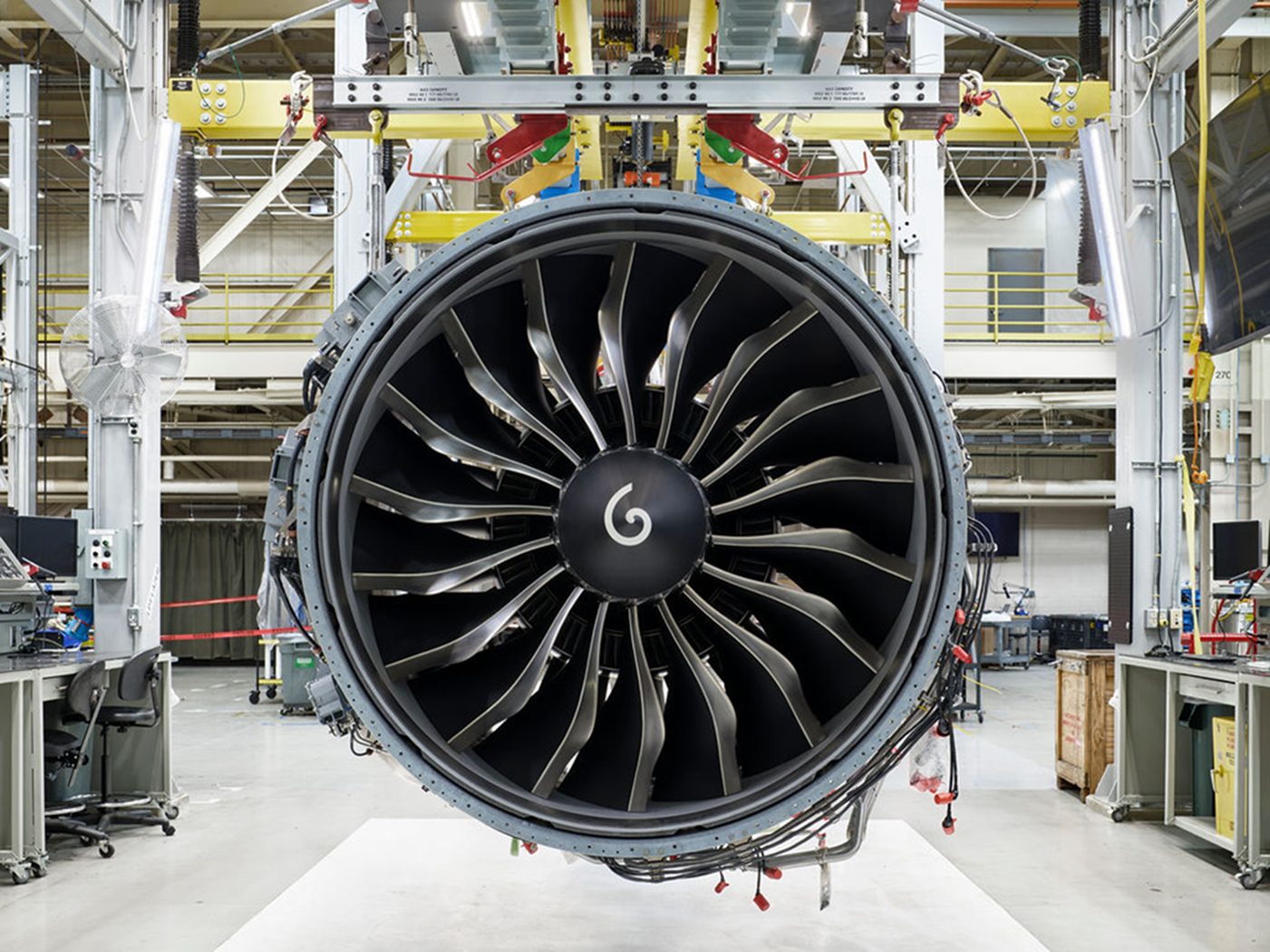
Ceramic matrix composites: Is the future here yet?
By David Holthaus
Ceramic matrix composite (CMC) technology has long held the promise of solving some of the most fundamental yet perplexing challenges in the materials industries.
CMCs are created by embedding coated fibers about the width of a human hair into a ceramic matrix. Coating the fibers alters the bond between fiber and matrix, permitting the material to be more durable. Cracks from the surrounding material do not propagate into the fibers, so the material holds together in service environments and avoids catastrophic failures.
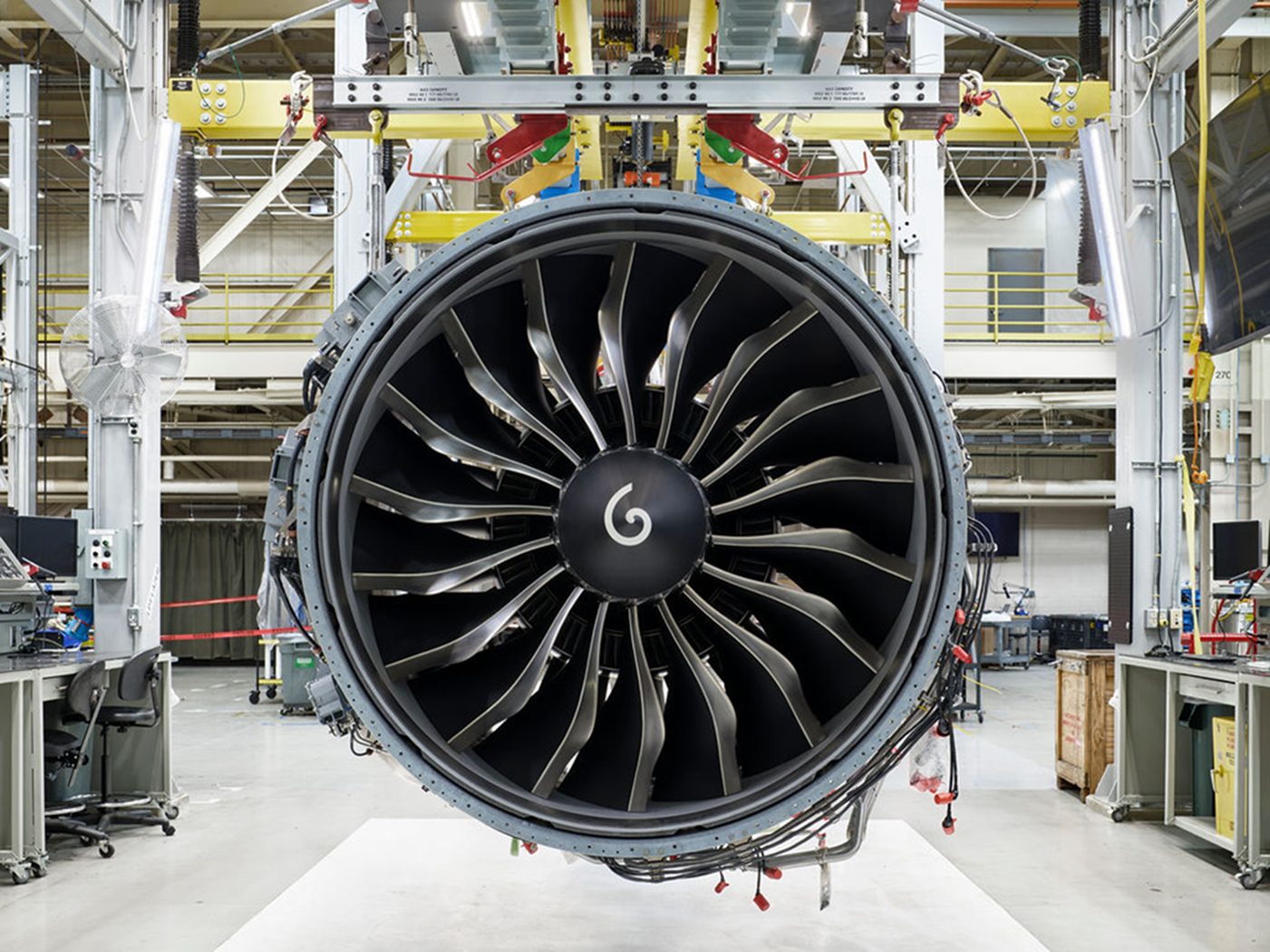
GE’s LEAP engine at the assembly plant in Durham, N.C. Credit: GE Aerospace
CMC technology has been the subject of decades of research and testing at leading manufacturers, national laboratories, and universities. The sustained interest in CMCs stems from the fact they are typically one-third the density of metal alloys and one-third the weight. They are also more heat resistant than metals and can be very durable in extreme environments.
The decades of CMC research have led to application of the technology in aerospace, power generation, transportation, and defense—and subsequent gains in competitiveness, efficiency, and sustainability in these industries. But though CMC technology has been tested, adopted, and put into commercial use in many areas, the technology is still considered to be in an early stage of development. Promising research is underway that is expected to lead to broader application in a range of industries.
SIDEBAR
Global market for CMCs
The lighter weight, durability, and heat resistance of CMCs has made this technology a subject of investment, research, and application in the aerospace, automotive, and energy industries. Unsurprisingly, all this investment is causing the global market for CMCs to expand.
An informal survey of market forecasts showed global market growth of CMCs is estimated to range from a 9.6% consolidated annual growth rate to 11% over the next five to seven years. Estimates vary, but three market research firms forecast the global market will grow to at least $21.5 billion in five years.
Driving that growth will be increases in demand in the automotive sector, which is seeing a surge in demand for lightweight and electrified automobiles, and the aerospace sector, where the airlines and engine makers are searching for more powerful yet lighter weight engines and aircraft.
ADVERTISEMENT
The early days of CMCs
Research into CMCs goes back at least three decades, but it was advanced in the early 1990s when the Department of Energy funded its Continuous Fiber Ceramic Composite (CFCC) program, which supported research and development that was going on at private corporations, including Dow Chemical, Dow Corning, DuPont, and GE. The program funded companies to make composites, which were then characterized at national labs and universities. The researchers were working toward a common goal of getting CMCs into industrial applications, including high-pressure heat exchangers, land-based turbines, heat-treating furnaces, and radiant burners.
The efforts at that time were coordinated and funded through Oak Ridge National Laboratory (ORNL), where researchers studied different fibers, coatings, and matrices, as well as how the materials degraded and performed, and cost-effective techniques for preparing them.
GE researchers have worked with CMCs since the ’70s. They initially studied the technology’s application in gas turbines, which then found its way into industrial power plants. Researchers at the industrial conglomerate then turned their attention to the company’s jet engine manufacturing and the possibility of using CMC technology in flight.
They were undeterred by a 2001 study done by the Institute of Defense Analyses for the Defense Advanced Research Projects Agency. The study assessed the potential use of CMCs in the development of military supersonic aircraft, which would require a lightweight, efficient engine that could operate at high pressure. The study, titled “Will pigs fly before ceramics do?,” ultimately concluded that “What is needed is a more radical, unconventional approach toward designing turbine engines that will take better advantage of ceramic materials properties … if the present mindset in technology development continues, there may be more pigs flying than ceramics in the future.”
Two decades later, GE has invested more than $1.5 billion in CMC research and development. The company’s CMC technology has found its way into the LEAP engine, the first widely deployed CMC-containing product. CMCs are used in the hottest section of the LEAP engine, which is made by CFM International, a joint venture between GE and Paris-based Safran Aircraft Engines.
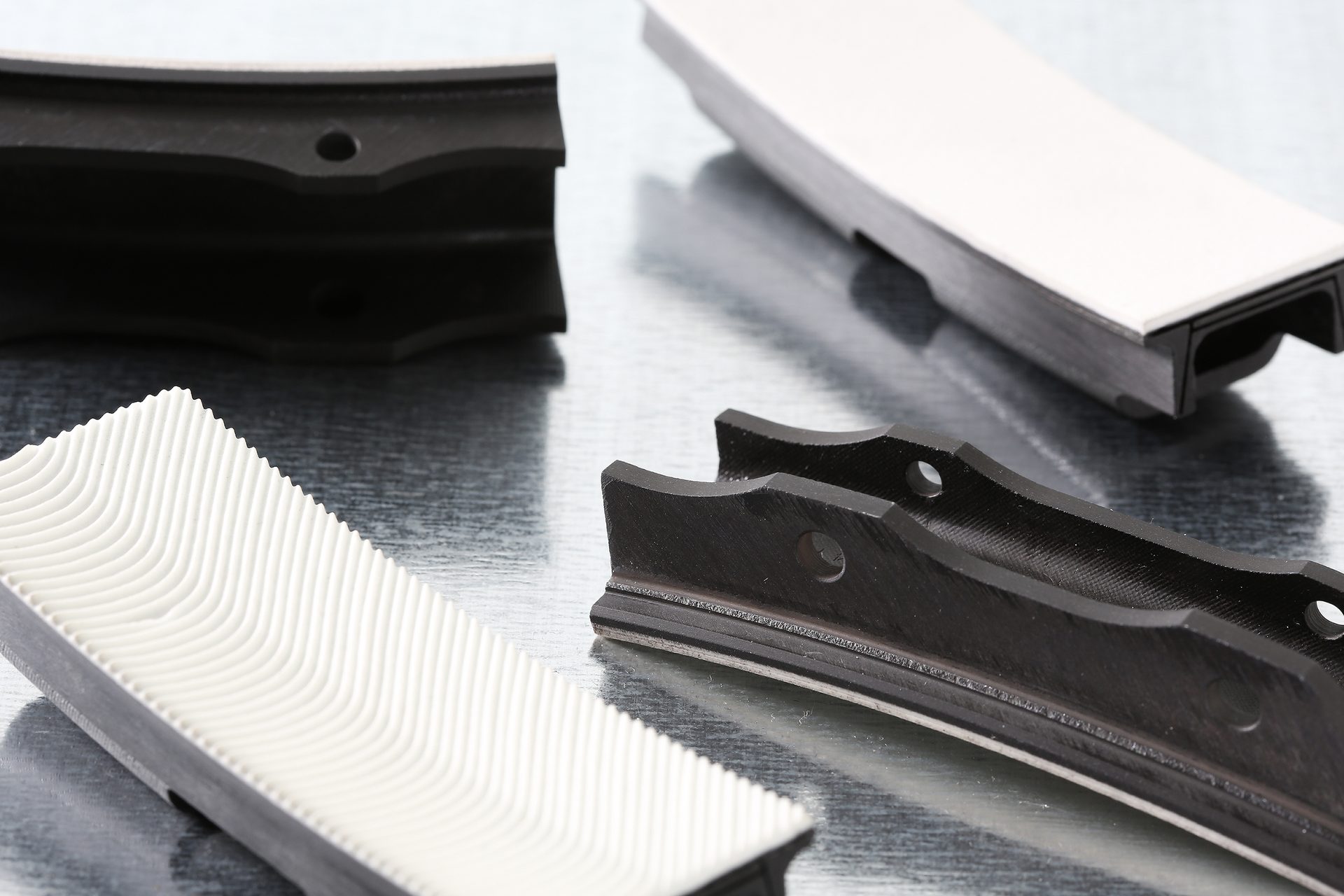
Components of the ceramic matrix composite turbine shroud in the LEAP engine. Credit: GE Aerospace
CMC development at GE: LEAPing into commercial deployment
Jon Blank, an engineer and manager at GE Aerospace who has worked with CMCs for years, explained the technology’s evolution at the jet engine maker.
“We know temperatures are always going to go up, and engine pressures are going to go up,” he says, describing the competitive drive to make more powerful yet efficient engines. “On the material side, we said we need the next-generation material.”
Nickel-based superalloys were running out of the capability to achieve higher operating temperatures, he says.
“We needed that next step. And that’s where ceramic matrix composites came in.”
GE researchers began developing the material and testing it on a small scale. Fast forward to today, and ceramics are not only flying but have been successfully put into the field in one of the best-selling engines for single-aisle aircraft in the world.
The LEAP engine features a CMC turbine shroud, i.e., the component which directs airflow into the hottest part of the engine. The component is much lighter than its metal counterpart and can withstand hotter temperatures, increasing the potential for greater thrust and better efficiency.
“If you need more thrust, more power, this allows you to get that,” Blank says. “It also is an environmental play, a sustainability play, because now you can change how you run the engine … you can change the amount of emissions that come off. It’s a real game changer from a materials standpoint in our end product.”
The LEAP engine has been embraced by the world’s airlines. At the Paris Air Show in June 2023, GE announced orders for 70 LEAP-1A engines and for 80 LEAP-1B engines to power Boeing and Airbus aircraft.
Following the success of LEAP, GE has incorporated CMCs into its GE9X engine. This engine, which GE says is the largest and most powerful aircraft engine ever built, is designed to power the next-generation Boeing 777X aircraft. In contrast to the single CMC component in LEAP engine, the GE9x features five CMC components: two combustor liners, two nozzles, and one shroud.
“And the level of complexity of those components has gone up significantly,” Blank says. They will help make that engine one-third the weight of conventional jet engine but twice as durable, and able to use 59% less cooling air.
In an engineering test in 2017 at GE’s outdoor test facility outside Cincinnati, Ohio, the GE9X achieved 134,300 pounds of thrust, a world record.
CMCs have also been incorporated into GE’s military engines, specifically its XA100 adaptive cycle engine, which has completed testing and is planned for the Air Force’s F-35 combat aircraft. Its engineering innovations, including the use of CMCs, have contributed to a 10% increase in thrust and a 25% improvement in fuel efficiency.
CMCs are also a key part of the engineering behind the RISE program that GE initiated with its joint venture partner Safran. RISE, which stands for Revolutionary Innovation for Sustainable Engines, aims to reduce fuel consumption and carbon dioxide emissions by more than 20% compared with today’s most efficient aircraft engines, a key to helping the aviation industry achieve a larger target: net-zero CO2 emissions by 2050.
“So, we see a very bright future for CMCs,” Blank says. “It’s why we’ve invested now close to $2 billion in it.”
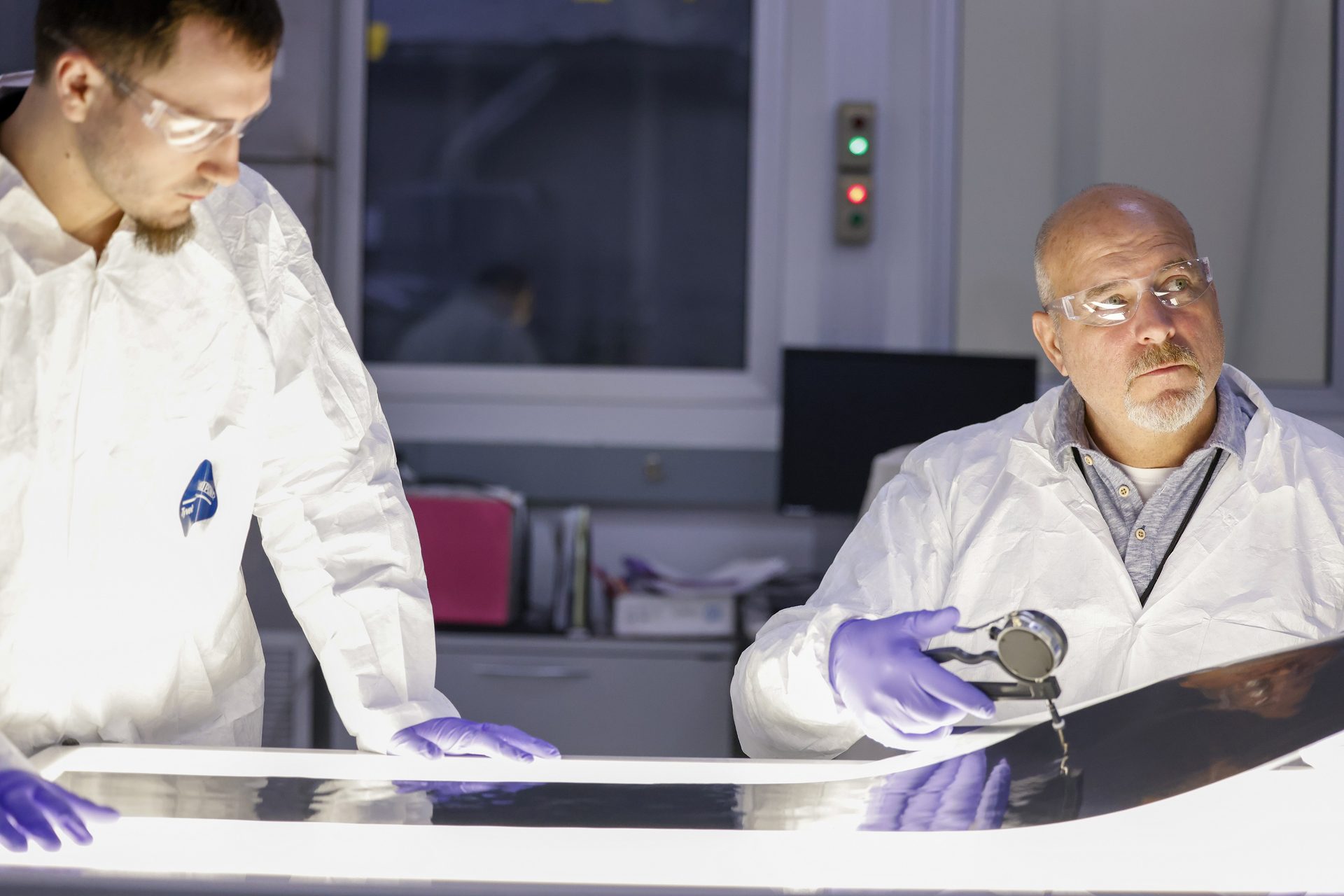
Researchers working with CMCs at GE’s complex in Evendale, Ohio. Credit: GE Aerospace
In addition to leading the charge to commercialize CMCs, GE’s research and investment led to its decade-long effort to establish an integrated CMC supply chain.
In 2017 in Huntsville, Ala., GE opened what it says is the first center to mass produce silicon carbide, the raw material used to manufacture CMCs. Two adjacent factories on 100 acres produce silicon carbide ceramic fiber, the material used to make the unidirectional CMC tape produced in the neighboring factory. The tape, which is used to fabricate CMC components, is then shipped to Asheville, N.C., where another plant condenses it, machines it, and then ships the final part to engine assembly shops in Durham, N.C., or Lafayette, Ind.
Control over the supply chain allows the company to focus on boosting production rates, refining manufacturing processes, and lowering costs, GE says.
CMC development throughout the aerospace industry
GE’s competitors in the aircraft engine space are also investing in CMC technology research and development.
In 2013, Rolls-Royce purchased Hyper-Therm High-Temperature Composites, a privately held company based in Huntington Beach, Calif. Then in 2016, it announced a $30 million expansion and new facility in southern California as its CMC technology hub.
“The development of lighter, stronger, composite fiber components is just part of our commitment to continuously improve the performance of our products by focusing on lowering fuel consumption, emissions, and noise,” former CEO Marion Blakey said at the time.
In 2021, Pratt & Whitney opened a CMC facility in Carlsbad, Calif. This 60,000-square-foot facility focuses on the engineering, development, and production of CMCs for aerospace applications.
“Some of our best and brightest minds are innovating within this facility and they will ensure that we continue to operate on the cutting edge of aviation technology for decades to come,” says Frank Preli, vice president of Propulsion and Materials Technology at Pratt & Whitney.
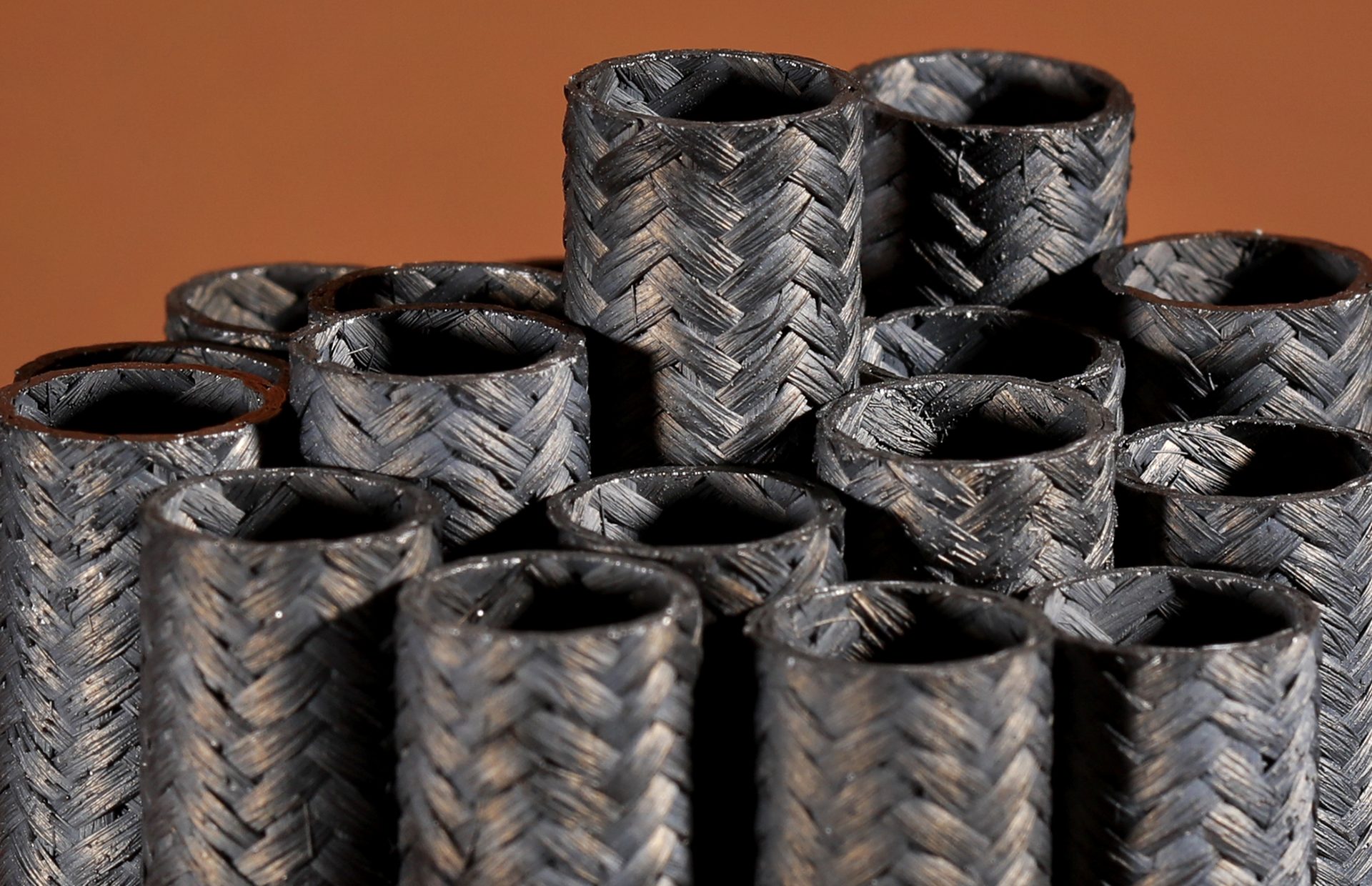
Tubes made of nuclear-grade continuous silicon carbide, fiber-reinforced, silicon carbide-matrix composite. These tubes will be used in the development of accident-tolerant fuel cladding for light-water reactors. Credit: ORNL
Next-generation CMCs: Establishing new applications and fabrication methods
The promise of lightweight durability in high-stress environments has scientists looking for new applications and new manufacturing methods for CMCs.
Oak Ridge National Laboratory researchers recently demonstrated the feasibility of additively manufacturing fiber-reinforced ceramic matrix composites, an advancement that will open new possibilities in the design space for these materials, says Edgar Lara-Curzio, a distinguished scientist at the national laboratory.
Researchers there are also initiating a project to test new techniques, including additive manufacturing, to fabricate furnace heating elements and components. The successful completion of that project could enable a leap in CMC capabilities by improving matrix densification, Lara-Curzio says. Another ORNL team is working to further develop CMCs for applications in nuclear energy.
Westinghouse, in partnership with San Diego-based General Atomics and the Department of Energy, has developed “accident-tolerant” nuclear fuel rods that use CMC cladding to replace the metal cladding that it typically used. The companies say the silicon carbide-based cladding allows the fuel rods to withstand temperatures of more than twice what can be sustained by metal cladding.
At GE, researchers are developing rotating engine parts using CMCs and have conducted engine tests using the material, Blank says.
Researchers at Boeing, the University of Southern California, and 3M are working on a project to ensure the affordability of CMC components for hypersonic platforms, and to use 3D vision-based sensors to reduce the cost and variability for high-rate production of CMC structures. The project recently received funding from the Advanced Robotics for Manufacturing Institute.
Clearly, the future for CMCs is attractive, as corporations, universities, and governments continue to invest in research and development for new applications. This collaborative atmosphere supports the recommendation that faculty in the Sustainable Manufacturing Systems Centre in the School of Aerospace, Transport, and Manufacturing at Cranfield University (U.K.) noted in a paper published in February 2023.
“Advanced ceramics have a tremendous amount of innovation potential, but to fully realize this potential along the entire value-added chain, significant efforts from both the academic and industrial sectors are needed,” they write.
They continue, “Despite already having a plethora of uses, CMCs have not yet reached their full potential. The obstacles in the medium and long term, particularly in aeronautics and aerospace applications, will be such that the use of custom materials will necessitate a significant R&D investment.”
That situation appears to be in the cards, as successes to date in critical applications of the material are leading to stepped-up investments and broader research.