Es
By N
bulletin | feature
Glass waste solutions: Current trends, emerging markets, and new technologies
By Collin Wilkinson, Arron Potter, and Gabrielle Gaustad
bulletin | cover story
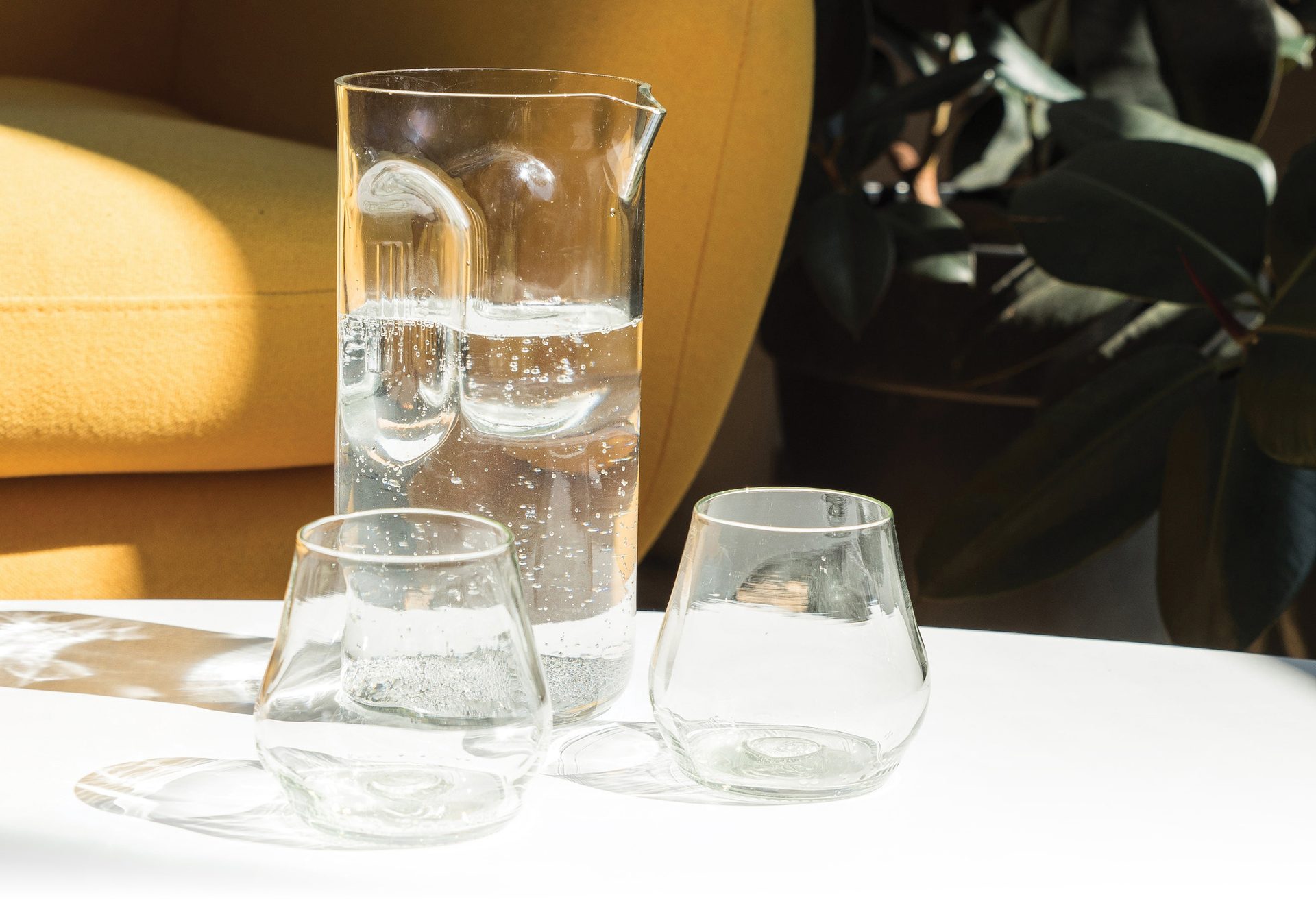
Glass waste solutions: Current trends, emerging markets, and new technologies
By Collin Wilkinson, Arron Potter, and Gabrielle Gaustad
Glass punch set produced by Remark Glass (Philadelphia, Pa.) based on recycled liquor bottles.
Credit: Rebecca Davis, Remark Glass
Glass recycling is, in principle, the perfect closed-loop process. The material can be continuously and completely recycled in theory, so only a small amount of raw materials would be needed to account for the systematic loss of material during processing of new products, such as production of fine powders during crushing.
In practice, though, glass recycling is often hampered by diverse factors, including low collection rates, increased comingling and contamination of recycled goods, and shifting economics such as labor and fuel costs. While the European Union has done a commendable job addressing these challenges, achieving an average 76% recycling rate for glass containers in 2018,1 the United States has struggled, reporting an average recycling rate of just 31.3% for the same year.2
In this article, we will examine the factors that prevent U.S. companies and communities from adopting a more robust recycling ecosystem. We will then discuss a model of the glass recycling system in New York state to better understand the flow of waste glass and identify some solutions that can help address the current recycling challenges.
Challenges to recycling
Many factors contribute to the lack of glass recycling in the United States, but almost all trace their origins to economics: Recycling must be profitable for companies to invest in its setup and maintenance. Unfortunately, the way that glass is typically collected in the U.S. prevents profitable glass recycling from the very start.
In general, glass recycling systems send post-consumer glass products, such as bottles and jars, to material recovery facilities (MRFs). These facilities either sort and clean waste glass themselves or pass it to a secondary processor, if financially worthwhile. Ideally, after sorting and cleaning, the glass is returned to a furnace and turned into new containers or fiberglass.3
The use of waste glass (cullet) reduces the need for raw materials in glass production. As a result, the carbon dioxide emissions that come from converting carbonate precursors to oxide glass are mitigated, thereby decreasing the embodied energy and carbon profile of the new glass products.4
In contrast to many European Union countries, most waste collection systems in the U.S. are based on single-stream recycling, meaning consumers mix all their recyclables together in one bin. Such a system reduces transportation costs and increases collection rates, but it places a burden on MRFs to sort all these recyclables.
Compositionally, most consumer glasses vary little. However, to MRFs, even small amounts of impurity or contaminants within and alongside these glasses makes a big difference. The most valuable glass is clear, colorless, free of organics (e.g., glue or paper), and free of fine particulates.5 Colorless clarity indicates the glass has minimal transition metal content, i.e., the substances used to give glass its color, and so allows for improved control over the chemistry of new melts. Additionally, glass with low organic and fine particulate content experiences reduced bubble formation during reprocessing. Unfortunately, by its nature, single-stream recycling results in post-consumer glass mixed with organics and tricolor (clear, green, and brown) glass waste with a wide range of particle sizes, making the job of the MRF more complicated.
Any tricolor stream could theoretically be transformed into pure single-stream feed stock for new glass melts, but the work, capital, and time required varies greatly based on the waste stream. Even the highest quality streams often require significant startup capital for sorting and automation due to challenges inherent to glass itself. Unlike other material streams, such as plastics, metals, and paper products, glass cannot be compacted and baled for ease of transport. It also breaks into small pieces that end up in other material streams and cause issues with MRF handling equipment. As a result, many recycling facilities will only invest if they are sure of an end market and a steady stream to process.
Some waste streams are so contaminated with metals or organics that it is unlikely the comingled glass will ever make its way into high-quality products. Instead, it is more cost effective to send this glass to landfills or use it as “landfill cover,” an acceptable end-of-life stream in many states, including Connecticut, Maine, Massachusetts, New Hampshire, New Jersey, New York, Pennsylvania, and Rhode Island.6,7
In addition to post-consumer glass waste streams, the construction and demolition industries generate waste glass from flat glass used in buildings. The production of flat glass requires materials of even higher quality than that of fiberglass or bottle glass, reducing manufacturers’ flexibility with input materials. Some flat glass manufacturers have programs to use recycled materials.8 But this process is difficult and slow growing, leaving post-industrial glass a critical, largely unaddressed problem with no clear solution.
Besides post-consumer and flat glasses, which largely conform to a narrow range of chemical compositions, specialty glasses with diverse compositions have the potential to form a large waste stream in the future. Specialty glasses can be found in applications such as kitchen and labware, electronic displays, wind turbine blades, photovoltaic modules, and emerging glass-based battery technology.5,9 As the U.S. pushes to decarbonize, the use of these specialty glass technologies is sure to expand quickly, requiring new recycling streams to handle this waste. The sidebar “Photovoltaic glasses and challenges to end-of-life disposal” provides a deeper look at one of these emerging specialty glass markets.
Modeling glass recycling in New York state
To identify solutions that can help address the current recycling challenges, Alfred University recently partnered with the New York State Department of Environmental Conservation (NYSDEC) to model the flow of waste glass in New York state.
New York is one of 10 bottle bill states, meaning there is a deposit on each glass container sold for beer and soda. Consumers can reclaim the deposit by returning the containers, thus improving return rates and ensuring a cleaner waste stream. New York also contains several glass manufacturers within state borders, meaning its intrastate recycling infrastructure positions it as a microcosm of the United States at large. These factors, in addition to New York’s current glass recycling rate of 50%, make the state an excellent proving ground for new innovations.
To understand the flow of waste glass in New York state, we developed a simple source/sink model in which consumers are treated as the “source” of glass waste.10 To account for geospatial variation, we assume that post-consumer glass waste is generated proportional to the population, which is determined based on zip code. Meanwhile, the two “sinks” in the model indicate where the glass ends up: at an MRF or the landfill. In the former case, the value of creating new glass products must be higher than the processing and transportation costs to make the process profitable. Notably, the model uses an estimated 70% glass recovery rate from MRFs, though the real recovery rate may be lower. In the latter case, the glass only needs to be moved once, which is economically advantageous. But it requires a tipping fee to be deposited in the landfill, which cannot be economically recovered.
Performing this analysis of the lowest cost option for each zip code resulted in a map that shows where and why recycling is economically favorable (Figure 1).
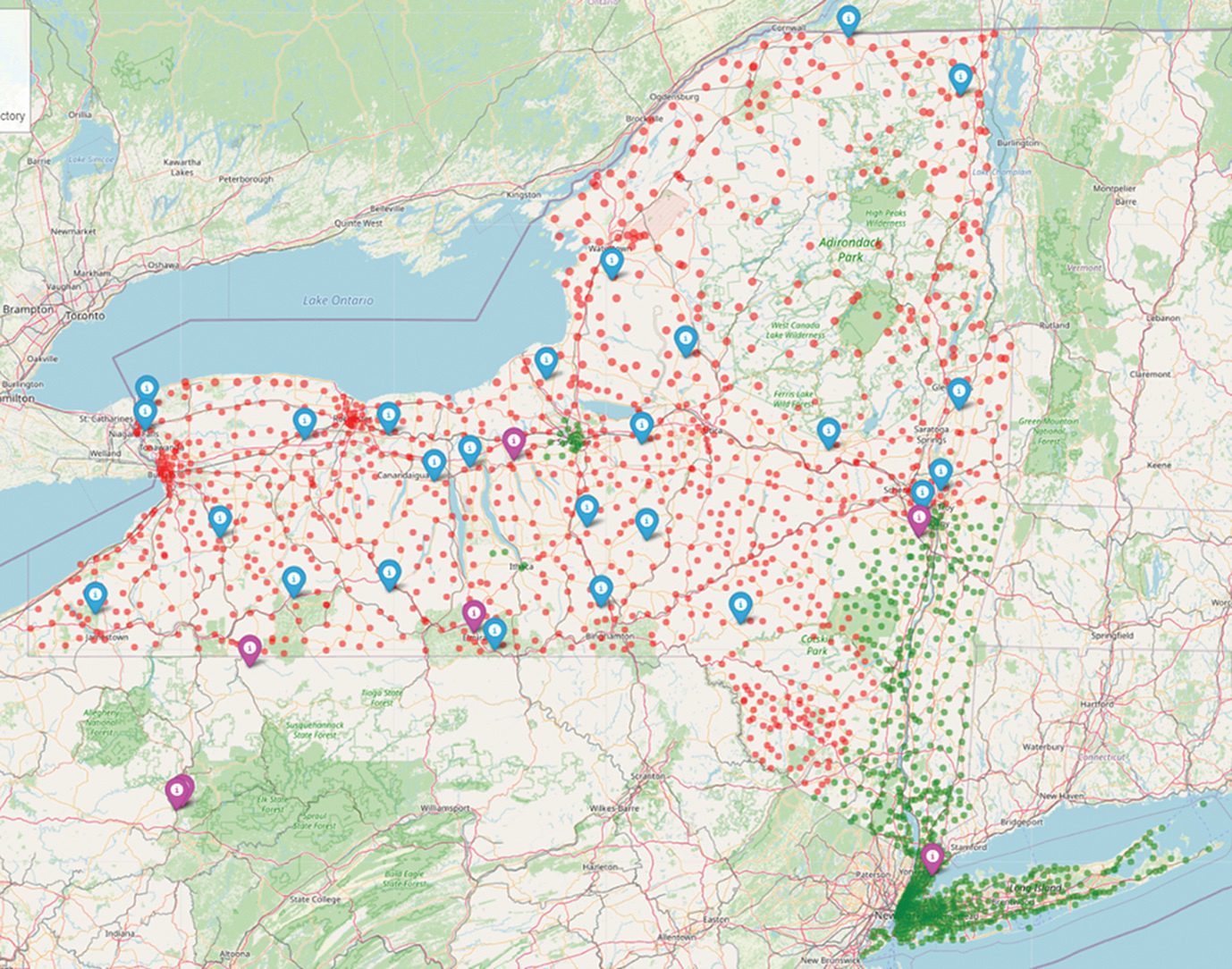
Figure 1. Green dots represent zip codes where recycling is economically favored, and red dots represent locations where landfilling is more affordable. Blue markers show landfill locations and purple markers represent factories.
Credit: Deniz Saadatpour
Though this model only accounts for purely economic factors and omits social factors, such as consumer opinion on recycling in each zone, the results align well with reports from the NYSDEC.
The model found that large population centers in Western New York, such as Buffalo, Rochester, and Syracuse, have no economic way to deal with their glass besides landfilling because, despite sufficient nearby MRFs, they lack an end market. Even in places where recycling would be expected, such as Long Island, the introduction of a new landfill can easily undercut the recycling rate due to the high cost of transportation.
Varying the input parameters further confirmed the impact that transportation costs have on the overall recycling rate in New York state (Table 1). A small decrease in transportation costs can lead to a significant increase in the feasibility of recycling by effectively increasing the radius of recyclability around factories. However, these costs are largely inflexible, and if anything, likely to increase in the future due to fuel and regulatory costs. Landfill tipping fees are likely to rise in coming years as well due to increased demand for landfilling and added regulation as landfill capacity decreases. An artificial increase in tipping fees for recyclable materials is likely infeasible, as it would require waste to be organized and would encounter significant political resistance.
Based on these findings, one way to improve glass recycling in New York state is to create more efficient MRFs that process glass at recovery rates higher than 70%. This approach has been a subject of ongoing research for the last few decades, and recent innovations are detailed in the next section.
Of course, not every MRF needs expensive sorting technology if they cannot guarantee a return on investment. This reality leads to another solution for improving glass recycling rates in New York state: creating a new glass sink. New end-use destinations, such as bottle redemption centers, or markets, such as construction filler materials, offer a double advantage, both by increasing the value of glass as demand rises in these alternative outlets as well as reducing transportation costs. Plus, if the new sink leverages newer technologies or high-quality waste streams, this improved efficiency will be reflected in lower processing costs.
Recent innovations in MRFs
Our models suggest that the largest gains in glass recycling rates can come from improving MRF efficiency. Specifically, finding ways to reduce contamination during single-stream recycling will be the key, as most reuse applications require cullet with low impurities.
Diverting more glass to bottle collection facilities separate from other municipal solid waste is the most straightforward way of reducing contamination. But within the MRF itself, several techniques exist to separate glass and nonglass materials (Figure 2).
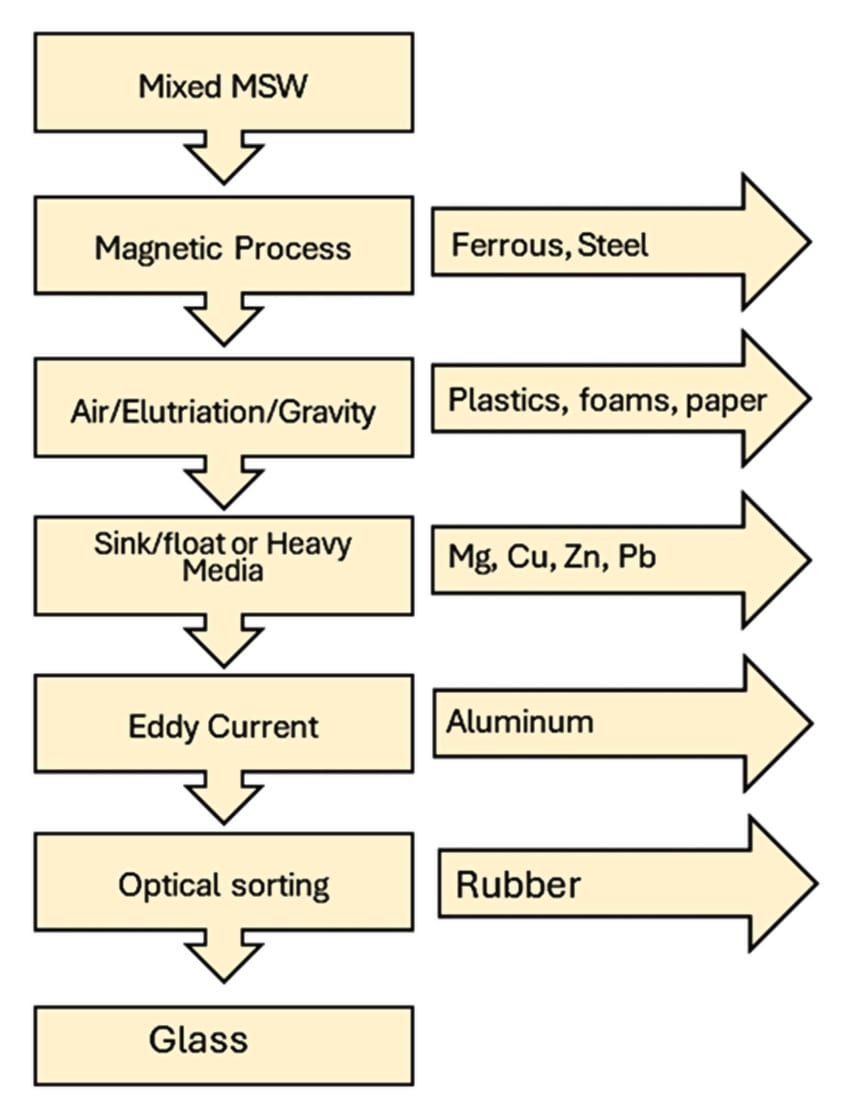
Figure 2. Schematic of a common scheme for glass separation from municipal solid waste streams.
Credit: Gabrielle Gaustad, Alfred University
Besides manually sorting by hand, most MRFs take advantage of gravity or air-based sorting techniques, such as windsifting, air-knives, elutriation, winnowing, and air columns. Conveyor belt systems often use suction to pull off lightweight materials, such as paper, plastic, low-density rubbers, and foams. For metallic products, a magnet or eddy current can separate ferrous and nonferrous metals from the mixed stream.
Recent decreases in both computing and sensor costs have improved adoption of a variety of optical and color sorting techniques,11 which can sort materials into streams with more than 95% purity. Computers analyze images of each scrap based on specified color ranges and then direct them to different feeds. Robotics also have potential in this area,12 but current high costs prevent widespread adoption.
Though many traditional end-use applications of glass require the material to be of high purity, some emerging markets for glass waste, such as aggregates for concrete, can tolerate low-quality glass cullet very well. The new demand that comes from developing these alternative markets can increase the glass waste’s value. Some of these emerging markets are described in the following section.
Emerging markets for recycled glass waste
New markets for recycled glass waste ideally will have several features, including the option for local use to reduce transportation costs, stability, and growth so they can accept large volumes of glass waste, and minimal requirements for additional processing or large remelt facilities to incorporate the glass back into the new product. Major emerging markets for waste glass are shown in Table 2 and described in more detail below.
Foam glass is one promising emerging market for waste glass. This porous construction material, which is created by heating a mixture of crushed or granulated glass and a blowing agent, such as carbon or limestone, is known for being lightweight and strong with good thermal and acoustic insulating properties.
Foam glass was first created almost 100 years ago.13 It has always been popular in Europe as a low-cost insulation material due to tighter environmental regulations and geographic restrictions, but it has only recently gained popularity in the U.S. Foam glass manufacturing can take even highly contaminated waste glass and create a quality end product with minimal additional additives. For example, the waste-based foam glass created by AeroAggregates (Eddystone, Pa.) was used to reconstruct a destroyed section of I-95 near Philadelphia, Pa. Though this end application of waste glass is unlikely to be circular, it provides an alternative avenue for glass waste that would otherwise be landfilled.14
Companies have started to leverage glass foams’ inherently high surface area to expand beyond the traditional application of insulation. For example, Growstone from Aeroaggregates is used as a high-performance soil aeration material. SilicaX (Spokane, Wash.), one of Alfred University’s partners, is working to convert waste glass into a foam aggregate with high resistance to oceanic corrosion (Figure 3a), which can be used to create improved concrete retaining walls. Large coupons of these materials are being produced and sank into the Long Island Sound (Figure 3b).
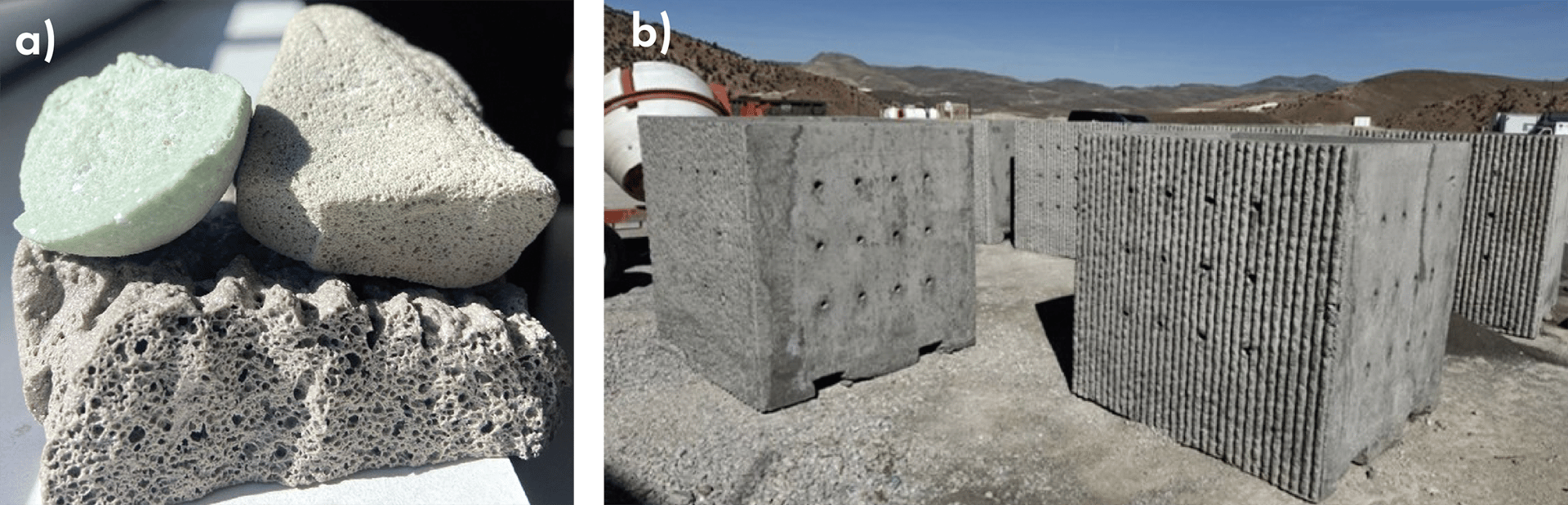
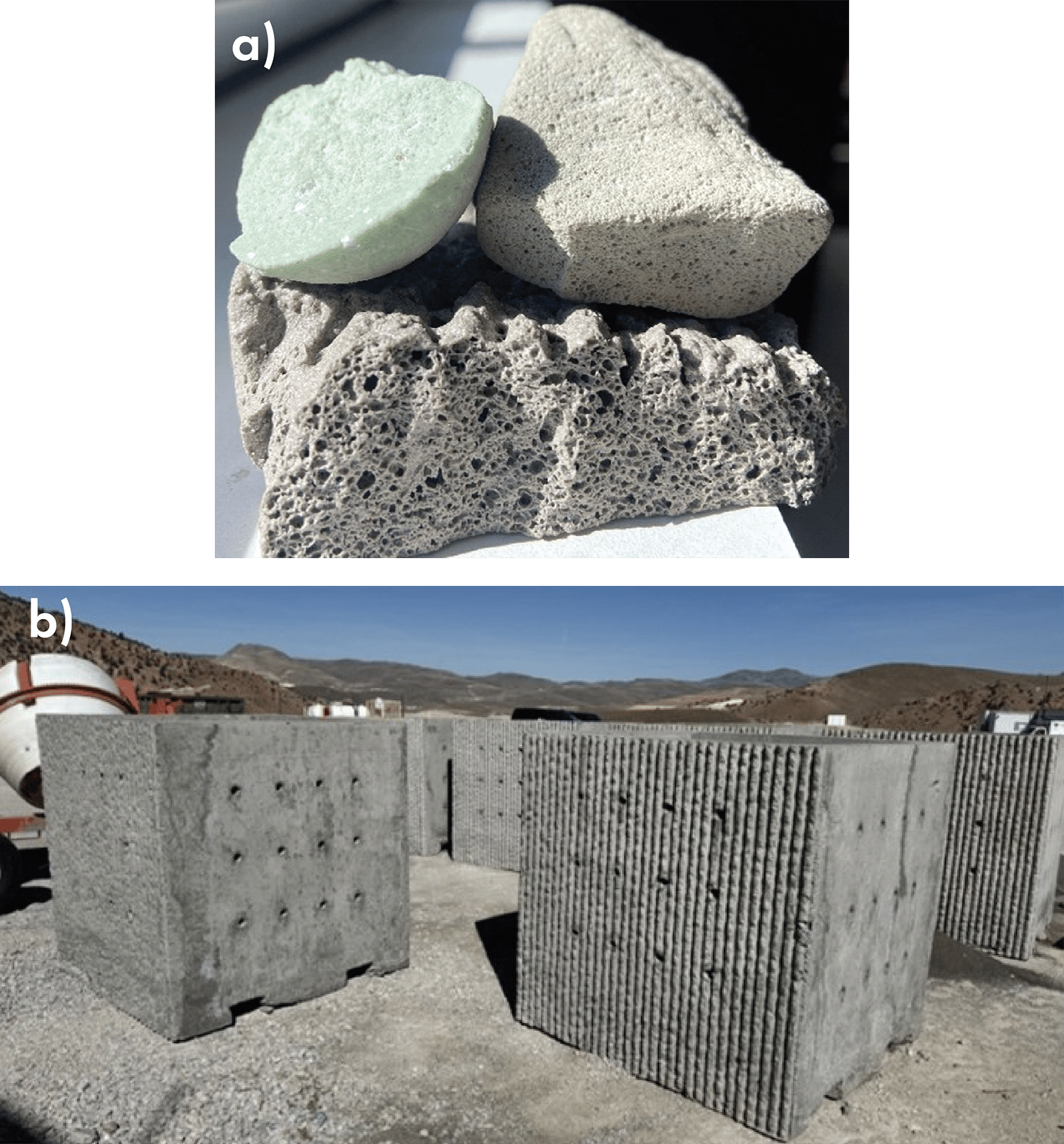
Figure 3.
a) Images of varying foam glass compositions. The green foam glass (left) is SilicaX’s aggregate, while the traditional grey foam glass (top) and experimental foam glass (bottom) were created by Collin Wilkinson’s group at Alfred University.
b) SilicaX coupons being produced for immersion in the Long Island Sound.
Credit: 3a) Collin Wilkinson; 3b) Philip Galland
Foam glass as water filtration has shown promise as well,15 but it competes with simple materials, such as woodchips or charcoal, for low-level filtration or activated carbon and zeolites for high-end filtration. It is also unclear how much processing is needed to make glass into good filtration media.
Waste glass can also serve as a pozzolan for cementitious materials.16 Concrete consists of cement, water, and aggregate, and replacing some of the cement with a supplementary cementitious material can help reduce concrete’s embodied carbon. Recent studies have found that, despite historical challenges with alkali silicate reaction, glass can be used as a supplementary cementitious material without any negative results, provided the particle size is fine enough.17 One company, SQ4D (Patchogue, N.Y.), has partnered with Alfred University to create specialized forms of these glass additives that can be used to 3D print homes. The only downside of this method is that much like with foam glass, these materials are unlikely to be circular.
Future opportunities
The European Union’s high rates of recycling demonstrate that an improved glass recycling system is achievable.18 However, geographic proximity of sources and sinks remains a major difference between the U.S. and European Union. In the U.S., destinations for recycled cullet have decreased from roughly 40 container glass companies with 112 plants in 1967 to about 17 companies operating 54 plants in 2018.19 Deploying additional infrastructure—whether collection facilities, processing facilities, or manufacturing centers that require glass cullet—will greatly impact U.S. glass recycling rates.
Because costs are a key driver in U.S. waste management, policy interventions would likely be beneficial as well. For example, in areas with higher landfill tipping fees, recycling rates are typically higher.10 Strategies aimed at consumers may also improve the quantity and quality of recyclables put in bins destined for MRFs and reduce contamination. These strategies may include curbside feedback to consumers,20 enhanced labeling of receptacles,21 and general consumer education aimed at understanding challenges around processing at the MRFs.
Similarly, strategically employed economic development incentive programs would likely also improve glass recycling rates. These initiatives may include programs that fund capital equipment improvements at waste processing facilities or provide incentive programs for collection. Also, states that have passed bottle deposit legislation, or “bottle bills,” typically have higher return rates for glass and plastic bottles, and some states are exploring expansion of their bottle bills to include additional container types, such as wine and liquor bottles.
In the end, it will take close collaboration and communication between consumers, researchers, manufacturing, policymakers, and the waste management industry to drive increased glass recycling rates in the United States.
SIDEBAR
Photovoltaic glasses and challenges to end-of-life disposal
Glass recycled from end-of-life photovoltaic (PV) panels will become increasingly significant in coming years. However, three major factors differentiate PV waste glass from traditional consumer waste glass: availability, composition, and separability.
Availability
At present, PV waste glass accounts for a very small quantity of overall glass waste. This makes the use of recycled cullet from such material difficult, as supply remains low and inconsistent. But as more panels begin to fail around their expected lifetime of 25–30 years, PV waste will become increasingly relevant.
As installed PV capacity quickly expands, waste material generated by end-of-life modules will naturally follow, increasing cumulatively to a projected 7.5–10 million metric tons by 2050 for the United States alone and 60–78 million metric tons globally.a This increase equates to an additional 0.5–1 million metric tons of waste per year. For context, the total amount of recycled glass in the United States was just 2.8 million metric tons in 2018.b
Composition
Most modern solar panels are crystalline silicon covered with a patterned, tempered, low-iron (~120 ppm) soda-lime silicate glass, though thin-film cadmium telluride panels are gaining market acceptance. In principle, the consistency and clarity of PV waste glass cuts the cost of high-purity raw materials and eliminates the need for sorting of clean cullet by color, thus improving the marketability and price of such material.c
For example, whereas fiberglass insulation production requires (comparatively) little control over the color or iron content of incoming cullet, architectural glass manufacturers require cullet with low iron content and negligible coloration. If recycled PV glass meets the more stringent requirements of the architectural glass manufacturers, that glass would command a significantly higher price than mixed-color glass with high impurity content. Furthermore, as the amount of available material increases, this glass might also be able to be directly reused in the production of new solar cell cover glass.
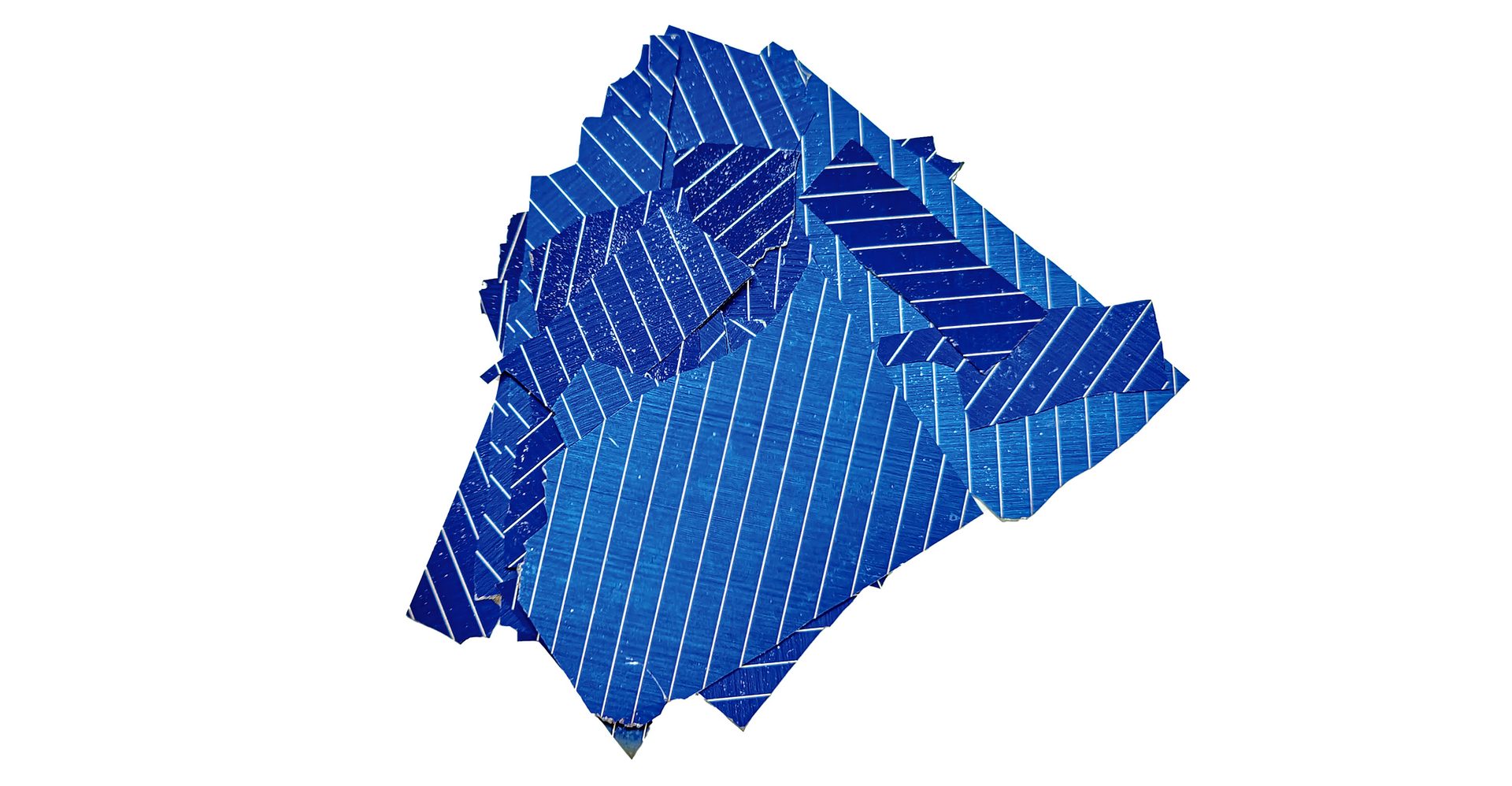
Example of clean pieces of silicon extracted from discarded solar panels using thermal delamination.
Credit: Arron Potter
Another benefit of having high-purity cullet available is furnace longevity. Raw batch materials are corrosive to furnace refractory, so introducing cullet to flat glass and specialty glass production, especially in locales where cullet usage is low, could provide additional value.
Unfortunately, most currently installed PV glasses contain antimony as a fining agent and decolorant.d Antimony oxidizes the small amount of residual iron content to improve transmission of the near-infrared wavelengths absorbed by silicon. For PV glass sheets produced by rolling, antimony is an effective solution to improve performance of the glass. If recycled into glass produced on a float line, however, the antimony can enter the tin bath and cause deleterious interactions.
Thankfully, with the advent of PV technologies that do not require high transparency in the near-infrared range, such as the cadmium telluride thin films mentioned earlier, new glass will not need to contain antimony and so this danger can be avoided.
Separability
In practice, PV waste glass is difficult to remove from the other solar cell components without significant contamination.e A crystalline silicon solar cell is composed of five major layers, from bottom to top: plastic backing sheet, usually polyvinyl fluoride (PVF); a crosslinked ethyl vinyl acetate (EVA) encapsulant; the silicon wafer itself; another layer of the same EVA encapsulant; and finally, the glass cover sheet. The silicon wafer is coated with an aluminum rear conductor, silicon nitride surface coating, and a screen-printed silver grid, with soldered copper interconnects between cells.
The efficacy of EVA as an encapsulant creates some difficulty in delaminating the solar cells, which tend to swell under solvent dissolution or thermal delamination, the two major avenues being pursued for intact delamination of solar cells. This behavior means that most techniques for recycling PV glass are either costly or result in cullet contaminated with pieces of the other materials present in the system, if not also residual organic content.f
These contaminants can affect reuse in multiple ways. For example, silver and copper are strong colorants in soda-lime glass, while lead and tin pose major environmental and health hazards. These metals also can pool at the bottom of furnaces and cause significant damage. Additionally, if the fluorinated polymer backing sheet remains in the cullet, its decomposition produces hydrofluoric acid fumes.g As a result, the separability with current technology remains low and as such the value of PV scrap is low.
Recently, solar panel recycling methods were reviewed by Crespo et al.h They compared the three leading proposed methods to recycle panels: thermal delamination, mechanical separation, and solvents. All three methods faced major financial or technical challenges, but thermal delamination appeared to show promise. However, any technologically viable approach remains limited by the purity, and therefore value, of the materials recovered.
Resources
a Weckend, S. et al., “End of life management: Solar photovoltaic panels,” International Renewable Energy Agency, 2016.
b “Advancing sustainable materials management: 2018 fact sheet,” United States Environmental Protection Agency: Washington, D.C., 2020.
c Deng, R. et al., “A techno-economic review of silicon photovoltaic module recycling,” Renew. Sustain. Energy Rev. 2019, 109: 532–550.
d European Solar PV Industry Alliance, “Recommendations Paper Series II: Addressing uncertain antimony content in solar glass for recycling,” April 2023.
e Tao, M. et al., “Major challenges and opportunities in silicon solar module recycling,” Prog. Photovolt. 2020, 28(10): 1077–1088.
f Xu, Y. et al., “Global status of recycling waste solar panels: A review,” Waste Manage. 2018, 75: 450–458.
g Chowdhury, Md. S. et al., “An overview of solar photovoltaic panels’ end-of-life material recycling,” Energy Strateg. Rev. 2020, 27: 100431.
h Crespo, B. et al., “Technoeconomic feasibility of photovoltaic recycling,” Int. J. Appl. Glass Sci. 2024, In press.
About the authors:
Collin Wilkinson is assistant professor and Arron Potter is postdoctoral researcher in the Department of Glass Science at Alfred University (Alfred, N.Y.). Gabrielle Gaustad is dean of the Inamori School of Engineering at Alfred University. Contact Collin Wilkinson at wilkinsonc@alfred.edu.