Western U.S., for patents that enable up to a 50% reduction in the carbon footprint of cement and concrete. CalPortland also purchased some laboratory and plant assets from Solidia.
Teaming with investors like Riman did is just one way to commercialize research. The process of commercialization can transform scientific discoveries into new products and services, drive economic growth and job creation, generate revenue that can be reinvested into further research, and potentially lead to breakthroughs that can solve real-world problems.
There are many examples of research from ceramic and glass laboratories being successfully transitioned to commercial products. Among them are advanced materials developed for dental applications, which companies such as Zurich-based Nobel Biocare and Basel-based Straumann have commercialized into dental implants and crowns. Ceramics suitable for ballistic protection due to their extreme hardness and lightweight properties have been commercialized for use in body armor and vehicle armor. Also, carbon-composite ceramics are now used in high-performance applications, such as jet engines and spacecraft.
Partnerships with industry
Like Riman, addressing the global problem of climate warming was also a driving force behind professor John Mauro’s research into inventing and engineering a new family of glass at The Pennsylvania State University.
By far, the predominant type of glass produced around the world is soda lime silicate glass. It is used for windows in homes and offices; for automobile windshields; and for tableware, jars, and beverage packaging. The production of soda lime silicate glass produces millions of tons of carbon dioxide every year, largely because of the energy required to heat furnaces to the high temperatures needed to melt this glass. In addition, both the soda ash and limestone used to make soda lime silicate glass are carbonate, and they both decompose into oxides and release carbon dioxide during the glass melting process.
“Soda lime silicate is ubiquitous, and it has not changed in a very long time, and it is responsible for the lion’s share of the CO2 output of the glass industry,” Mauro says. “So, if we want to be serious about reducing the carbon footprint of the glass industry, we need to do something about soda lime silicate glass.”
There are few who are more qualified to do that than Mauro. During his 18-year career at Corning Inc., he co-invented Gorilla Glass, the thin, light, damage-resistant material now used in a wide variety of display technologies, personal electronic devices, and optical communications globally. After his stint at Corning, he brought his expertise to Penn State in 2017, where he is a professor of materials science and engineering.
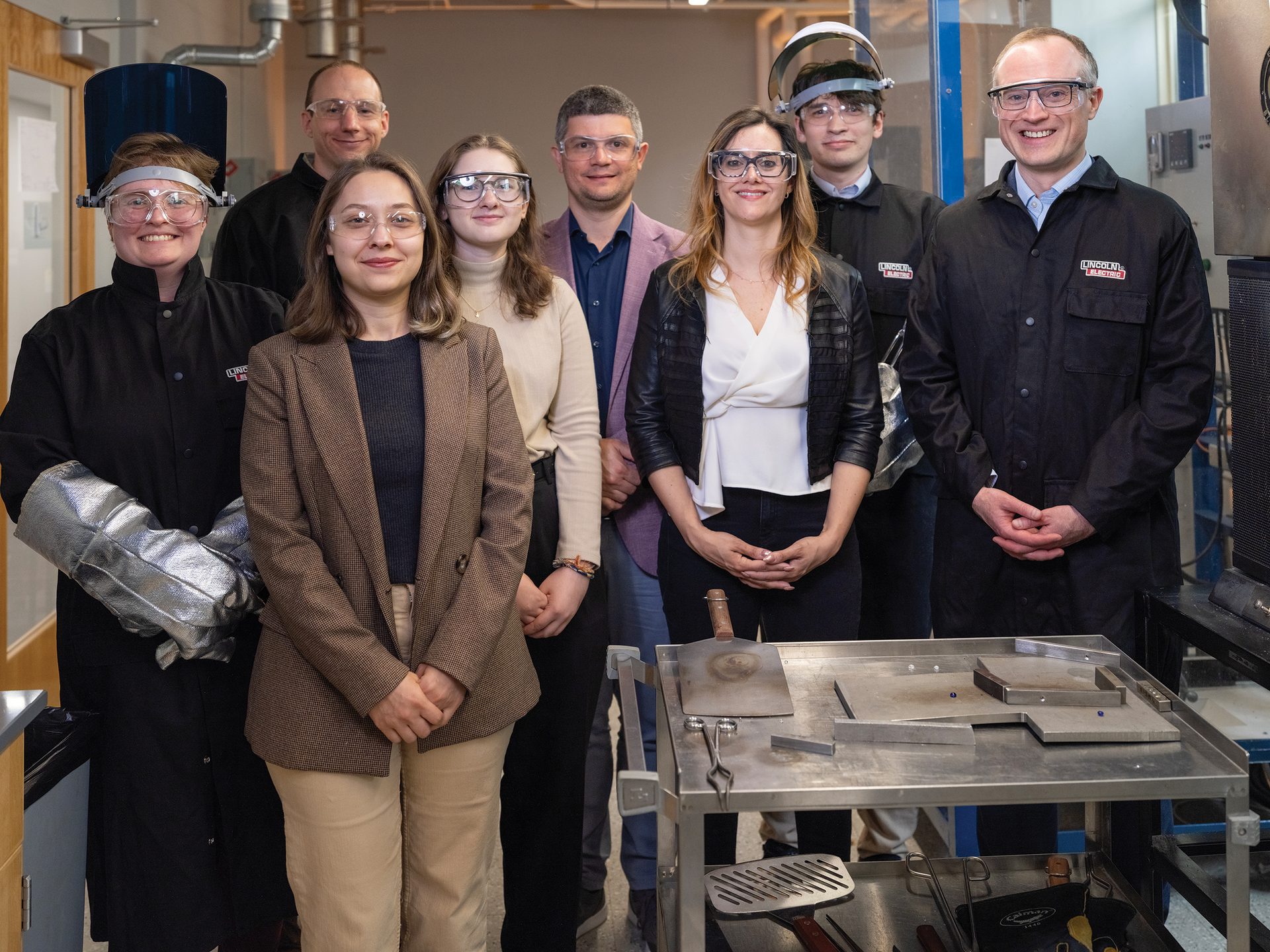
Penn State’s partnership with Bormioli Luigi will focus on scaling up LionGlass to create bottles for luxury beauty products. From left to right: Brittney Hauke, doctoral student; Titus Reed, doctoral student; Elif Akman, doctoral student; Elizabeth Aichele, undergraduate student; Andrea Marostica, Bormioli Luigi; Elisa Biavardi, Bormioli Luigi; Nicholas Clark, postdoctoral scholar; John Mauro, Penn State professor. Credit: Michael Owen, The Pennsylvania State University
In the university environment, Mauro was free of the profit-driven incentives of the corporate world and able to focus on passion projects. This academic freedom allowed him and his students to experiment with developing a glass that could serve as an environmentally friendly alternative to soda lime silicate glass.
Through these experiments, “We designed a glass called LionGlass that significantly lowers the melting temperature and eliminates the use of carbon batch materials,” Mauro says.
LionGlass, named after Penn State’s Nittany Lion mascot, is not based on the age-old mixture of quartz sand, soda ash, and limestone. Instead, it is based on phosphate materials and has a lower melting point than soda lime silicate glass. These two factors mean LionGlass has the potential to cut the carbon footprint of glass making in half, Mauro says.
LionGlass also has the added benefit of improved damage resistance compared to soda lime silicate glass. This benefit means that the glass can take a lot more stress before it cracks, “which means that the mechanical performance is better,” Mauro says, and allows for “thinner walled glass products instead of having thick-walled glass jars.” That design change could further reduce the carbon footprint by lowering the carbon emissions used to transport the glass.
With its intellectual property protected by patents, Mauro and Penn State are pursuing another path to commercialization—partnerships with industry. Mauro and his lab have built partnerships with corporations that include glass manufacturers and customers of the glass industry, and they are working with industry to tests the limits of LionGlass to see how it can be used in the real world.
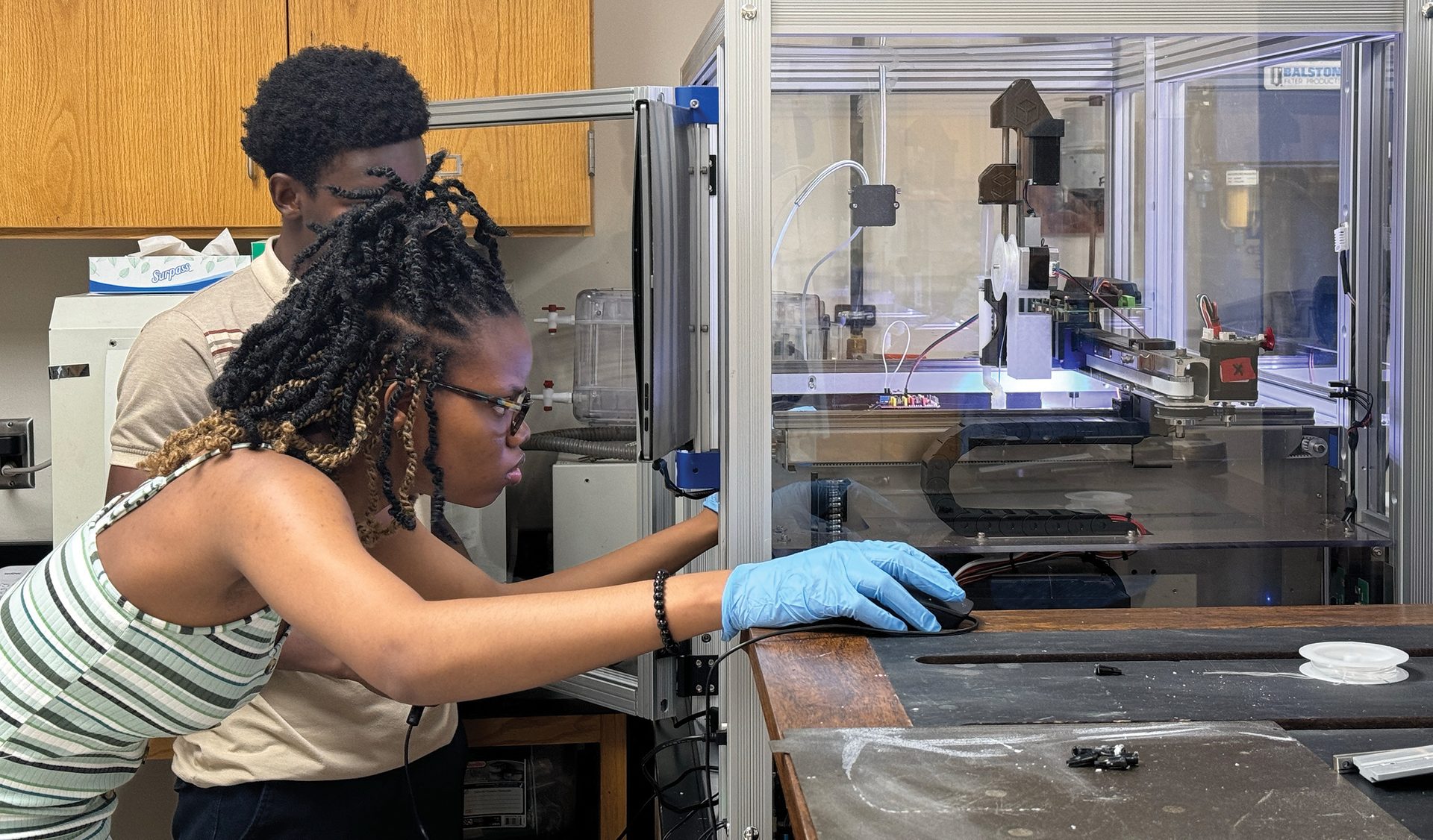
Alfred University and other colleges can provide talent as well as equipment to research and test new processes and materials. Credit: Alfred University
Scaling up
After securing the patents for Penn State, the next key step was getting the word out to companies about the new process. Penn State’s marketing group was instrumental in that, as several news outlets and trade publications published stories. The marketing effort resulted in meetings with nearly 50 companies to review the technology under confidentiality agreements, Mauro says.
In September 2024, the Penn State researchers announced they had secured their first corporate partner, a move toward bringing the ecofriendly alternative to the marketplace. The partnership is with Bormioli Luigi, an Italian glassmaker that specializes in producing high-end packaging for fragrance, cosmetics, and tableware. The company will work with Penn State to perform research and development with the goal of scaling up, manufacturing, and ultimately commercializing LionGlass.
The partnership will focus on using LionGlass to create bottles for luxury beauty products such as cosmetics and perfume. By focusing on a smaller, high-end market, the company can fine-tune the glass and determine the feasibility of scaling it up further for other uses, the company says.
In the lab, LionGlass is made in small batches using crucibles placed in high-temperature furnaces. But to produce LionGlass at an industrial scale, it will need to be melted in large batches inside massive furnaces and formed using molds, something that is still being tested with the new family of glass. The first year of the partnership will be dedicated in part to testing the feasibility of using the molding technique with LionGlass in Bormioli’s existing manufacturing infrastructure.
“We are working closely with them to get this glass ready for pilot scale manufacturing,” Mauro says. “That will hopefully take place next year, and it will demonstrate the ability to melt this at a large scale. It will also provide some prototypes that they can pass along to their customers to get their feedback, and it will also provide a much larger amount of samples that we can use for further testing.”
The Penn State team is starting with a high-end specialty market such as cosmetics because, Mauro says, “They are higher margin, and also because they are willing to, I think, take a chance on new technology like this.” The next likely step, he says, will be to test the technology in the high-end spirits packaging sector. Ultimately, they plan to test it in flat glass, which requires a more complicated technology to produce.
“We want to show that this innovation is compatible with the process for making architectural glass,” Mauro says. “So, we’re in discussions with a couple of companies about that.”
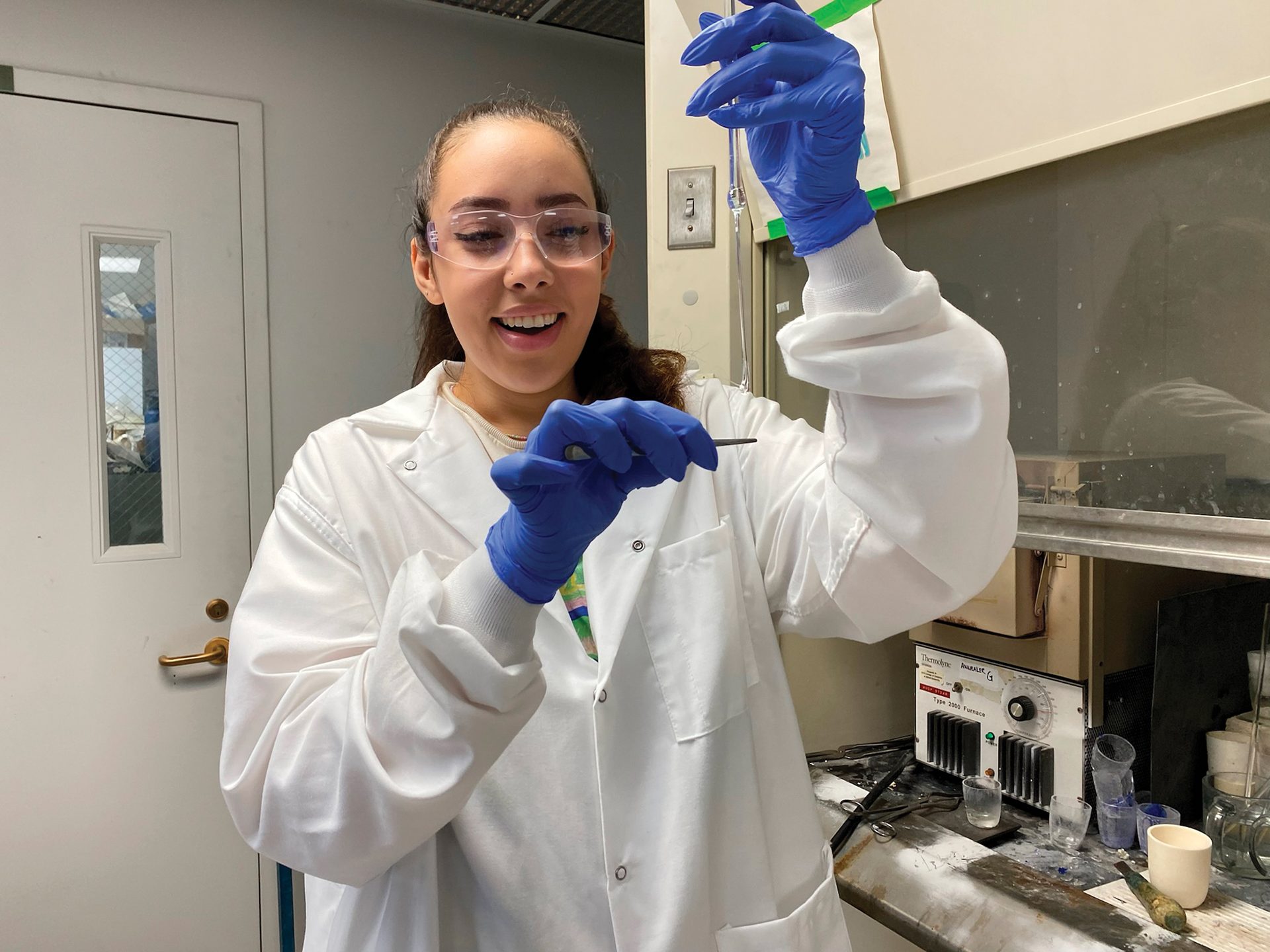
Alfred University’s Center for Advanced Ceramic Technology uses a model called SWIFT to work with industry that reduces transaction time. Credit: Alfred University
Working with academia
Mauro and his team have the benefit of the resources of a large, state-supported university as they work toward commercializing their invention. But smaller universities, such as Alfred University, can also work with industry to move research from the lab to the marketplace.
Alfred University’s Center for Advanced Ceramic Technology (CACT) is one of 15 industry centers located across New York state created to speed technology transfer from universities to the marketplace. The CACT works with firms from New York by providing financial support to offset short-term analytical programs as well as sponsor research, internships, and workforce development programs. For New York companies, the typical cost-share support ranges from 20–30%. The Center also works with out-of-state firms but, as a state-funded program, cannot apply a cost share to those projects.
Alfred, with an undergraduate enrollment of only about 1,500, does not have a dedicated office of technology transfer, nor does it invest in patenting, says David Gottfried, director of the Center for Advanced Ceramic Technology. Supporting patent applications, maintaining them, and defending them can be expensive.
“It’s almost better to treat them as trade secrets rather than as published patents when you’re working in a lot of these materials because with patents you’re just putting your formulations and other things out into the open, and that doesn’t really make a whole lot of sense,” Gottfried says.
Alfred uses a model employed at the University at Buffalo, called UB SWIFT, where SWIFT stands for Sponsorship With Industry-Focused Terms. The approach is an option to sponsor research through an agreement that includes preferred licensing terms for intellectual property that results from the project.
Gottfried says the approach allows both entities to set research and licensing terms at the project planning stage, providing financial certainty for both parties, eliminating ongoing and costly negotiations, and drastically reducing transaction time.
“It’s all about getting intellectual property into the hands of industry, where they will commercialize it and produce value,” Gottfried says.
Gottfried explains that if a company licenses a technology or utilizes a technology that was developed through its work with the Center, it can have an exclusive right to use the technology and generate $25 million of royalty-free revenue. Beyond that, a very small royalty accrues to Alfred University.
“It makes agreements with an industrial partner very easy on everyone and also extremely low-cost in terms of any payments back to the University in the form of royalties,” he says.
The Center also works with Alfred’s $7.75 million Ceramic Research, Education, and Technology Enterprise (CREATE), which focuses on supporting industry’s needs to develop and commercialize additive manufacturing and printed ceramics and glass, as well as solutions for ceramic machining and surface finishing.
Additionally, Alfred is a source of talented people, faculty, staff, undergraduate, and graduate students who are interested in hands-on experience and can provide talent to the industry, Gottfried says. Industry can also make use of the university’s equipment to research and test new processes and materials to avoid tying up production equipment to do that. For example, Alfred is acquiring a large glass furnace that can handle a 200-pound melt, significantly larger than the small crucibles it has worked with in the past.
There are several paths to commercializing basic research that can lead to breakthroughs that solve real-world problems, advancements in technology, and revenue that can support jobs and further research. Whatever the path, the ultimate goal is to translate scientific knowledge into practical applications that bridge the gap between research and markets, benefit society, and help ensure that scientific advancements have an impact on everyday life.