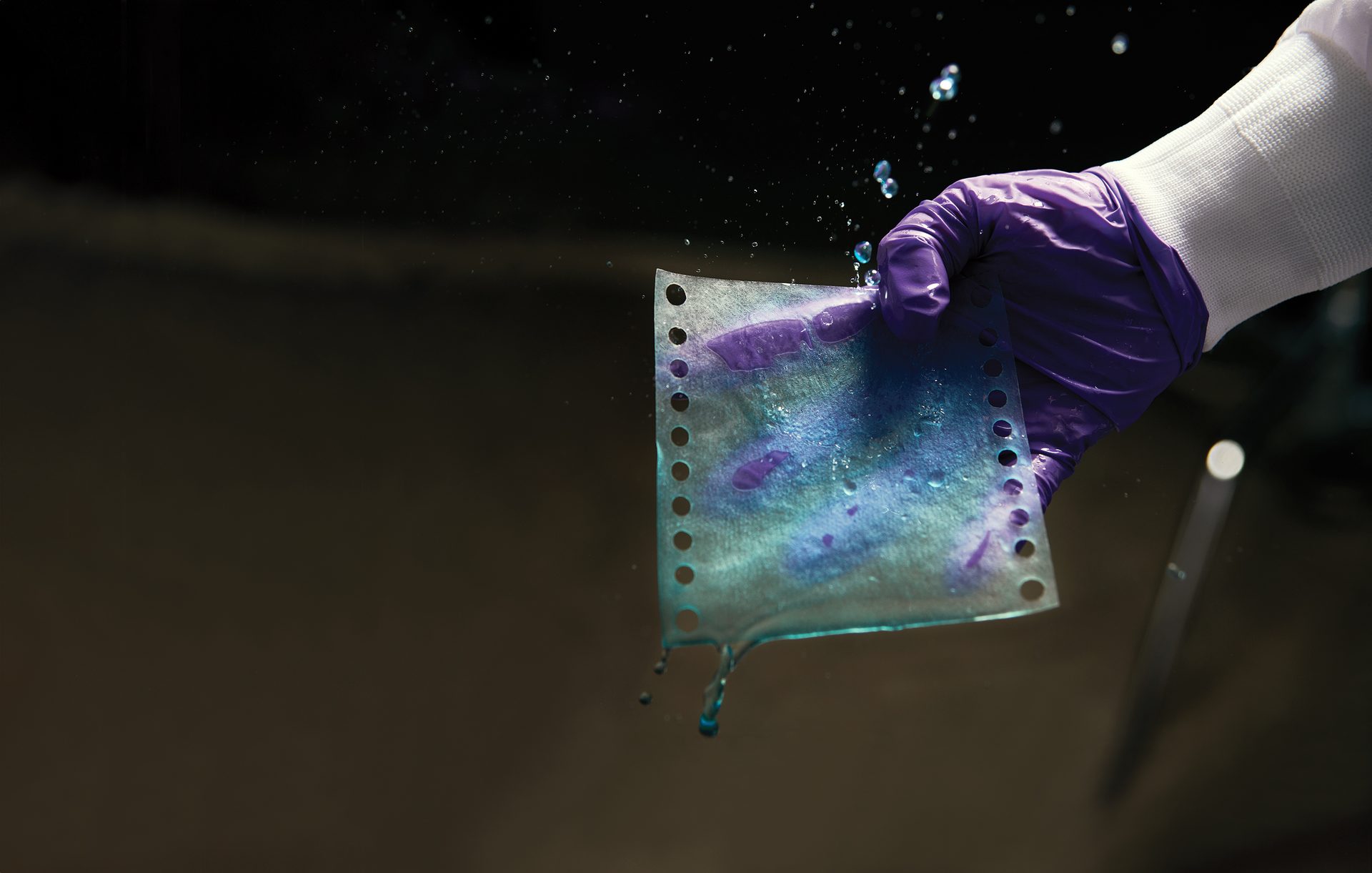
bulletin | cover story
United States of America:
Market giant with great expectations
By Randy B. Hecht
Membrion’s flexible ceramic desalination membranes, shown here, are resistant to harsh industrial wastewater.
Credit: Greg Newbloom, Membrion
U.S. companies, universities, and institutions assess the next-generation talent, technologies, and climate-friendly practices needed to sustain global leadership.
The United States has always favored people and entities who like to run on the fast track. These days, however, businesses are facing challenges that do not always support moving at full speed.
From resolving supply chain and labor constraints to adopting new sustainability standards and computer technologies, U.S. organizations are contending with a complicated environment for achieving their R&D and growth goals.
Rajendra Bordia, the George J. Bishop III Endowed Chair and professor of ceramics and materials engineering at Clemson University, has witnessed firsthand the effect of and response to these challenges in the ceramics and glass industry during his time as ACerS president (2023–2024).
For example, though artificial intelligence (AI) and machine learning methods have captured people’s imaginations with their potential for transformation, many businesses have yet to clarify how they would use these techniques and how they would get a return on their investment in it. But “I’m confident that we will start to see its implementation in terms of both product development and process optimization,” says Bordia.
Sustainable manufacturing practices, on the other hand, are already becoming embedded in product development, operations, and pursuit of emerging market opportunities.
“Ceramics and glasses have been very important in sustainability for a long time. Even if you think about a simple thing like a refractory brick used in furnaces or production facilities, its purpose is to reduce thermal losses and improve the efficiency of that particular process,” Bordia notes. “From my point of view, ceramics will be absolutely critical for sustainable and low-environmental-impact energy conversion and storage, including carbon capture and utilization.”
ADVERTISEMENT
Making these strides will require a reliable talent pool. To ensure an adequate supply of trained professionals, Bordia advocates including every generation that wants to be part of the workforce. He encourages employers to consider nontraditional approaches to late-career staff members, such as offering them the opportunity to transition to part-time work for several years before they move into full retirement.
“I think the best ideas, innovations, and advances will come from a combination of the young talent trained in these novel approaches and platforms and the older workforce’s experience in terms of what is useful and needed in the market,” he says. “They can guide and work with these younger colleagues to use the new tools to satisfy those needs.”
That is especially important from his perspective as a university professor because “we are seeing a decreased interest in what we call hardcore or traditional engineering disciplines.”
“There’s a lot of interest in computer science and a fair amount of interest in bioscience and biomedical technologies, but there is less interest in things like mechanical, materials science, chemical, and electrical engineering,” he says. He encourages companies that want to recruit from that smaller talent pool to partner with academic institutions and offer internships or co-op opportunities.
Bordia notes that ceramics will have a significant role to play not only in sustainability but also in national security and defense—and, by extension, sectors such as aerospace.
“Ceramics are critically important in everything from space exploration to hypersonic vehicles. Significant progress is being made in ceramics in electronic systems, including sensors and actuators. Biomaterials is another exciting area, particularly with the increased focus on individualized medicine,” he says.
The following sections demonstrate how these myriad market factors shape policy and decision-making at establishments both large and small through interviews with leaders in industry, academia, and the government. Despite the challenges, these experts still express a strong passion and drive to advance materials research and application in the U.S.
Overall, “It’s a very exciting time for ceramics,” Bordia says.
Industry perspectives: Startups and niche markets
Silica-necting the dots to clean water
A conversation with Greg Newbloom, founder and CEO of Membrion
“Electroceramic desalination for harsh industrial wastewater” is the sort of phrase that would not exactly have drawn a crowd at a party a generation ago. But in today’s sustainability-savvy world, Greg Newbloom and his team have a hot topic in play.
Newbloom is founder and CEO of Membrion, a Seattle-based startup focused on the reclamation of industrial wastewater. Their patented filtration and reclamation systems aim to eliminate unnecessary pre-treatment stages, offering a simplified and tailored solution for wastewater treatment.
A fresh perspective, a new opportunity
Newbloom says the Membrion team invented their solution for industrial wastewater treatment while pursuing a solution for a different application.
“Initially, we were trying to develop a membrane for use within redox flow batteries,” Newbloom says. “The membranes they use have to be in these really harsh environments with lots of acids and oxidizers. Most materials break down, and we were trying to find an alternative material that could withstand these really challenging applications.”
That path led to silica gel materials such as those used to maintain freshness in packaging and that are very good at absorbing water.
“They have molecular-size pores,” Newbloom says. “So instead of having those little silica gel beads, we made full sheets of it. We control the size of the pores and the surface chemistry, and that optimization made the sheets able to withstand these really harsh environments.”
These silica sheets, pictured in the header image of this article, became a solution in search of an alternate problem.
“While these new batteries are unique and interesting, they’re still very young in their commercialization cycle,” Newbloom says. “So as a business, we really needed to look at other applications that could benefit from those same use cases. That’s how we made our way into the water sector. We basically will remove anything that is ionic from the water stream.”
Membrion’s first full commercial system is now in operation, being used to treat wastewater for a microelectronics manufacturing company in Portland, Oregon. The solution is deployed under a “water treatment as a service” model, which means that in exchange for a fee-per-treated-gallon rate, Membrion handles water treatment operations for its customers.
Two more systems are expected to go online during the third quarter of 2024. For now, the company is focused on the North American market, but it is seeing demand for the product in Europe and Asia and may begin exploring those markets in the next year or two.
Tapping AI for data-driven performance
Like most companies, Membrion generates a high volume of data related to its processes and results monitoring. Newbloom notes that facilities do not always have a firm grasp on what their wastewater contains. With that in mind, the team is in the early stages of building datasets that can, via artificial intelligence and machine learning, increase customers’ usage and waste predictability to optimize the system’s performance. The long-term vision also includes enabling circularity of critical materials.
“In a lot of cases, we’re working with valuable metals in these wastewater streams—things like copper, cobalt, nickel—so there is value in being able to recover the water and those metals and return both back to the value chain,” Newbloom says. “That’s where our customers get their cost savings and their return on investment for leveraging our system today. And in the long run, we will partner with existing technologies to valorize these metals and return those back to the supply chain as well.”
Aiming for growth (talent pool permitting)
Newbloom says that Membrion has the production capacity in play to scale as demand grows and that “nothing outside of labor prevents us from producing more of these.”
“Our membranes are produced roll in our facility, which is a high-volume production method, so from a production rate standpoint, we’re not limited in the amount we can produce,” he says. “But as we grow and scale, getting access to incredible people is always hard. They’re in high demand for good reason.”
Newbloom anticipates that sales and field services will be the two biggest growth areas in the coming 12–18 months, and he believes the company’s sustainability strength will be a lure for people who want to “have a bigger impact—that’s something that we certainly lean into as we recruit people.”
Learn more about Membrion’s current projects and future goals.
Additive advances and ambitions
A conversation with Ryan Bock, vice president of research and development at SINTX Technologies
SINTX Technologies (Salt Lake City, Utah) develops ceramic materials, components, and technologies that historically have been marketed to the medical sector; the company notes that “its products have been implanted in humans since 2008.”
A leader in silicon nitride research and development, it has in recent years moved into additional lines of business by way of a series of acquisitions and partnerships. Today, its research facilities in Utah and Maryland are concentrated on three areas of focus: additive manufacturing of advanced ceramics and composites; traditional production of high-performance silicon nitride, biomedical, and aerospace components; and development of complex thermal barrier coatings for aerospace and energy applications.
Additive technology multiplies R&D options
“The potential with printing ceramics is a huge focus. We’re investing quite a bit in advancing our capabilities in that area in particular,” says Ryan Bock, vice president of research and development at SINTX.
Currently, the company can print alumina, zirconia, and silica ceramics. But SINTX is working to advance the capabilities to print other ceramics, such as silicon nitride.
“We subtractively manufacture silicon nitride parts today. That’s really the foundation of our company. We have traditionally done that with biomedical parts, in particular spine implants—more than 40,000 worldwide,” says Bock.
As SINTX seeks new market opportunities for its silicon nitride, it is zeroing in on what Bock calls “quality-stringent areas or industries, such as aerospace.” Areas of expanded investment and R&D activity include complex thermal barrier coatings and ceramic matrix composites. The company has been pursuing collaborations with other companies and government entities in support of its expansion plans.
Like many companies targeting substantial growth, SINTX has encountered challenges in recruiting and retaining the talent it needs.
“There are not enough people to go around, and there are no magic bullets,” Bock says.
Although the company does not recruit from specific schools, Bock says SINTX holds schools with a special focus on ceramic engineering “in high esteem,” and staff members in R&D and operations “are charged to stay in close contact with programs and key professors” at their alma maters.
Results begin with customer collaboration
Another common challenge is balancing the time demands of new solution development on one hand and post-launch customer support on the other. SINTX has adopted the strategy of bringing customers into the R&D process “as far along as they can get on the front end and bring them as far along as possible” to minimize restarts, Bock says.
That customer orientation extends to the company’s approach to sustainability, and customer requirements regarding sustainability often reflect existing and emerging industry or regulatory requirements.
“We do the testing that the customers require of us, whether it be in that area or another,” Bock says. “And we want to do what we can to make a positive impact right at a grand scale level. The great thing about our ceramic materials is that they have inherent benefits versus nonceramic materials, such as metals and polymers.”
On June 18, 2024, SINTX announced that its board of directors had “initiated a process to explore potential strategic options” and had retained Ascendiant Capital Markets, LLC as “exclusive strategic advisor” to the board in this process.1
On Aug. 6, 2024, SINTX announced the retirement of B. Sonny Bal as president and chief executive officer.2 He is succeeded in both roles by Eric K. Olson, who is described in the announcement as having been a “serial founder and entrepreneur in a broad range of medical device, diagnostic, biologic, and biomaterial companies” for more than 30 years. Bal remains chairman of the company’s board of directors.
Learn more about SINTX’s capabilities and plans for the future.
Industry perspectives: Market influencers
Long-term planning ‘drives’ a carbon-free future
A conversation with Ann Nicholson, Corning’s vice president of investor relations
Since development of the ceramic catalytic converter in the 1970s,3 Corning Incorporated (Corning, N.Y.) has helped lead the way in emissions control in the automotive and other industrial sectors. Even now, sustainability continues to drive both business and social priorities at Corning, which was named to Time magazine’s “World’s Most Sustainable Companies” list for 2024.
In an interview with Bulletin editor Lisa McDonald, Ann Nicholson, vice president of investor relations at Corning, shared insights on Corning’s current work and plans to support a greener future for the ceramics and glass industry.
Q: Which application areas are the focus of investments and advancements right now?
A: Emissions reduction—cleaning emissions from gas combustion engines—is one focus of research and development efforts. Engines are getting more sophisticated, so their emissions are changing, and regulations are continuing to tighten.
More broadly, we are investing in research to support a cleaner environment. We have research on carbon capture technologies, and then we have—and have always had—some kind of development in the energy storage space. A lot of times, renewable energy systems give you energy when you do not really need it, so you need to be able to store it for later release.
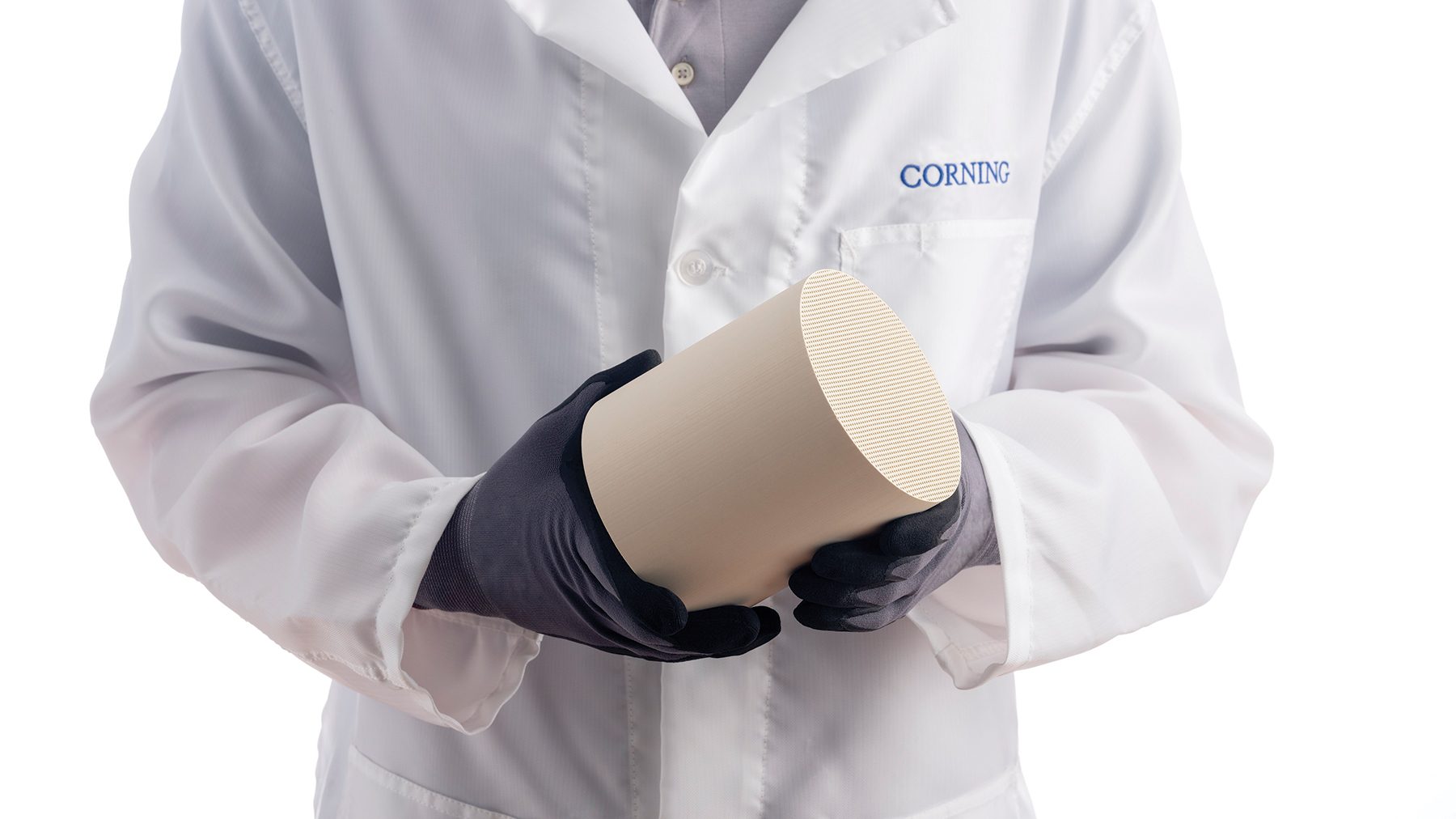
Example of Corning’s DuraTrap® gasoline particulate filter technology, which helps gasoline-powered vehicles meet the latest real-world-driving emissions standards.
Credit: Corning Incorporated
Q: Which manufacturing process steps are a focus for innovation?
A: We do not disclose anything specifically, but two broad categories are 1) improving yields so we are throwing less stuff in a landfill and 2) diverting materials from the landfill and recycling them back into new products. We do that with glass. We make a sheet of glass, trim the ends, and put those trimmed ends right back in the tank.
In addition, one of the biggest sources of energy usage during the manufacturing process is in the firing. We have engineers and scientists that focus on things such as burner technology to make the process more energy efficient.
Q: What are some of the biggest benefits and challenges to materials innovation within the United States?
A: The way we are organized, there are lots of opportunities to exchange information. We have a centralized research facility, and each of our scientists are involved in multiple projects. They work on teams that include ceramic engineers, mechanical engineers, and industrial engineers, among other specialties. So, there is ample opportunity to learn from different people and cross populate ideas.
The challenge is sometimes work–life balance. From a cost perspective, it makes sense for us to be in the region where the customer is. So, we have facilities in Europe, the U.S., and Asia, but that means you can be on the phone 24 hours a day. We recognize work–life balance is important, and we encourage our scientists to balance their schedules.
Q: Do differing regulations between various countries or regions affect your ability to conduct research and innovate?
A: We do not view regulations as limiting factors on innovation but more as guidelines to push us to be better, innovate more, and give our customers what they are looking for so that it meets those standards.
Innovation can take time, and it is hard to invent on a schedule. So, a key to navigating new regulations is to be looking ahead and anticipating those changes. For example, who is working on the next generation of emissions engines? Or what is happening in the world of hybrid vehicles? We call that planning “technology roadmaps.”
Q: Looking ahead, what other developments is Corning prioritizing?
A: We have worked on emissions control within the automotive industry for decades, but we continue to explore other sectors where this technology can apply. We also have some teams looking at developing technical glasses to replace soda lime glass in certain applications.
Learn more about Corning’s sustainability initiatives in the company’s 2023 Sustainability Report.
From home-grown to global competitor
A conversation with Chris Kraft, senior director of thermal and foundry commercial operations at HarbisonWalker International
As North America’s biggest supplier of refractory products and services, HarbisonWalker International (HWI) serves a customer base that spans such industries as iron and steel, aluminum, copper and heavy nonferrous metals, ferrous foundry, glass, power generation, refineries and petrochemicals, chemicals, gasifiers, incineration, cement, pulp and paper, and lime.
Since February 2023, HWI has been part of Calderys Group, which has opened European, Middle Eastern, and African markets as well as Asia–Pacific markets to HWI solutions, including its “green steel” applications. The move makes it possible for HWI products to be manufactured at Calderys facilities that provide proximity to customers in those regions.
“As a combined organization, we can leverage what Calderys has globally and utilize that in the market in the Americas,” says Chris Kraft, senior director of thermal and foundry commercial operations at HWI. “And similarly, what we have in the Americas can be offered in Europe, the Middle East, and APAC [Asia–Pacific]. Working through that has not been without challenges: figuring out who does what and how we’re doing things. But it’s also been fun.”
Overcoming supply chain and talent pool concerns
The company has recovered well from COVID-19-era supply chain constraints, Kraft says. During that period, when conventional wisdom held that vendor diversification was key to maintaining access to materials, HWI sought to work more closely with its most reliable established suppliers. Risk management necessitated identifying alternative vendors and avoiding dependence on a single source, but “we were sticking with them through a crisis situation,” Kraft says. “That collaboration helped put us in a better position, and we’re continuing that moving forward.”
Access to talent is another story, especially at HWI’s manufacturing locations but also within the ranks of professionals at the company. The company maintains relationships with a core group of universities (among them Rutgers, Clemson, Ohio State, and the University of Missouri) to increase its access to graduating seniors through classroom guest lectures and on-campus job fairs or recruiting events. In addition, HWI’s innovation group established joint projects with research institutes and universities to advance its R&D and widen its network of contacts in the next generation of talent.
But its relationship with the outgoing generation has presented challenges as well. Earlier this year, with an eye to organization-wide succession planning, HWI offered a voluntary retirement incentive that created opportunities for younger workers. At the same time, it resulted in a loss of knowledge that available candidates cannot in all cases replace. This shift coincides with the trend toward delivery of more complex solutions that can necessitate a stronger customer support capacity.
Navigating the data dilemma
“Everyone wants to make decisions based on data, but the data needs to be converted to useful information that supports predictive analysis,” Kraft says. “As a supplier, we’re trying to understand our customers’ needs and understand where they want to go. We then try to match our capabilities to help them make better informed decisions.”
At this point, Kraft says they are not always sure exactly where they are going, or where they want to finish. Regardless, “this is very exciting to HWI, and we do believe that we are a great partner in this uncharted territory,” he says.
Sustainability figures prominently in that equation in terms of customer and internal initiatives. One significant change is in recycling of unused materials. Kraft recalls how 30 years ago, customers were responsible for dealing with their stores of unused bricks. Today, HWI is developing programs for dealing with those surpluses in an environmentally responsible manner. The company is also analyzing its energy and water consumption, exploring waste reduction, and evaluating the impact that use of alternative fuels has on the refractories.
“New standards are being forced upon industry by regulations or standards. And when customers ask what we’re doing for sustainability, we need to be able to answer that question for various reasons, but one is because it is the right thing to do,” Kraft says.
Kraft says there is currently a lot of innovation regarding sustainability. If it all supports using less resources to do what they need to do, “That’s great. I hope that continues,” he says.
Learn more about HWI’s latest sustainability initiatives.