Sequestering carbon in clay products:
An approach to net-zero
and net-negative ceramics
By Brian P. Gorman, Jim Welte, David Nowacek, and Alexis Sitchler
bulletin | application note
Credit: Brian Gorman
To keep global temperature from rising more than 1.5°C, we must reduce carbon dioxide emissions by 50 Gtons per year while also removing an additional 10 Gtons per year from the atmosphere by 2050.1
Several methods exist to remove CO2 already present in the atmosphere, but none alone presently can achieve the goal of sequestering 10 Gtons per year. As such, stakeholders in every industry must do their part in lowering CO2 emissions and enabling sequestration.
This article explores a novel approach the ceramics community can take to help achieve these goals: sequester carbon in clay products.
Mineralizing carbon: A primer
Mineralization can be defined as a chemical reaction in which gases react with solids and/or liquids to produce other nonreactive solids. In the context of mineralizing CO2, reactions with mafic rocks, such as olivine-rich basalt, to produce carbonate solids is a natural process that geochemists are exploring as a way to sequester CO2 on a Gton per year scale.2,3
This natural process starts when gaseous CO2 reacts with liquid water to produce carbonic acid. This acidic solution reacts with silicate minerals in mafic rocks to release the rock’s alkaline and alkaline earth cations, namely calcium, magnesium, and iron, into the solution. These cations subsequently react with the inorganic carbon species and precipitate solid carbonate minerals such as calcite (CaCO3), dolomite (Ca,Mg(CO3)2), and siderite (FeCO3).
Throughout the reaction process, mineral dissolution and precipitation reaction rates are heavily dependent upon surface area contact between the solution and solid reactants. Though geologic sources of mafic rocks have some surface exposure, it is nowhere near enough to contribute substantially to the goal of sequestering 10 Gtons per year. Scientists would need to either increase exposure to mafic rocks at Earth’s surface through mining or capture and pump the CO2 underground.
Rather than relying on natural deposits of mafic rock to sequester CO2, engineering clay products to elicit mineralization reactions may be a more feasible and reliable approach to achieve significant emissions reductions.
ADVERTISEMENT
Mineralization via clay products
Clay products, such as architectural bricks, pavers, and roof tiles, are a promising high-surface-area solution for carbon mineralization. Approximately 4 billion bricks are manufactured in the U.S. every year. Globally, that number increases to more than 1 trillion bricks per year.
Unfortunately, fired clay products are traditionally felsic, meaning they are rich in aluminosilicates but low in the alkaline and alkaline earth cations of calcium and magnesium. As a result, they do not lead to significant precipitation of carbonate minerals after contact with carbonic acid.
We hypothesized that adding materials rich in mafic minerals to clay products would improve the product’s CO2 uptake by increasing the amount of alkaline and alkaline earth cations, which are necessary ingredients for the mineralization reaction. However, for this sequestration method to be a commercially viable solution, the mineral addition cannot significantly affect the clay product’s mechanical properties and appearance.
Industrial trials
We tested the feasibility of this sequestration method by adding 25 wt.% commercially available 70 mesh magnesium-rich olivine to an industrial clay extrusion process for pavers and modular bricks at Summit Brick Co. in Lakewood, Colo. Olivine melts at 1,890°C, so it can be directly incorporated into most clay product manufacturing.
We found that the olivine addition did not affect the manufacturing process. In fact, the olivine aided the drying process as little to no defects were observed in either the dry or green states.
In addition, because the olivine does not absorb water or undergo vitrification during firing, the bricks and pavers containing olivine had slightly less shrinkage. A small color change was observed in some products due to the precipitation of hematite from the natural iron content of olivine during sintering.
X-ray diffraction after sintering showed the presence of olivine remaining in the final product, along with the expected quartz and hematite. Microstructural analyses with scanning electron microscopy (Figure 1a) illustrated the olivine is well dispersed with abundant pore–olivine interfaces. Elemental spectral imaging with energy dispersive X-ray spectroscopy (Figure 1b) showed magnesium remained in the olivine grains and did not diffuse into the felsic matrix phases. Regarding mechanical properties, all bricks and pavers exceeded ASTM standards for compressive strength, water absorption, and freeze-thaw.
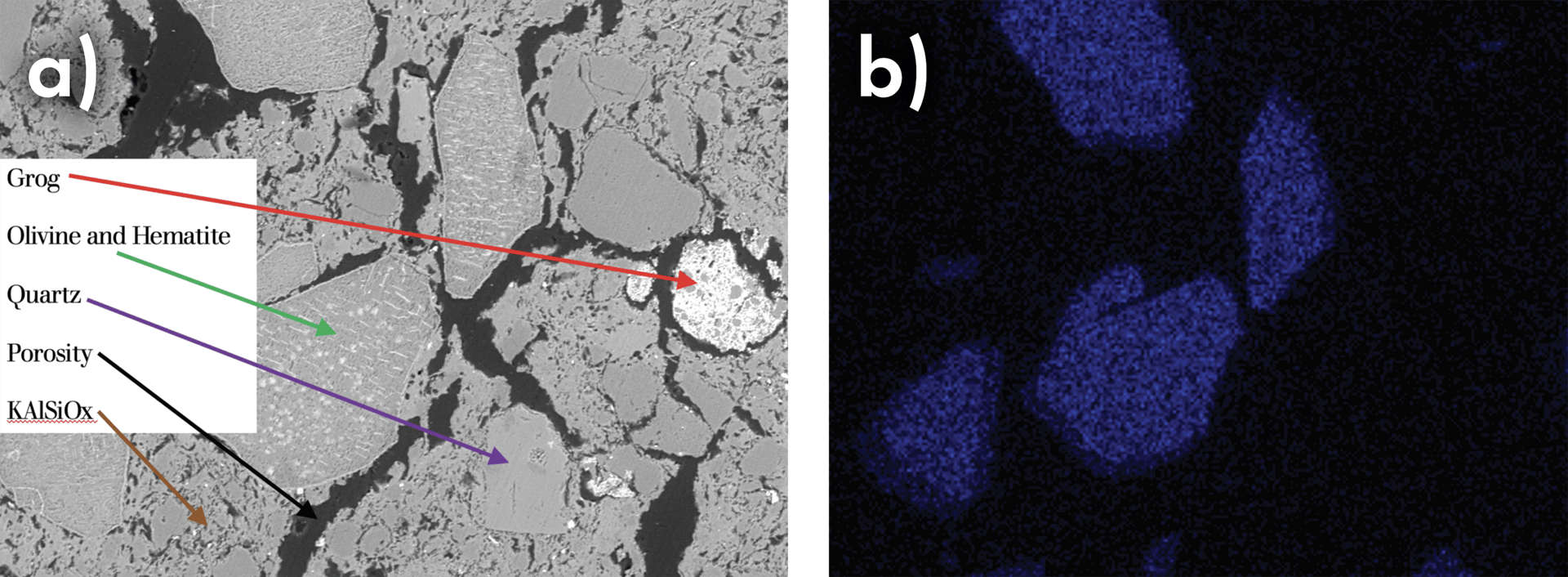
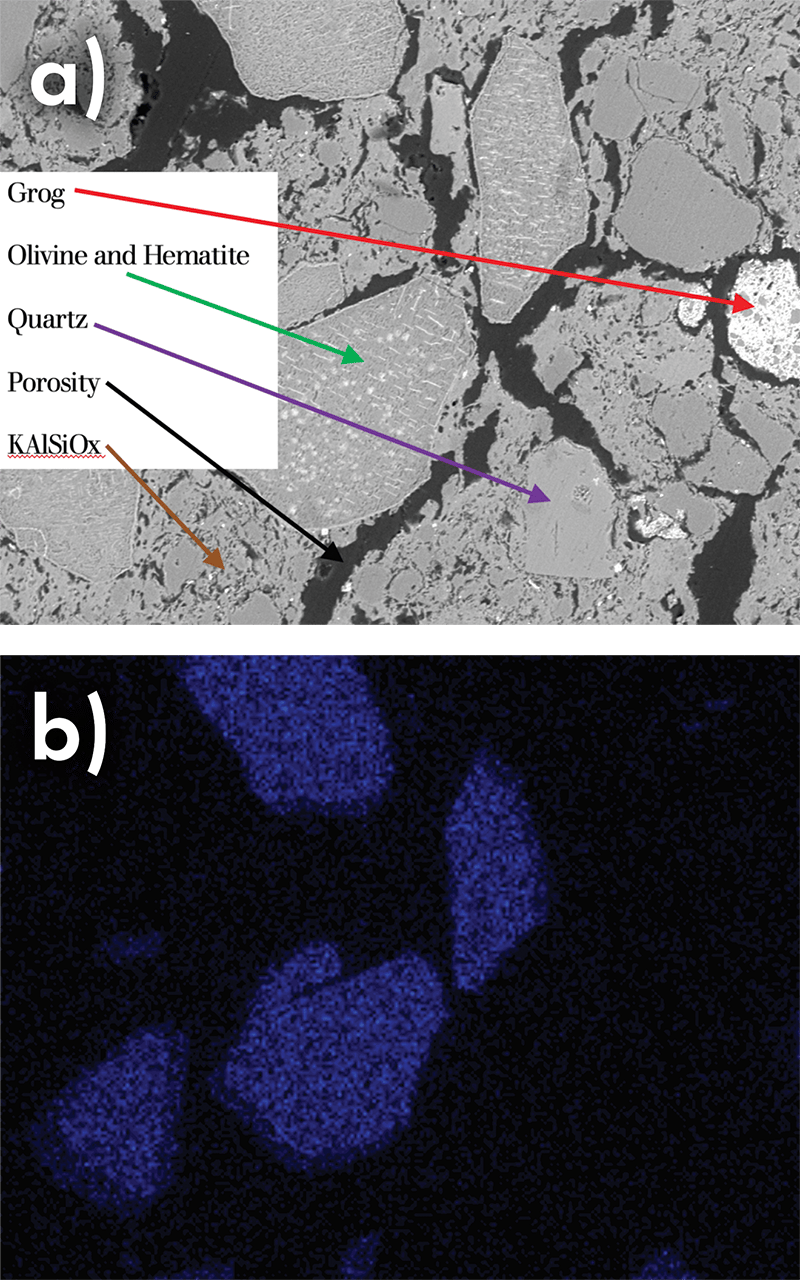
Figure 1.
a) Backscattered scanning electron micrograph of the clay brick sintered microstructure.
b) Energy dispersive X-ray microanalysis spectral image of the same area illustrating the location of magnesium. Magnesium is retained within the olivine grains, which are well dispersed within the microstructure. Abundant pore–olivine interfaces are also observed. Horizontal field width = 600 mm.
Credit: Brian Gorman
Generally, a 2-kg modular clay brick has about 550 grams of embodied carbon.5 As such, incorporating 31 wt.% olivine into the clay products is necessary to achieve net zero. Based on our tests, at least 40 wt.% olivine should be possible while still meeting ASTM standards. In other words, these materials have the potential to be net-negative because they sequester more CO2 than is produced during manufacturing.
Considerations of producing net-zero and net-negative clay products
Though the results of the first industrial tests are promising, several considerations must be addressed to enable global scale-up of the process.
First, olivine is not the only reactive mafic material compatible with ceramic manufacturing. Steel slag, metallurgical casting sand, basalt, and fly ash are all potential candidates, and they are all widely available as waste products. Engineered fiberglass may also have potential as an enhanced mineralization material.
Second, several micro- and macrostructural features influence how quickly the clay product sequesters carbon. On the micro level, particle size, volume fraction of porosity, and pore location relative to the mafic particles are all critical to the reaction rates. On the macro level, the installation method (horizontal pavers versus vertical bricks versus roof tiles) affects water exposure. Environmental factors such as humidity, rainfall, and temperature also play a role in sequestration rates.
Initial tests on pavers installed as a driveway in Colorado did not display any degradation in mechanical properties over the course of a year, but micro-Fourier-transform infrared spectroscopy indicated the formation of carbonates within the pores.
Besides material and form factor considerations, the embodied carbon of clay products can be further reduced by using less carbon-intensive production and distribution methods, such as firing in electric kilns and lower carbon transportation.
Summary and outlook
Clay product industries can easily and immediately incorporate mafic materials into their products. Once this solution is implemented, the ceramics community will be well positioned to make a large contribution in the global push toward net-zero and net-negative materials.
About the authors
Brian P. Gorman is professor of metallurgical and materials engineering at Colorado School of Mines and president of Net Negative, LLC (Golden, Colo.). Jim Welte is operations manager at Summit Brick Co. (Lakewood, Colo.). David Nowacek is president of Ironstone Strong, Ltd. (San Antonio, Texas) and vice president of Net Negative, LLC. Alexis Sitchler is professor of geology and geological engineering at Colorado School of Mines. Contact Gorman at bgormangolden@gmail.com. A patent for the described process is pending.