news & trends
Circular Supply Chain Coalition establishes e-waste recycling networks in local communities
While a lot of time is spent celebrating new technological advances, the question of what to do with these devices at the end of their life is generally less frequently discussed. But over the past decade, the topic of electronic waste, or e-waste, has become increasingly difficult to ignore.
In 2022, a record 62 million metric tons of e-waste were produced, up 82% from 2010. But even as more e-waste is being produced, less than one quarter (22.3%) of e-waste mass in 2022 was documented as having been properly collected and recycled. Without intervention, the gap between e-waste generation and recycling is expected to grow even larger by 2030, with generation growing to 82 million metric tons and recycling dropping to only 20%.
The above statistics comes from the 2024 Global E-waste Monitor report. This report is published every few years as a partnership between the United Nation’s Sustainable Cycles program and the International Telecommunication Union, the United Nation’s specialized agency for digital technology.
While there are obviously environmental risks of e-waste, there is also an untapped economic component to this complex waste stream. The 2024 Global E-waste Monitor report estimates there is US$91 billion worth of metals embedded in 2022 e-waste.
ADVERTISEMENT
If e-waste management is improved, it “could result in a global net positive of US$38 billion, representing a significant economic opportunity while addressing climate change and health impacts,” says Ruediger Kuehr, senior manager of the Sustainable Cycles program, in a press release on the report.
In May 2024, several companies and organizations announced the formation of a new coalition to encourage e-waste recycling on a local scale. The new Circular Supply Chain Coalition is governed by Pyxera Global, Sustain Our Future, and Metabolic, with FedEx directing the implementation.
As explained on the coalition’s website, modern waste infrastructure is often placed in low-income neighborhoods, and jobs managing discarded materials usually pay subpar wages. The founding partners “aim to change the situation by creating systems that distribute material value through networks rooted in and powered by frontline communities.”
They plan to establish networks of small businesses and nonprofits within a given city to process the e-waste, and then the networks will sell the recovered materials to a large clean energy technology manufacturer through a forward procurement financial mechanism called the circular services agreement.
To test the feasibility of this concept, the founding partners ran a five-month pilot program in Lebanon, Tenn., that ended in March 2024. The program provided consumers with free FedEx shipping labels to mail in their used laptops and tablets to the Electronics Reuse and Recycling Alliance, a Nashville-based information technology scrap management company, which collected the items and wiped the hard drives.
According to a GreenBiz article, the founding partners currently are planning to establish logistics hubs in Phoenix, Ariz., Atlanta, Ga., and Cleveland, Ohio. They are seeking new partners to help establish these and other local networks.
Solar panel breakage on the rise
Even as governments and companies around the world race to embrace solar energy to reduce their carbon emissions and help curb climate change, the increasing frequency and severity of hailstorms stymies installation in hail-prone regions that could greatly benefit from this emerging energy source, such as the Great Plains of the United States and the Pampas in northern and central Argentina.
To improve the resistance of photovoltaic modules to hail damage, thicker front glass panels is an excellent approach, as shown in a September 2023 CTT that summarized a study by researchers in India and Hong Kong. Yet paradoxically, the recent trend in solar panel manufacturing is to make the glass thinner than before. This decision has led to an increase in spontaneous glass breakage even under normal conditions of use, as detailed in the Renewable Energy Test Center’s sixth annual PV Module Index Report.
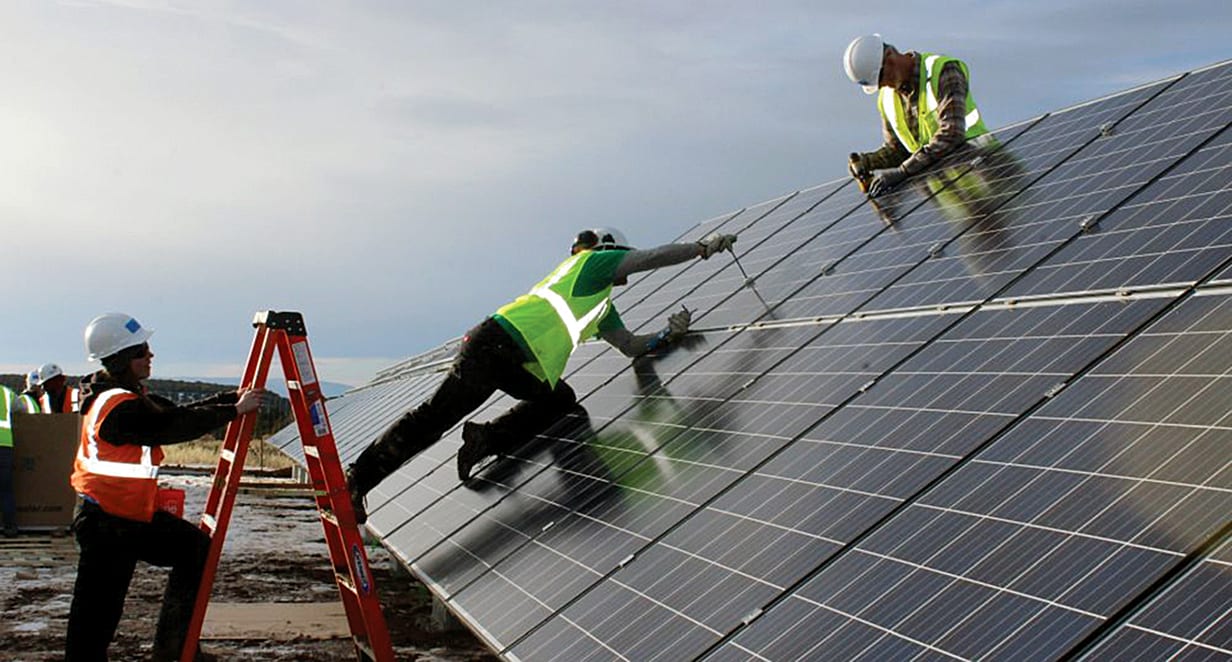
Solar installers and volunteers construct a community solar array in Norwood, Colo. Installation of solar panels in the U.S. Great Plains region is hindered by the increasing frequency and severity of hailstorms.
Credit: U.S. Department of Energy, Flickr
The report, which published in June 2024, discussed the phenomenon of spontaneous glass breakage with Teresa Barnes, who manages the Photovoltaic Reliability and System Performance group at the National Renewable Energy Laboratory.
In the interview, Barnes notes that when she first started working on solar module reliability seven or eight years ago, she mostly heard about glass breakage in cases of sloppy operations or maintenance practices. Now, though, “People are seeing glass breakage for no apparent reason, often before commissioning,” she says.
While these field reports are anecdotal, they mirror reports coming from the testing labs.
“It used to be the case that modules would pass the IEC 61215 static load test with a big safety factor. Today, modules are either barely passing the base static load test or they are not passing with higher safety factors. Some new module designs are simply not passing the minimum static load test,” Barnes says.
The reason thinner glass panels experience this failure mode more often than standard or thicker panels is because it cannot be fully tempered, Barnes explains.
“… [Any] manufacturer can temper glass that is 3 mm or thicker because it is relatively easy to get the thermal differential to build the stress profile you need,” she says. “However, it is more difficult to fully temper glass below a thickness of 3 mm. If you do not have a good temper on the glass, it is relatively easier for the glass to break.”
In addition, Barnes notes that the way people are cleaning or grinding around the edges of the glass may cause more rather than fewer defects, “perhaps making this thinner glass even more sensitive to breakage.” Plus, the concurrent trend of developing ultralarge modules results in the glass bearing more of the load, “which may be bad because we have made the glass weaker,” Barnes says.
Fortunately, it appears that manufacturers are becoming more aware of the drawbacks that come with ultrathin module design. Barnes says that at this year’s PV Module Reliability Workshop, hosted annually by the National Renewable Energy Laboratory, manufacturers reported a trend back toward thicker frames and wider mounting rails to help optimize how loads are balanced out.
You can download the full 2024 PV Module Index Report here.
Corporate Partner news
- CeramTec revives SPK brand, expands machining offerings: CeramTec announced that all machining activities will now fall under the name SPK by CeramTec. This name pays homage to the company Südplastik Gummi-und Kunststoff-Verarbeitung GmbH (SPK), which was one of the original companies acquired to form today’s CeramTec. Read more.
- Elkem Materials announces new vice president of corporate communications and public affairs: Elkem Materials Inc., a provider of advanced silicon-based materials, welcomed Marianne Stigset as vice president of corporate communications and public affairs. Stigset will be “instrumental in fostering strong collaboration with Elkem’s key stakeholders and enhancing our strategic positioning as a leading, global player within sustainable silicon-related products,” says Elkem CEO Helge Aasen. Read more.
- NSL Analytical Services acquired by Levine Leichtman Capital Partners: In June 2024, NSL Analytical Services announced that it will be acquired by Los Angeles-based private equity firm Levine Leichtman Captial Partners. NSL provides materials testing for a wide range of sectors, including aerospace and defense, electronics, advanced materials, and more. NSL laboratories will remain based in Cleveland, Ohio. Read more.
- Rauschert works to purify wastewater with zero liquid discharge approach: Rauschert Industries Inc., a manufacturer of technical ceramics, plastic molded parts, and functional components, is working to develop special ceramic membranes for a zero liquid discharge approach in hospitals to purify and reuse wastewater. Practical implementation of the approach is being tested by researchers in the Department of Psychiatry and Psychotherapy at Jena University Hospital. Read more.