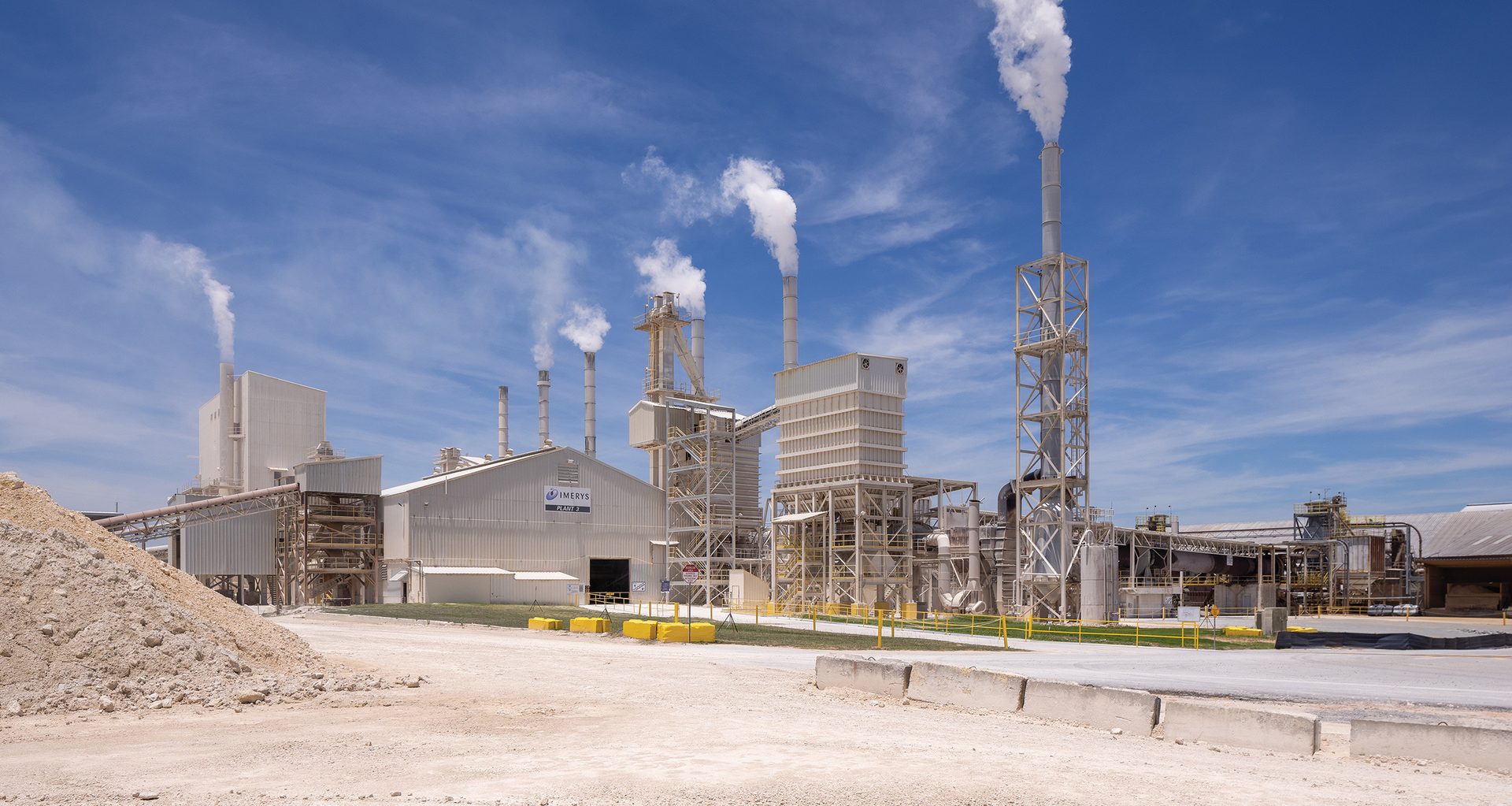
Imerys on its way to reduce CO2 emissions through biomass waste consumption in Georgia
By Nancy Bunt
Five years ago, multinational group Imerys S.A. (Paris, France) embarked on a journey at its Andersonville plant in Georgia to reduce greenhouse gas emissions.
Imerys Andersonville is the home of a superior sintered mullite product called Mulcoa®.1 This product, which is produced from unique high-purity refractory grade kaolin clay from the southeastern kaolin belt, is renowned in the world of refractory aluminosilicate calcines as the benchmark for refractory production.
The carbon footprint of Mulcoa, which has been in production for 54 years, is impacted by the combustion of fossil fuels during the manufacturing process. This plant consumes the most energy across all Imerys facilities.2
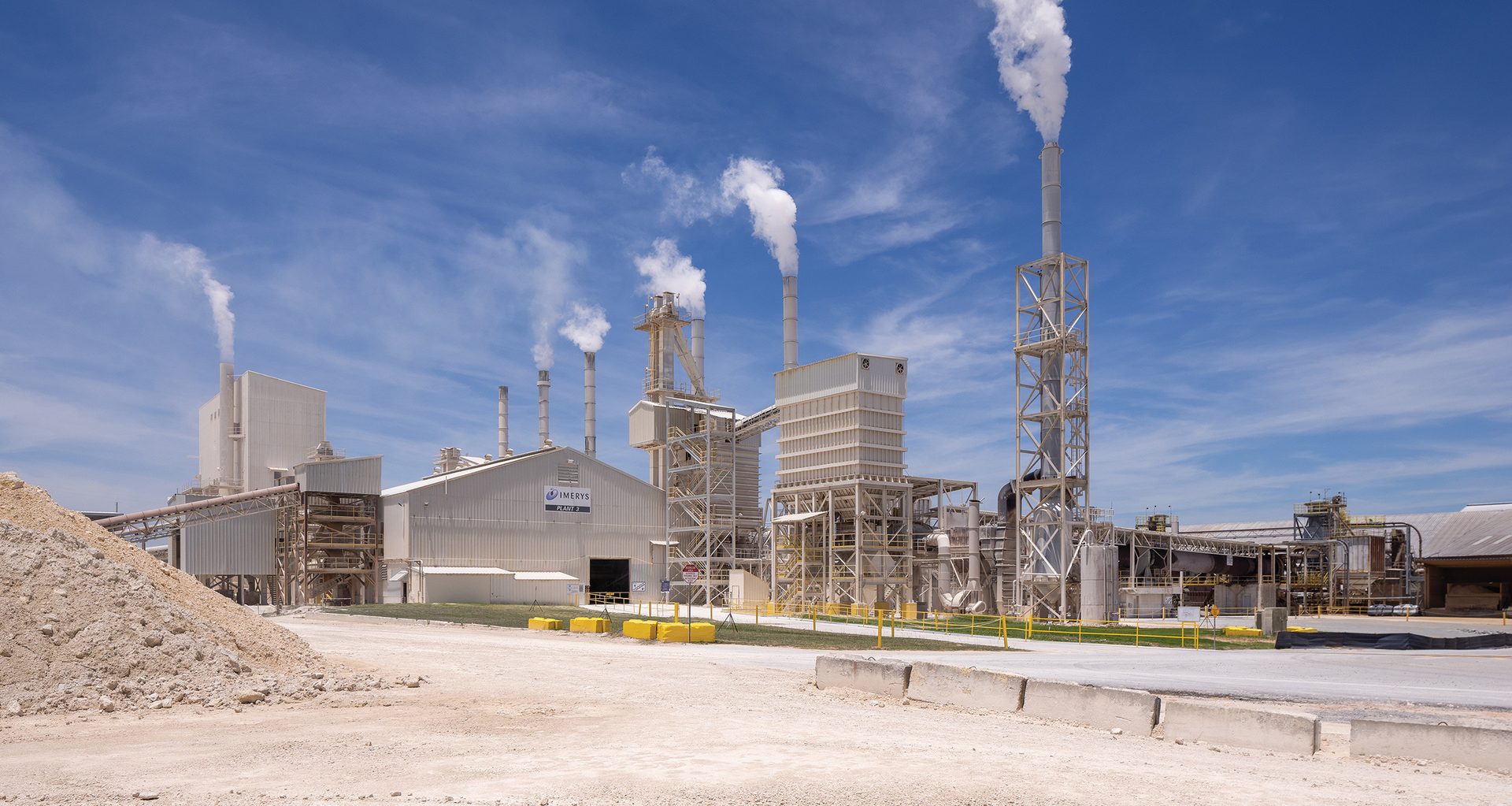
On June 11, 2024, Imerys held a ceremony inaugurating the carbon reduction project at its Mulcoa® production site in Andersonville, Ga.
Credit: Imerys
To address the plant’s environmental impact, Imerys Andersonville personnel initially aimed to reduce the plant’s greenhouse gas emissions by 103 Kt CO2 /year, which is equal to a 4% reduction in the Group’s emissions. To achieve this reduction, they planned to implement a solution successfully adopted at five other plants: transition from the use of fossil fuels to biomass waste and natural gas. Fortunately, the Andersonville plant is uniquely positioned to make use of a local biomass waste source: peanut shell hulls.
Andersonville is located in the largest peanut growing area in the United States. Peanuts were designated the state crop of Georgia in 1995, and today 53% of the peanuts grown in the United States are grown in southern Georgia.
To make use of ground peanut shell hulls as biomass waste, the US$20-million project entailed converting the existing kiln burners to accommodate ground peanut hulls (GPH) as well as installing the necessary infrastructure to handle and store a large quantity of GPH. The first phase of this project was completed in 2019, with first results being reported in 2020. As of 2023, 13% of the site’s total energy consumption came from GPH, which resulted in a 30-Kt reduction of CO2 emissions annually.
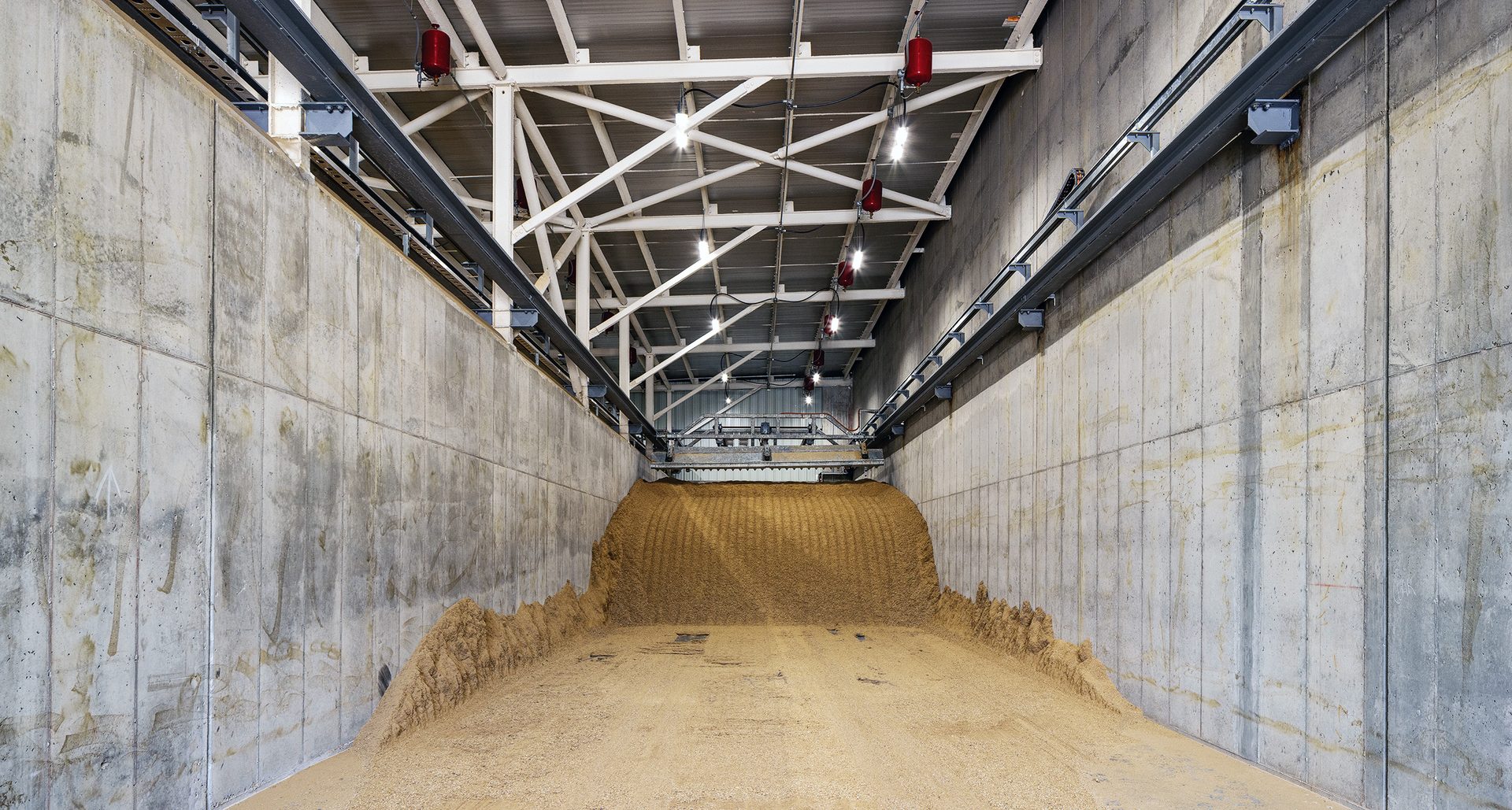
A loading bay for the ground peanut hulls at the Andersonville, Ga., site.
Credit: Imerys
As of mid-2024, the second phase of the project was completed. The plant now runs on a combustion source of roughly 20% natural gas and 80% ground peanut hulls, and it consumes close to 40 trucks per day of ground peanut shells. When the third and final phase of the project is completed by 2030, an overall reduction target of 140 Kt CO2 emissions per year will be achieved, compared to the emissions in 2018 when the project was conceived and designed.
The impact this fuel switching project will have on the individual product carbon footprint of Mulcoa products is significant, with up to a 50% reduction. Finalized life cycle assessments evaluating the new energy mix of natural gas and biomass waste will be available in 2025.
This project is just one example of Imery’s commitment and investment to align its activities to the 1.5°C trajectory under the Paris Agreement.3 The Group invests approximately US$16–21 million annually on projects and technologies to decarbonize its operations, all with the goal of reaching two set targets by 2030: reducing the Group’s scope 1 and scope 2 emissions by 42% and its scope 3 emissions by 25% from the base year of 2021. Through these activities and collaborations with suppliers across the value chain, Imerys is on the path to create more sustainable value for its customers.
About the author
Nancy Bunt is global sustainability director at Imerys Refractory Abrasives and Construction. Contact Bunt at nancy.bunt@imerys.com.