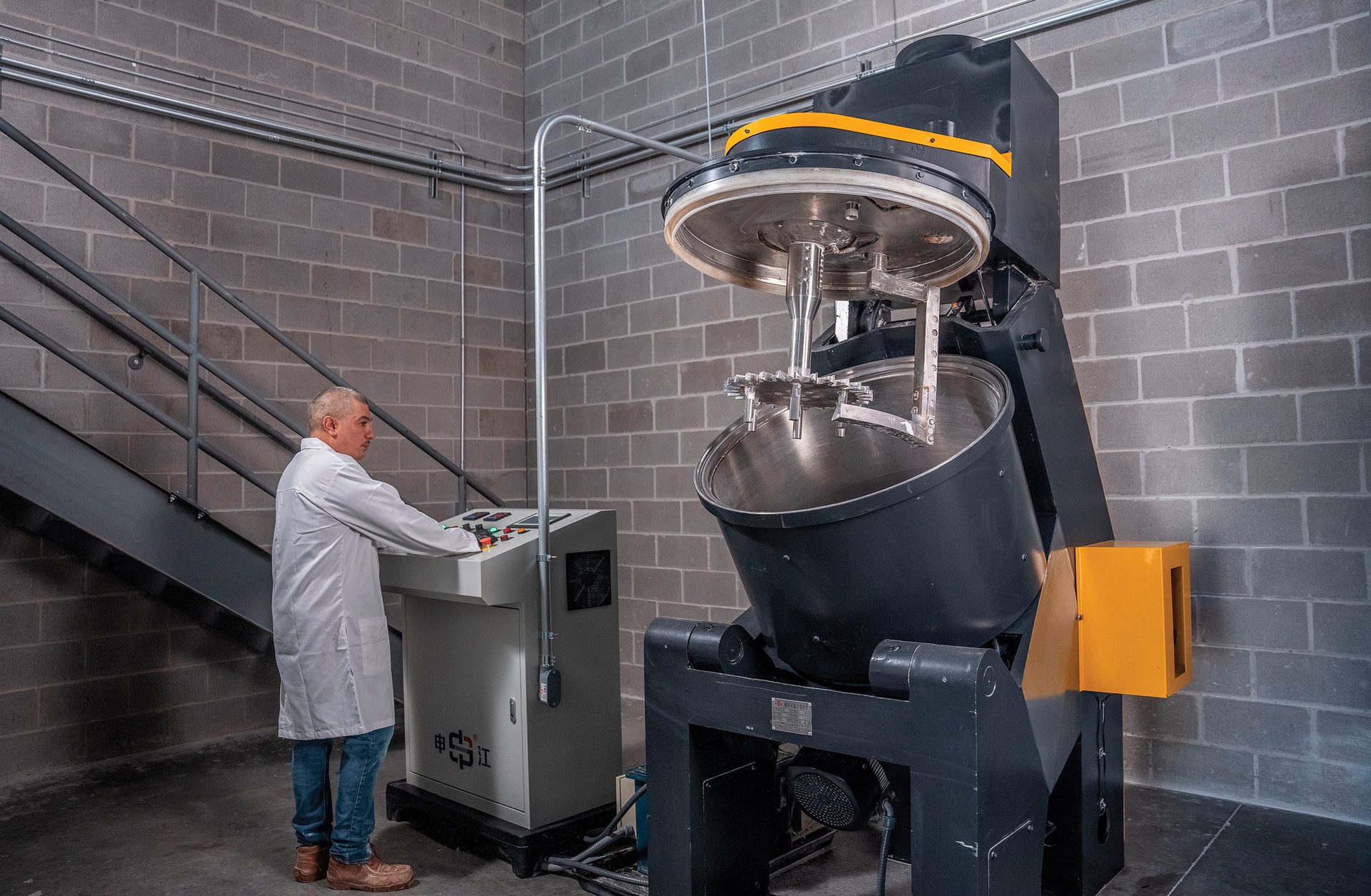
Investing in the future:
Practices for ensuring environmentally friendly and cost-effective manufacturing
By David Holthaus
There has never been a better time to put an environmental focus at the center of the manufacturing process, as addressing concerns around climate change and resource scarcity is increasingly critical for long-term business success.
Local and national governments around the world are implementing stricter regulations in part because their constituents are becoming more attuned to these issues. But there is also a clear economic benefit because environmentally friendly practices can lead to long-term cost savings through reduced energy use. Likewise, many manufacturers are under pressure from their partners and suppliers to meet targets for emissions and waste reduction. And adopting environmentally friendly processes can be a competitive advantage, as a reputation for environmental stewardship can attract environmentally conscious customers, build loyalty, and improve sales.
Every industry and every company has its own environmental challenges. In this article, we gathered the perspectives of three companies that collaborate with ceramics and glass industries to learn how they work to ensure current needs are being met without compromising the ability to meet future demand.
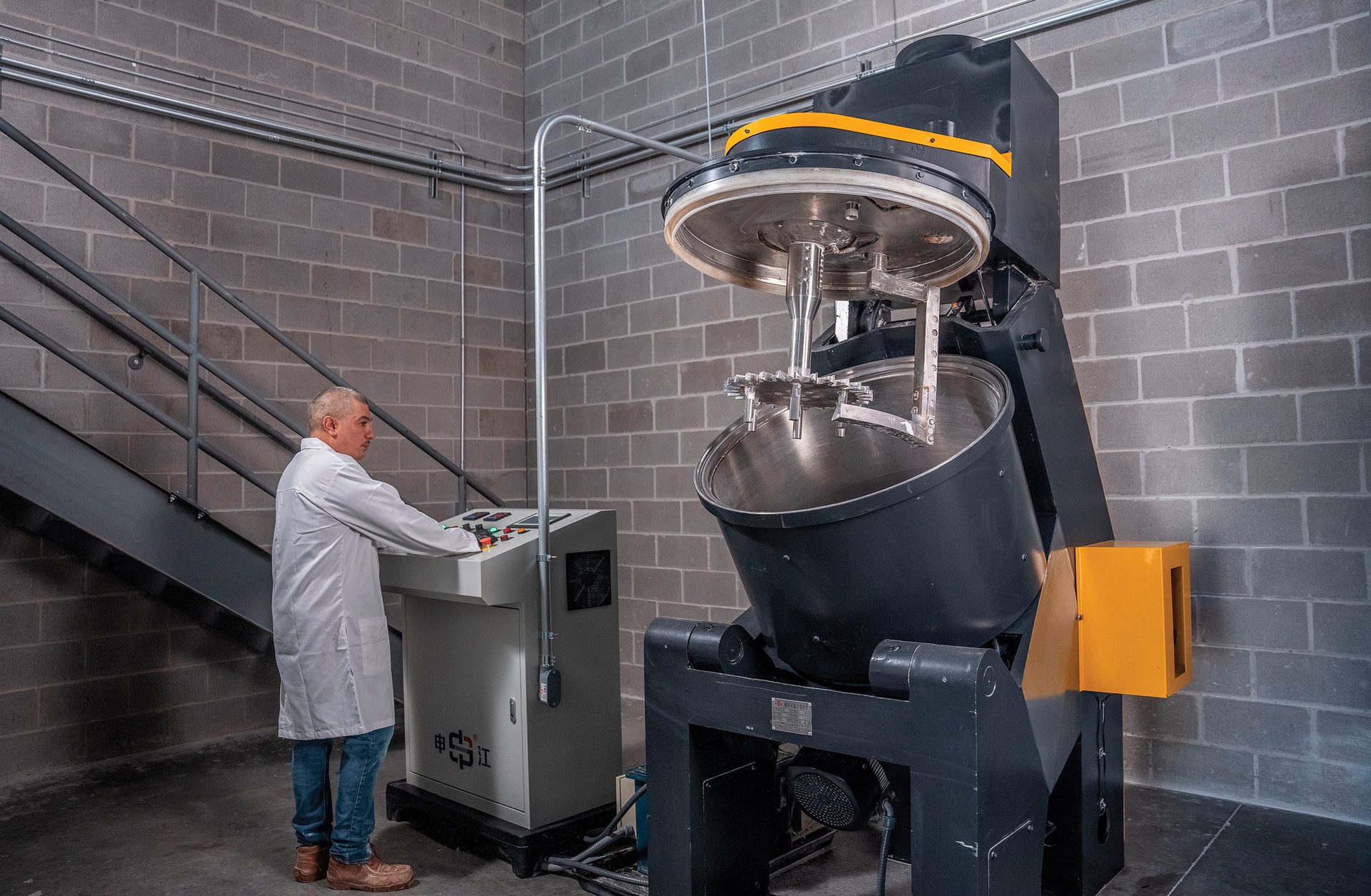
A high intensity mixer-granulator at the IntoCeramics lab.
Credit: IntoCeramics
IntoCeramics: Converting waste into usable products
Bryan Geary and Carl Sorrell founded On the Plant Floor (Houston, Texas), a manufacturing consultancy, in 2010. About five years ago, “We found the nature of our business changing,” Sorrell says. “We had large manufacturing companies coming to us and saying ‘I’ve got this waste stream. Is there something we can do about it?’” That led to the creation of the IntoCeramics division, which aims to convert waste materials into usable products. The work for that part of the business has remained steady ever since then.
Even before IntoCeramics, Sorrell had an interest in converting waste into usable products dating to the 1970s, when he worked for a brick manufacturer. Once a year, a mobile unit would be brought in to crush waste brick to be used as landscaping material.
“Lo and behold, we made more money on the landscaping material per pound than we did on the brick,” he says. “It just started something rolling in my mind, and I’ve been working in that arena ever since.”
These days, their work makes much more use of high-tech methods to analyze materials and to target potential uses for the waste stream. One successful project involved an aggregate company that produced 30,000 metric tons a year of waste from a washing operation. It cost $2.2 million a year in tipping fees to dispose of the material, and the company was running out of landfill space to dispose of it. They had even considered shipping the waste out of state for disposal, which would have been very costly. The company was interested in saving that money and finding some productive use for it.
IntoCeramics used X-ray diffraction and X-ray fluorescence technology to examine the material, analyzed its thermal performance and its forming characteristics, and discovered it was unsuitable for use in brick, tile, or other traditional ceramic materials. But the analysis did find that a lightweight aggregate could be made from it, with potential uses in road construction and other areas where lightweight concrete is used. The IntoCeramics team then went through a three-phase process, including a capital expenditure analysis and pilot manufacturing, to determine if the product was suitable for recycling.
The team at IntoCeramics is also working with a company called Vecor Technologies (Houston, Texas) on methods for processing a waste stream material as a substitute for titanium dioxide, a product used in paints, coatings, inks, ceramics, and plastics.
“In this case, you’re taking a material that is relatively low cost to begin with and using it to replace material that is extremely expensive,” Sorrell says.
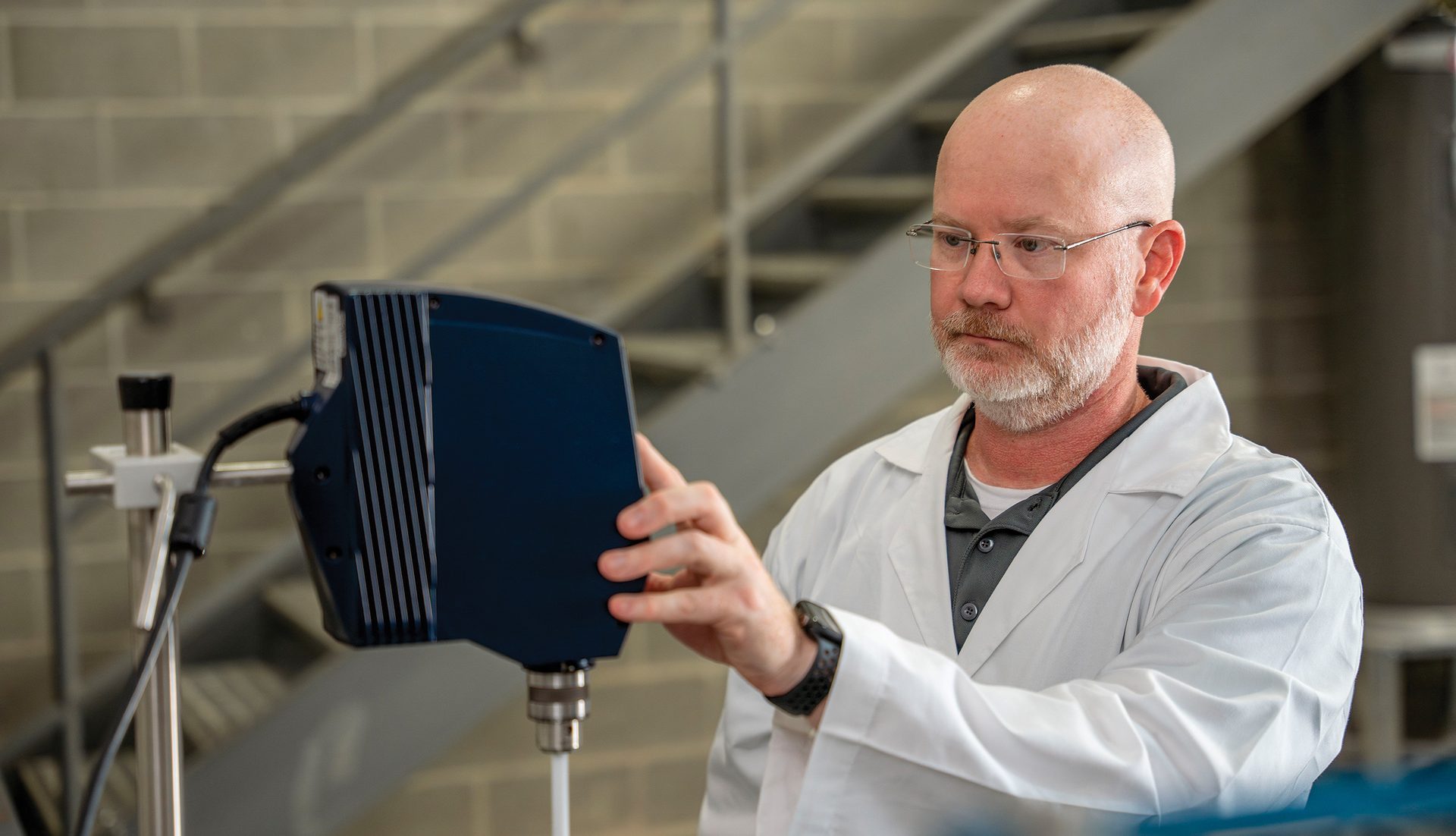
IntoCeramics uses high-tech methods to analyze materials and target potential uses for waste.
Credit: IntoCeramics
Conversely, analysis sometimes reveals that waste streams are not always feasible. A large mining company approached the team at IntoCeramics a few years ago to ask about turning mining waste into ceramic tile. Although it was possible to do, the company generated so much waste that it could not use it all and the capital expenditure involved in setting up such an operation would have been prohibitive.
Sorrell says that worldwide mineral waste generated annually is between 88 billion and 98 billion metric tons, while worldwide production of cement, ceramic tile, glass, sanitaryware, and refractories is only 10 billion metric tons.
“You’ve got to target the approach and define what your goal is,” he says. “If your goal is to recycle as much as possible, then you’ve got to target areas where lots of the material can be used.”
The growth of environmental regulations and awareness has helped drive the company’s business.
“Our business has expanded significantly,” Sorrell says. “Five years ago, we had one laboratory in Houston. We now have four, and we are looking to expand even further.”
Kyanite Mining: Going beyond the minimum
Kyanite is a mineral used in the manufacture of refractories, and in North America, it is produced by one company from two mines in central Virginia. Kyanite Mining Corp. (Dillwyn, Va.) is a family-owned and operated business that has been producing kyanite and its calcined derivative, mullite, since the 1940s. Its two quarries and four processing plants in Buckingham County, Va., supply most of the world’s kyanite.
A long list of federal laws and regulations covers all aspects of mining, and each state also has laws that companies must follow. At Kyanite Mining Corp., those voluminous regulations are just the beginning of its environmental stewardship.
“The bare minimum is not the goal for us,” says John Snoddy, Kyanite Mining’s environmental and safety director. “Our goal is to achieve more than the minimum threshold between compliance and noncompliance.”
That goal stems largely from the fact that many of the company’s 130 employees are either natives of central Virginia or of Buckingham County itself, Snoddy explains.
“When you’re operating in the county that’s home, you treat it like home,” he says.
It is also just good business. The company works to use or sell as much of the material that it extracts as possible, including the mining byproducts of sand, pyrite, and magnetite. That minimizes waste and follows sound resource recovery practices. It also works to contain pollution and restore the land to its natural state after mining, ensuring that the company can operate effectively for years to come.
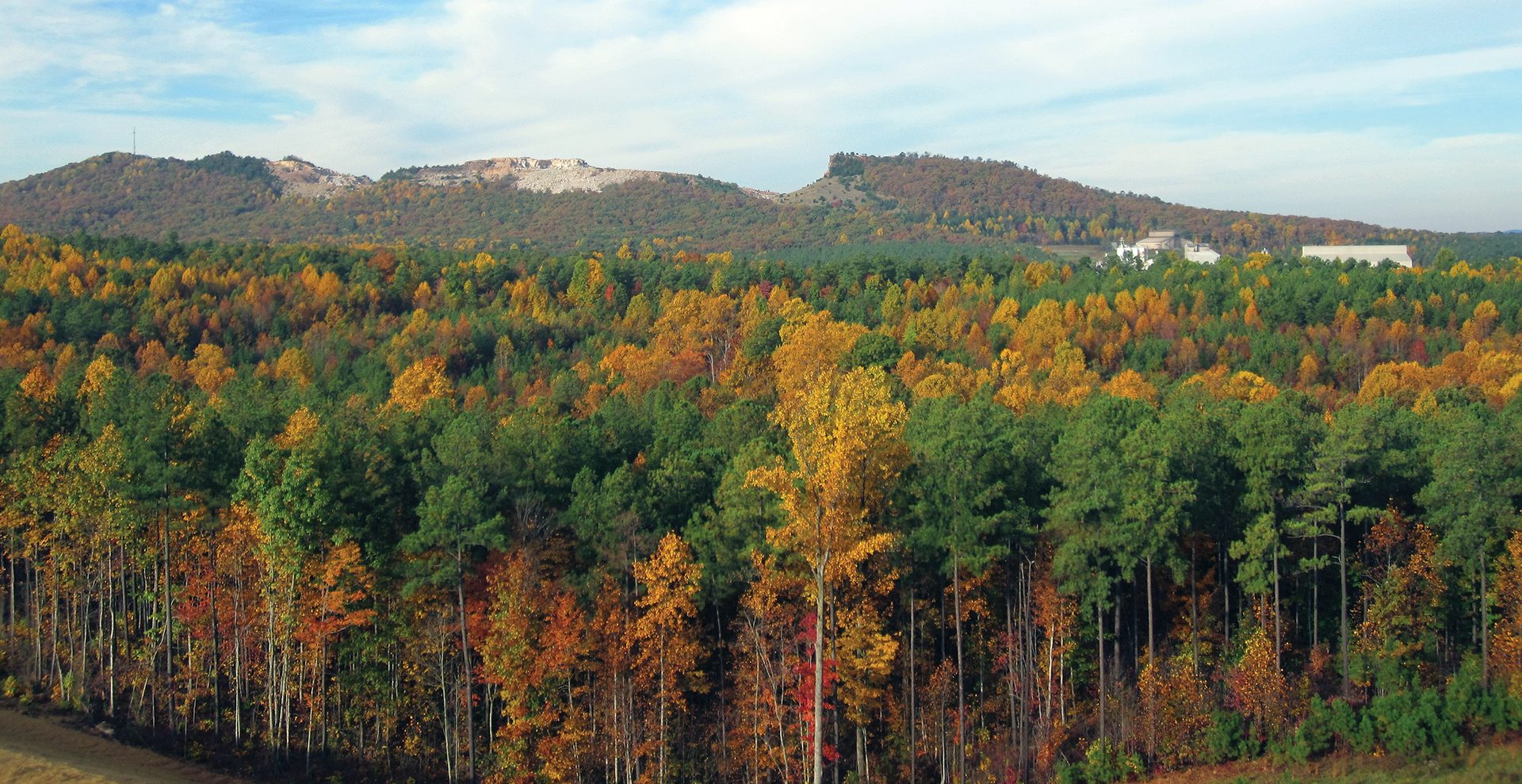
Kyanite Mining Corp.’s Virginia quarry is the main source of the mineral kyanite in North America.
Credit: Kyanite Mining Corp.
Producing 150,000 tons of highly purified kyanite a year requires drilling, blasting, and moving massive amounts of earth to extract dirt, rock, and the minerals they contain. All that exposes whatever lies beneath the surface to the elements and can lead to runoff. Building sediment ponds, sediment traps, diversion berms, and rock filter berms ensures that the sediment stays on site.
“Our goal is to capture all of that sediment so that despite the fact we have to disturb the earth to operate, the sediment that is exposed to stormwater doesn’t migrate off our site,” Snoddy says. “That’s arguably the most important environmental requirement that mining companies have. Allowing your sediment to migrate offsite is a recipe for having your neighbors upset at you.”
Kyanite Mining has won several state and national environmental stewardship awards, the most notable of which is for the work completed at its original mine site at Baker Mountain. The site, in Virginia’s Prince Edward County, was operated as a mine from the 1920s into the 1970s, and a processing plant attached to the quarry continued to operate into the early 2000s. In 2006, the company began a large reclamation project, removing the industrial structures and turned the plant’s footprint and surrounding acreage into wildlife habitat.
“You’d be hard pressed to believe that there was once a processing plant on the site,” Snoddy says. “It’s now grassland and forest land with all of the native wildlife you would expect to see here in central Virginia.”
Lucideon: Researching and testing advances in sustainable manufacturing
The British Ceramic Research Association was created in 1948 to serve the ceramic industry with research and then later with testing and certification services. As the association grew and evolved, its name changed to CERAM Research Ltd. Following the acquisition of a testing and analysis company in the United States, the organization eventually rebranded in 2014 under the name Lucideon.
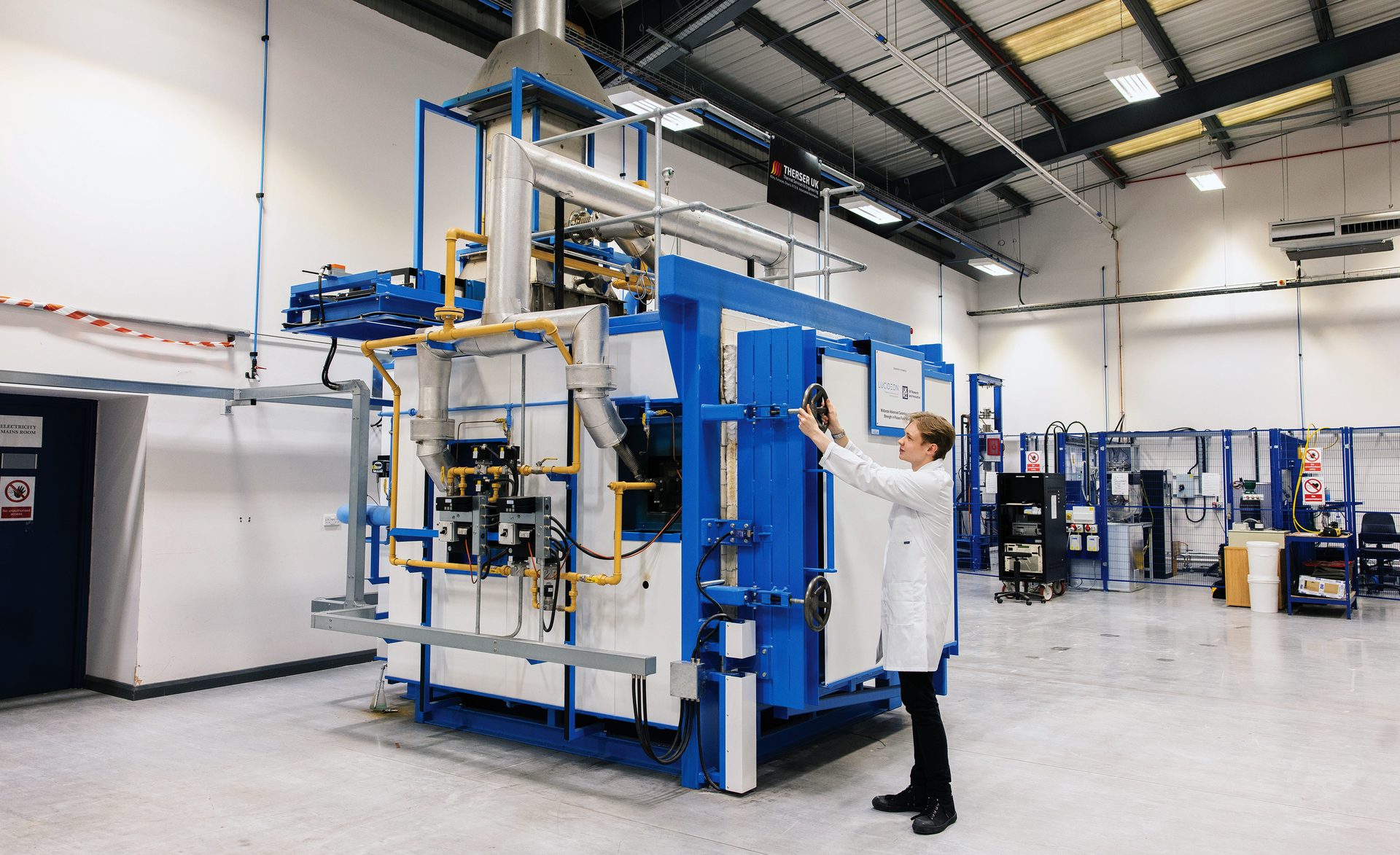
Lucideon’s kiln for research and development incorporating hydrogen fuel.
Credit: Lucideon
Through its expansions, Lucideon (Stoke-on-Trent, U.K.) has continued servicing the ceramic industry and has branched into aerospace, construction, energy, and health care, as well as other industries. Its team of experts in seven locations in the United Kingdom, the United States, and Japan assist companies with difficult materials challenges.
“If it’s made out of stuff, we’re probably going to be an expert in it,” says Richard Goodhead, Lucideon’s chief marketing officer.
For the ceramic and glass industries, Lucideon is consulting on a range of projects to reduce energy use and assist with decarbonization efforts. For more than two years, Lucideon researchers have explored the potential of hydrogen as a clean fuel for kilns. Hydrogen produces only water vapor as a byproduct of being combusted, but using the fuel comes with its own challenges, including how the finished products are affected. Lucideon owns two state-of-the-art kilns used for research into the potential of hydrogen fuel.
The pilot scale facility allows clients to explore using various blends of hydrogen and natural gas in their firing at an offsite location.
“If there are R&D challenges that an organization wants to try and undertake, the one thing they can’t afford to do is to shut down their production line to carry out those experiments,” Goodhead says. “So this is an off-plant, pilot-scale facility where they can do that kind of experimentation.”
Lucideon also has the capability to demonstrate and develop flash sintering technology, an advanced method that can reduce processing time and furnace temperatures, with the potential to have a big impact on energy use.
“What flash sintering seeks to do is to sinter at a lower ambient temperature and apply electrical fields to produce a localized and controllable input of energy into the body to cause the sintering process to still occur,” Goodhead says.
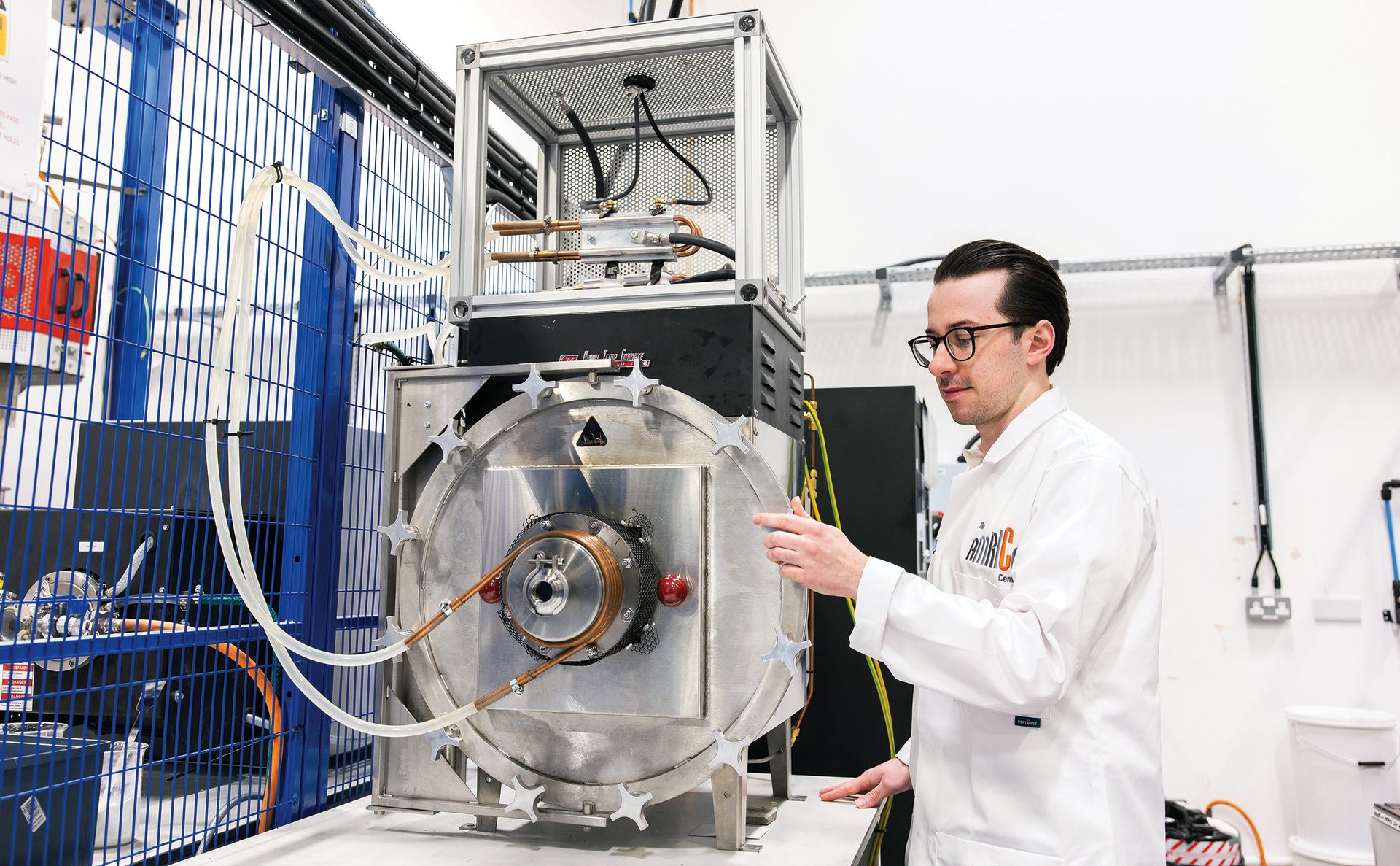
Lucideon is developing and demonstrating flash sintering technology.
Credit: Lucideon
In a case study, Lucideon experts worked with a fuel cell manufacturer to test flash sintering technology for ceramic electrodes, with results showing a decrease in energy use, increased productivity, and lower cost.
Lucideon researchers also developed a solution to the global challenge of disposing of nuclear wastes. The traditional method is to capture it in cement, a process that is energy intensive and leaves a carbon footprint. Lucideon and a partner use a geopolymer technology based on a chemical reaction at low temperatures, reducing energy usage and carbon emissions.
“We’ve also found through experimentation that we can encapsulate more waste per unit volume in a geopolymer formulation than you can in traditional concrete, so you can therefore take up less space,” Goodhead says.
The lower-cost, lower-carbon technique has been successful in completely encapsulating problematic waste streams, withstanding radiation, and other stresses.
“We’re quite optimistic that this could be a real game changer for nuclear waste,” Goodhead says.
Lucideon is also a member of the Foundation Industries Sustainability Consortium, a group of research leaders in the foundation industries of cement, metal, glass, ceramic, paper, polymer and chemicals, all of which require a lot of energy to produce the foundational products that they do. The group plans to work on a process optimization project for the ceramic industry, experimenting with better furnaces and heat management to improve efficiency and reduce energy use.